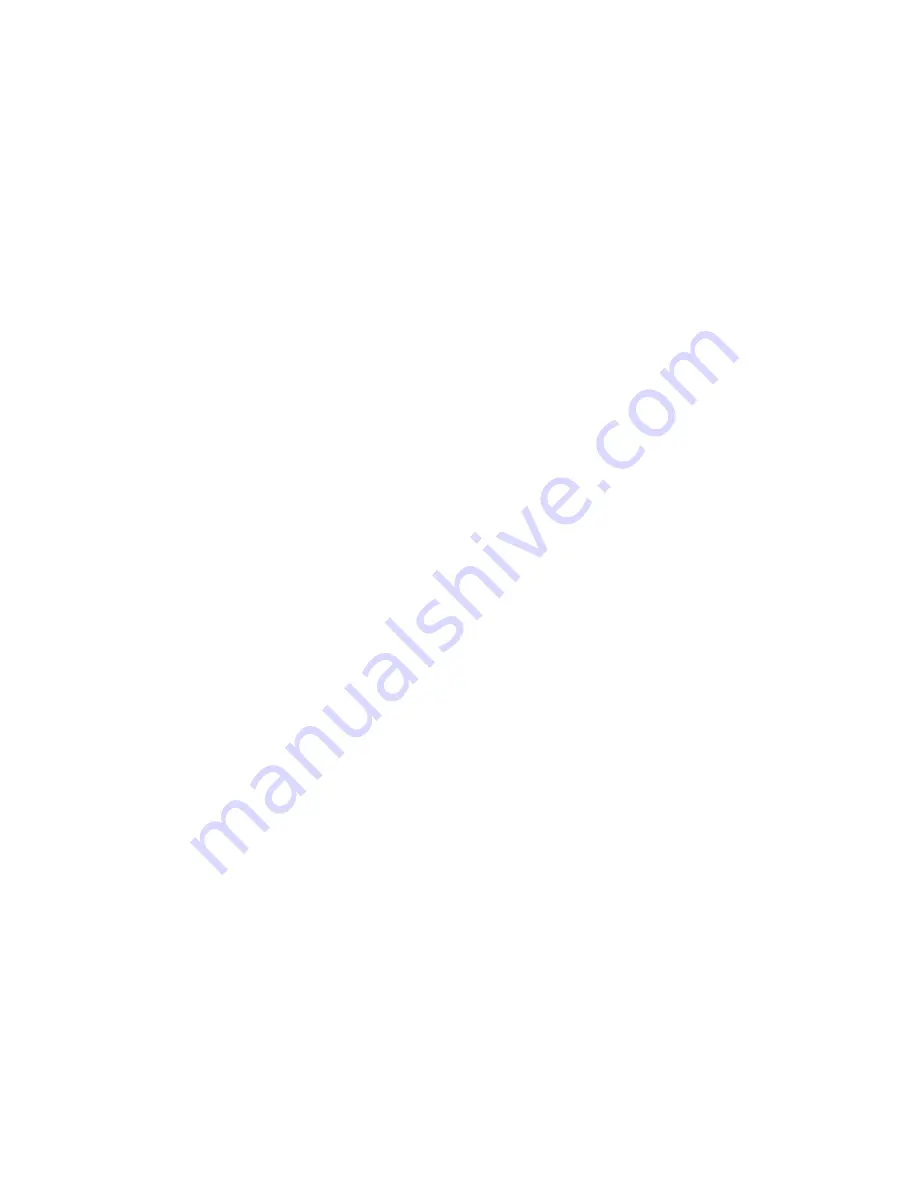
Safety Practices Before Operating the System
MTS Exceed™ 22 Series Product Information
Safety
11
Getting First Aid
Supplies Ready
Accidents may occur even if you are very careful. Please properly arrange the
schedule of operators, to ensure that there will always be properly trained
personnel in the vicinity who can carry out first aids. Also, post the local
emergency contact information within the sight of system operators.
Knowing Potential
Crush Positions
Know potential crush positions on the system, and keep personnel and equipment
away from these areas.
Understanding
Electrical Hazards
Minimize risks of electrical shocks after the system is powered on. Wear
insulated coveralls and use fully insulated tools for any electrical operations, and
avoid touching bare wires or switch contacts. Turn off the power if possible
before operating or approaching any electrical system components. Abide by
precautions for other high-voltage machinery.
Safe Distance of
Irrelevant Personnel
Irrelevant personnel should be kept a safe distance from the equipment. When
conducting tests, do not let any irrelevant person to touch the specimen or
equipment.
Wearing
Appropriate Outfits
Do not wear a tie, shop aprons, loose clothing, or jewellery, or let the long hair
loose, to avoid them being stuck into equipment, thereby causing personal
injuries. Take off your loose clothing or jewellery, or tie your hair up.
Emptying
Combustible Liquids
in Specimen
Before installing the container or component, empty combustible liquids inside
the container or component. Where necessary, replace combustible liquids with
non-flammable ones, to maintain an appropriate proportion of weight and
balance.
Checking Bolt
Ratings and
Torques
In order to ensure product reliability, the torque of fasteners (such as bolts and
connecting rods) in MTS systems must comply with requirements specified. Due
to high strengths and high pressures of MTS testing equipment, the actual torque
higher than or lower than the ratings could lead to dangers.
In rare cases, failures may occur even when fasteners are correctly installed.
Faults often occur during tightening, and may even occur several days later. Such
faults may result in fasteners springing off at high speed. As a result, on-site
personnel are better to avoid being on a straight line with or under assemblies
that contain large or long fasteners.
Keeping
Indoor Area Clean
Keep the floor of the work area clean. Do not leave any tools, facilities, or other
items unrelated to the test on the floor, system or accessories.
Protecting Hoses
and Cables
Avoid cables to be overheated, as they can cause the hardening and, ultimately,
failures of cables. Ensure that appropriate strain relief apparatus is installed near
cables and plugs of connectors. Do not use plugs of connectors to release strain.
Avoid all system hoses and cables to get in touch with sharp or rough objects, as
they may cause damages to hoses or cables. It is forbidden to stampede or use
heavy objects to press against hoses or cables. During considerations of system
layout and cabling, cables and hoses should be placed away from areas that may
cause damages to them.
When you need to remove the hydraulic pipe due to maintenance of the
equipment or replacement of test parts (such as replacement of hydraulic
clamps), ensure to tightly cover the two ends of the pipe to prevent oil spills.
Summary of Contents for Exceed 22 Series
Page 54: ...MTS Exceed 22 Series Product Information 54 Shortcut Operations Operation...
Page 58: ...MTS Exceed 22 Series Product Information 58 Troubleshooting...
Page 60: ...MTS Exceed 22 Series Product Information 60 Equipment Disassembly...
Page 67: ......
Page 68: ...m MTS Systems Corporation http www mts com en Global index asp ISO 9001 Certified QMS...