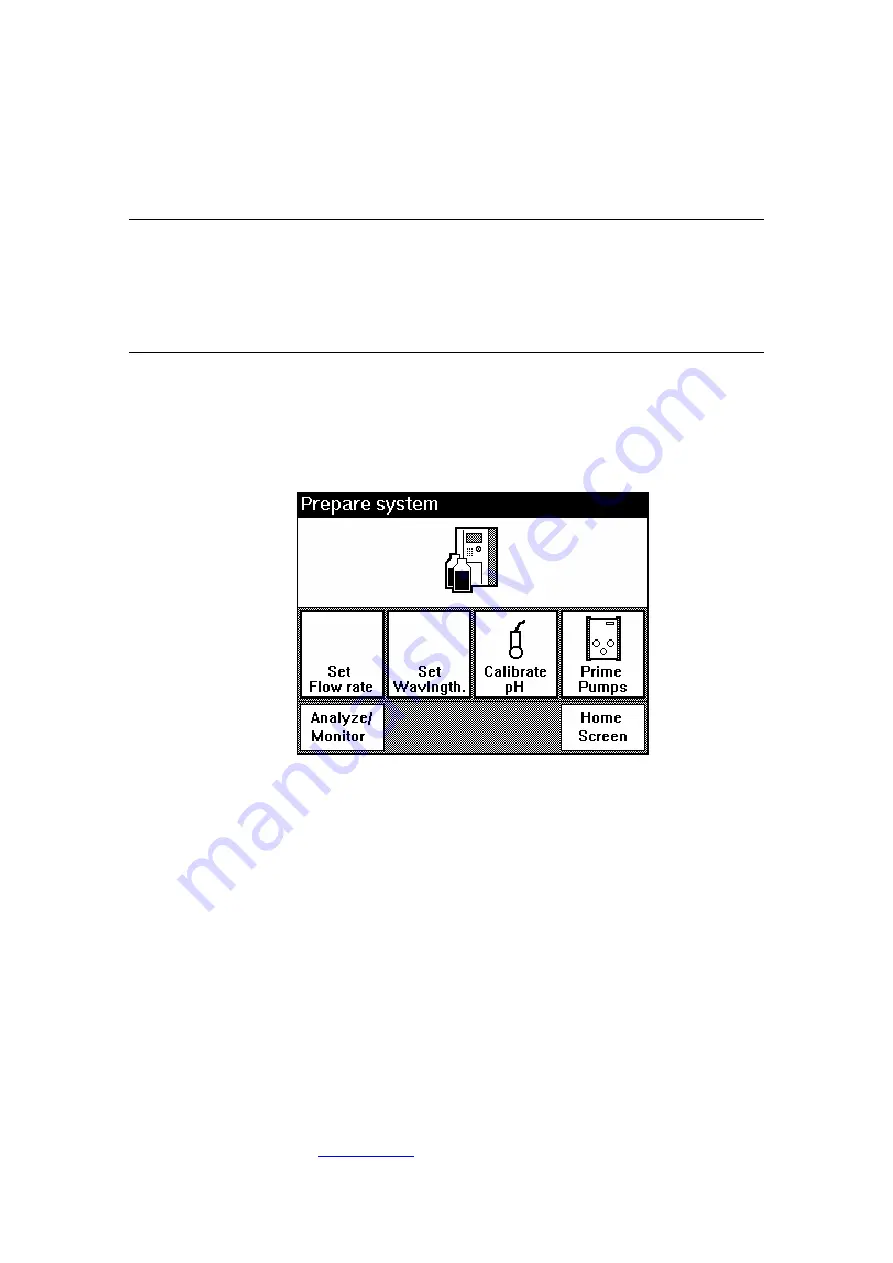
4-2
Matec Applied Sciences
56 Hudson St., Northborough, MA 01532 Ph: (508) 393-0155 Fax: (508) 393-5476
www.matec.com
e-mail: [email protected]
4 Operating the CHDF 2000
This chapter describes how to perform normal CHDF 2000 operations.
4.1 Priming the Pump
Prime the pump to remove air bubbles from the eluant supply tubes or to purge eluant from the
system before you use new eluant.
To prime a pump
1.
From the Home screen, choose Prepare system. The Prepare System screen appears as
shown in Figure 4.1.
Figure 4.1 The Prepare System Screen
2.
Choose Prime pump. The Prepare System...Prime Pump screen appears (Figure 4.2).
Artisan Technology Group - Quality Instrumentation ... Guaranteed | (888) 88-SOURCE | www.artisantg.com