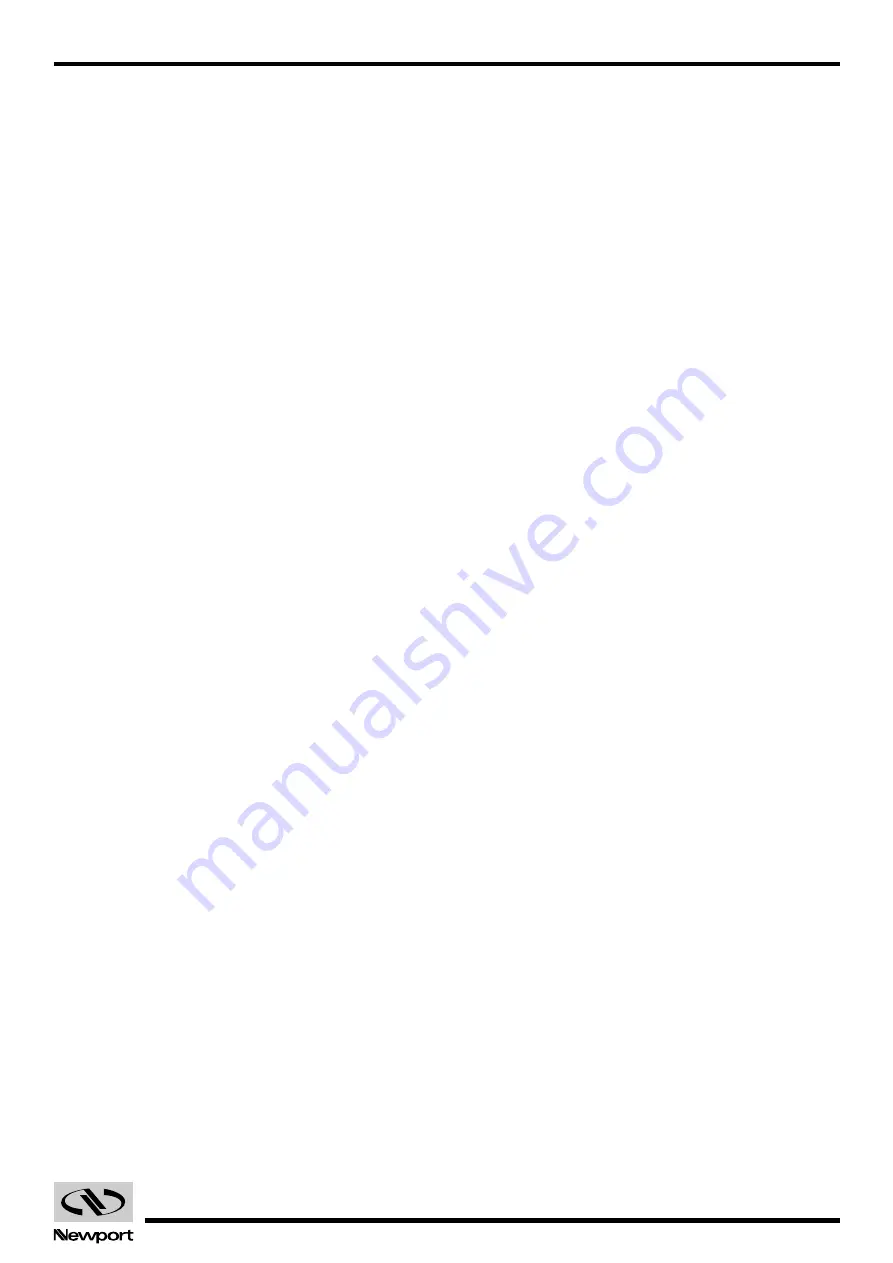
1.9
EDH0162En1040 – 06/99
MM4005
Introduction
1.3.1
Features
Many advanced features make the MM4005 the preferred choice for preci-
sion applications:
• Integrated controller and driver design is more cost effective and a
space saving solution.
• Compact, rack-mountable or bench-top enclosure.
• Allows any combination of motor types (stepper and DC) and sizes.
• Supports closed-loop operation of stepper motors.
• Feed-forward servo algorithm for smooth and precise motion.
• Velocity feedback motor drivers for best motion performance.
• Advanced multi-axis synchronization (linear interpolation).
• Powerful command set for the most demanding applications.
• Motion program storage and management capability.
• Advanced motion programming capabilities with up to 100 nested loops
and complex digital and analog I/O functions.
• User-selectable displacement units.
• User-settable compensation for accuracy and backlash errors.
• Full-featured front panel with bright fluorescent backlit display, numer-
ic/jog keypad, context-sensitive function keys, full motion selection and
control capability and motion program creation and editing capability.
• Multilingual display capability — English or French.
1.3.2
Specifications
1.3.2.1
Function
• Integrated motion controller and driver.
1.3.2.2
Number of motion axes
• 1 to 4, in any combination or order of stepper and DC motors.
1.3.2.3
Trajectory type
• Non-synchronized motion.
• Multi-axis synchronized motion (linear interpolation).
• S-Curve or Trapezoidal velocity profile for non-synchronized and syn-
chronized motion. The default configuration is S-Curve velocity profile.
1.3.2.4
Motion device compatibility
• Entire family of motorized motion devices, using ether stepper or DC
motors.
1.3.2.5
CPU type
• 5x86/100 Processor.
1.3.2.6
DC motor control
• 16 bit DAC resolution.
• 10 MHz maximum encoder input frequency.
• PID with velocity feed-forward servo loop.
• 0.3 ms digital servo cycle.
1.3.2.7
Stepper motor control
• 1 MHz maximum pulse rate.
• Full, half and mini step capability.
• Open or closed-loop operation.
• PID with velocity feed-forward closed-loop mode.
• 0.3 ms digital servo cycle.
Artisan Technology Group - Quality Instrumentation ... Guaranteed | (888) 88-SOURCE | www.artisantg.com