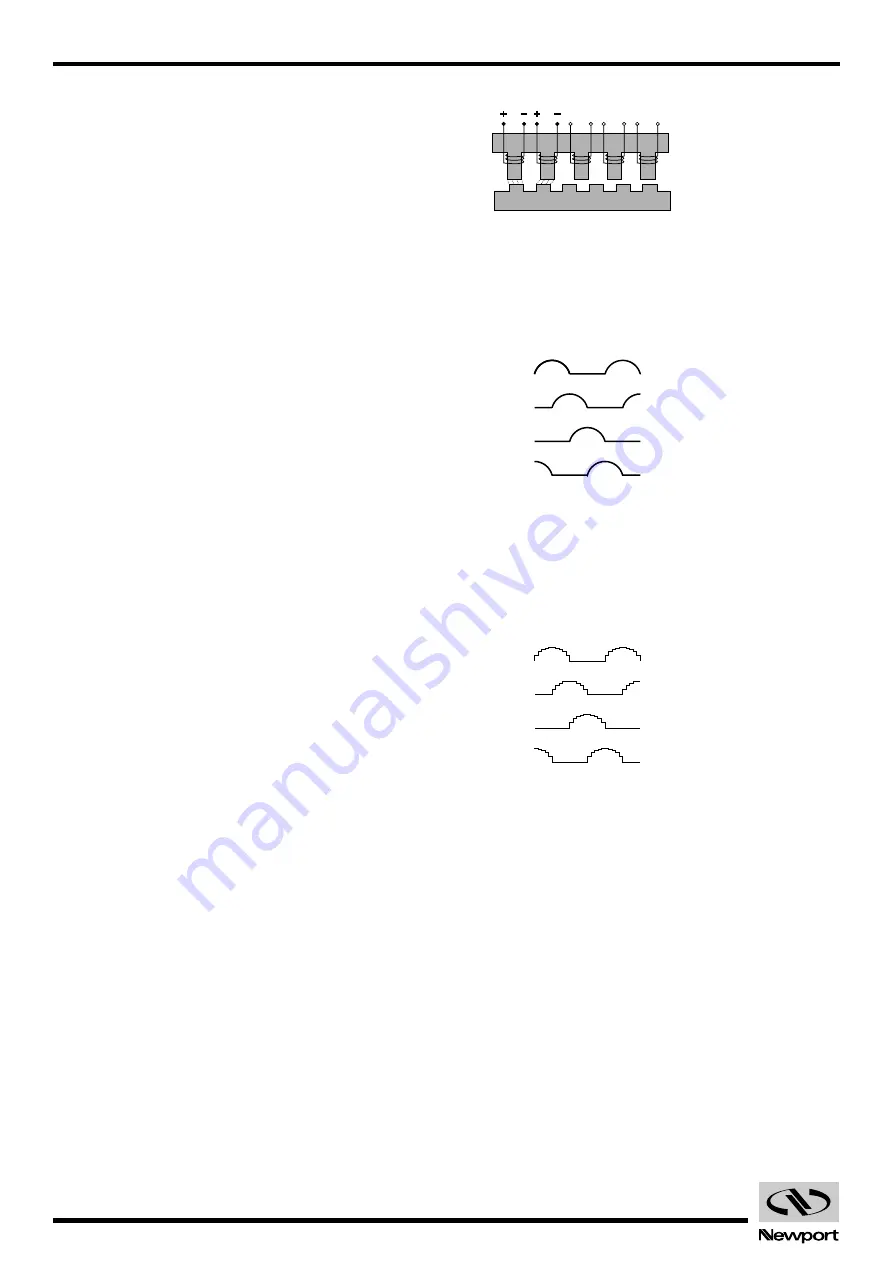
EDH0162En1040 – 06/99
4.26
MM4005
Motion Control Tutorial
Fig. 4.36
— Energizing Two Phases with Different Intensities.
The conclusion is that, varying the ratio between the currents of the two
phases, we can position the rotor anywhere between the two full step loca-
tions. To do so, we need to drive the motor with analog signals, similar to
Fig. 4.37.
Fig. 4.37
— Timing Diagram, Continuous Motion (Ideal).
But a stepper motor should be stepping. The controller needs to move it in
certain known increments. The solution is to take the half-sine waves and
digitize them so that for every step command, the currents change to some
new pre-defined levels, causing the motor to advance one small step (Fig.
4.38).
Fig. 4.38
— Timing Diagram, Mini-Stepping.
This driving method is called mini-stepping or micro-stepping. For each
step command, the motor will move only a fraction of the full step. Motion
steps are smaller so the motion resolution is increased and the motion rip-
ple (noise) is decreased.
The MM4005’s drivers use the mini-stepping technique to divide the full
step in ten mini-steps, increasing the motor’s resolution by a factor of 10.
However, mini-stepping comes at a price. First, the driver electronics are
significantly more complicated. Secondly, the holding torque for one step
is reduced by the mini-stepping factor. In other words, for a x10 mini-step-
ping, it takes only 1/10 of the full-step holding torque to cause the motor to
have a positioning error equivalent to one step (a mini-step).
To clarify a little what this means, lets take a look at the torque produced
by a stepper motor. For simplicity, lets consider the case of a single phase
being energized (Fig. 4.39).
A
B
C
D
A
B
C
D
A
B
C
D
A
Artisan Technology Group - Quality Instrumentation ... Guaranteed | (888) 88-SOURCE | www.artisantg.com