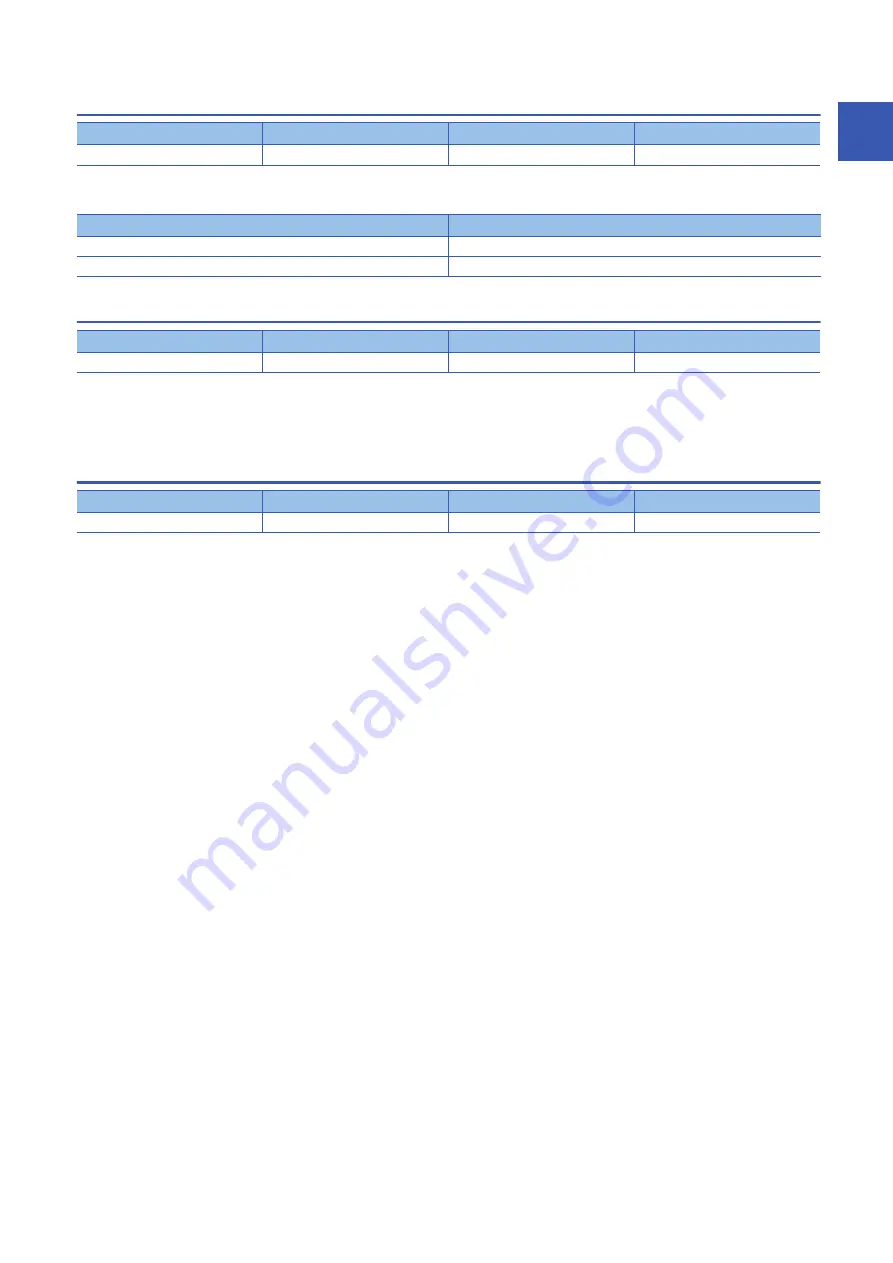
1 SERVO PARAMETER DETAILS
1.3 Gain/filter setting servo parameters group ([Pr. PB_ _ ])
33
1
[Pr. PB11_Speed differential compensation (VDC)]
Set the differential compensation.
The enabling conditions vary depending on the setting value in [Pr. PB24.1 PI-PID switching control selection].
[Pr. PB12_Overshoot amount compensation (OVA)]
Set a dynamic friction torque in percentage to the rated torque at servo motor rated speed. Alternatively, set a percentage of
dynamic friction force against the continuous thrust at linear servo motor rated speed.
If the response level is too low or if the torque/thrust is limited, the efficiency of the servo parameter may decrease.
[Pr. PB13_Machine resonance suppression filter 1 (NH1)]
Set the notch frequency of the machine resonance suppression filter 1.
When [Pr. PA08.0 Gain adjustment mode selection] is set to "5" (quick tuning mode), the setting value of this servo parameter
reflects the adjustment result of quick tuning.
When [Pr. PB01.0 Filter tuning mode selection] is set to "1" (automatic setting), the values obtained from adaptive tuning are
applied to the setting value of this servo parameter.
When [Pr. PB01.0] is set to "2" (manual setting), set the notch frequency with this servo parameter.
Initial value
Setting range
Setting method
Ver.
980
0 to 1000
Each axis
C4
[Pr. PB24.1]
The enabling conditions for this servo parameter
"0" (switching is enabled by the PID switching signal from the controller)
Enabled by turning on the PID switching signal from the controller
"3" (Continuous PID control (proportional control) enabled)
Always enabled
Initial value
Setting range
Setting method
Ver.
0 [%]
0 to 100
Each axis
C4
Initial value
Setting range
Setting method
Ver.
4500 [Hz]
10 to 9000
Each axis
C4
Summary of Contents for MR-J5-B
Page 2: ......
Page 153: ...4 SERVO PARAMETER SETTING METHOD 4 2 Controller 151 4 MEMO ...
Page 157: ......