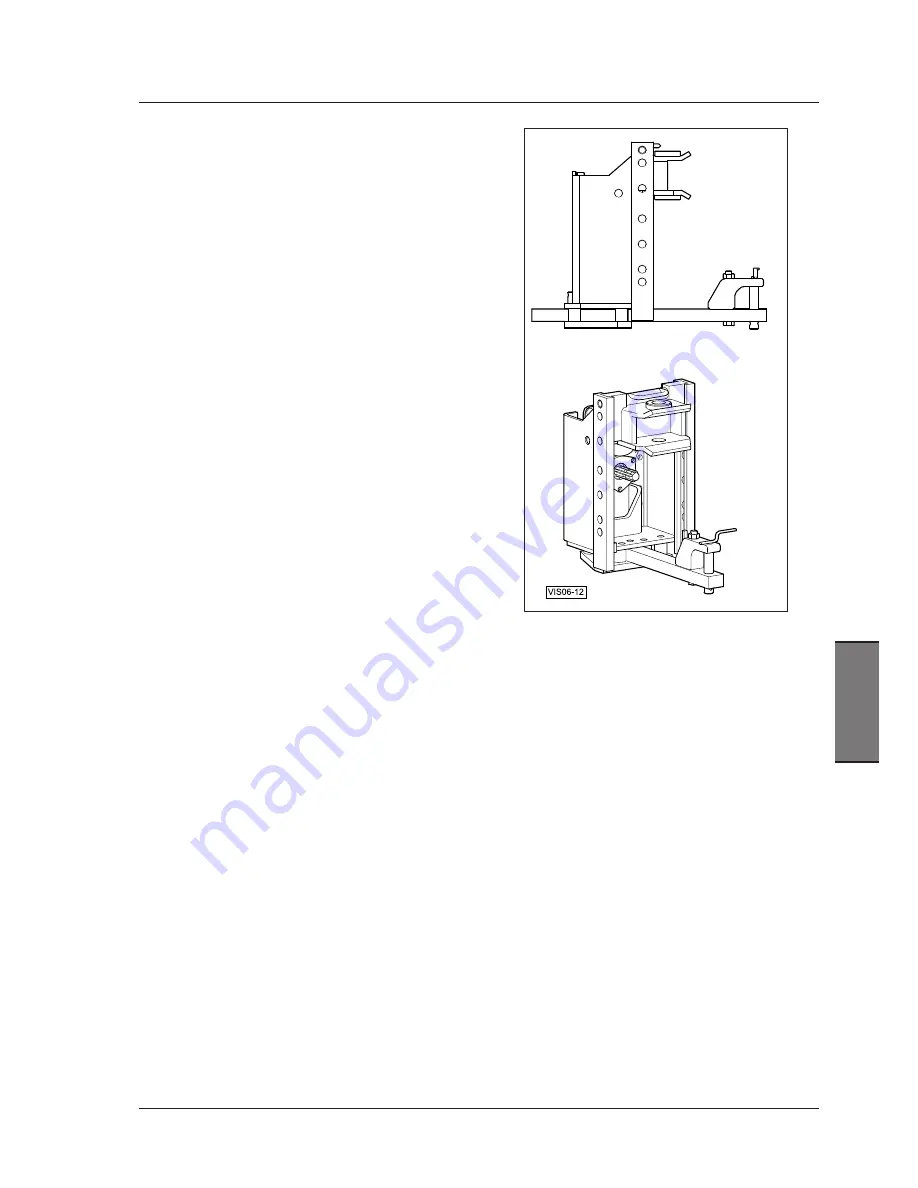
141
Operation
5
Standard sliding rear tow hooks, adjustable in
height - Italian market.
- CUNA ‘C’ tow hook (for the Italian market).
- CUNA ‘D2’ tow hook (trailer hydraulic brakes) (for the
Italian market).
- CUNA C hook and CUNA drawbar, Class A (for the
Italian market)
- CUNA D2 hook (hydraulic trailer brake) and CUNA
drawbar, Class A (for the Italian market)
Standard sliding rear tow hook, adjustable in
height - EEC market
- EEC hook, not automatic
- EEC hook, automatic
- EEC hook, not automatic and EEC drawbar.
- EEC hook, not automatic and EEC drawbar.
- EEC Drawbar
Summary of Contents for X60 Series
Page 39: ...39 Controls Cab 3 Section 3 Controls Cab...
Page 61: ...61 Instruments and Programming 4 Section 4 Instruments and Programming...
Page 90: ...90 Instruments and Programming This page has been left blank intentionally...
Page 91: ...91 Operation 5 Section 5 Operation...
Page 151: ...149 Tyres Wheels Ballasting 6 Section 6 Tyres Wheels Ballasting...
Page 168: ...166 Tyres Wheels Ballasting This page has been left blank intentionally...
Page 169: ...167 Maintenance 7 Section 7 Maintenance...
Page 229: ...Electrical system 227 8 Section 8 Electrical system...
Page 242: ...Electrical system 240 Page left intentionally blankf...
Page 256: ...Technical specifications 254 This page has been left blank intentionally...
Page 262: ...260 Alphabetical index...