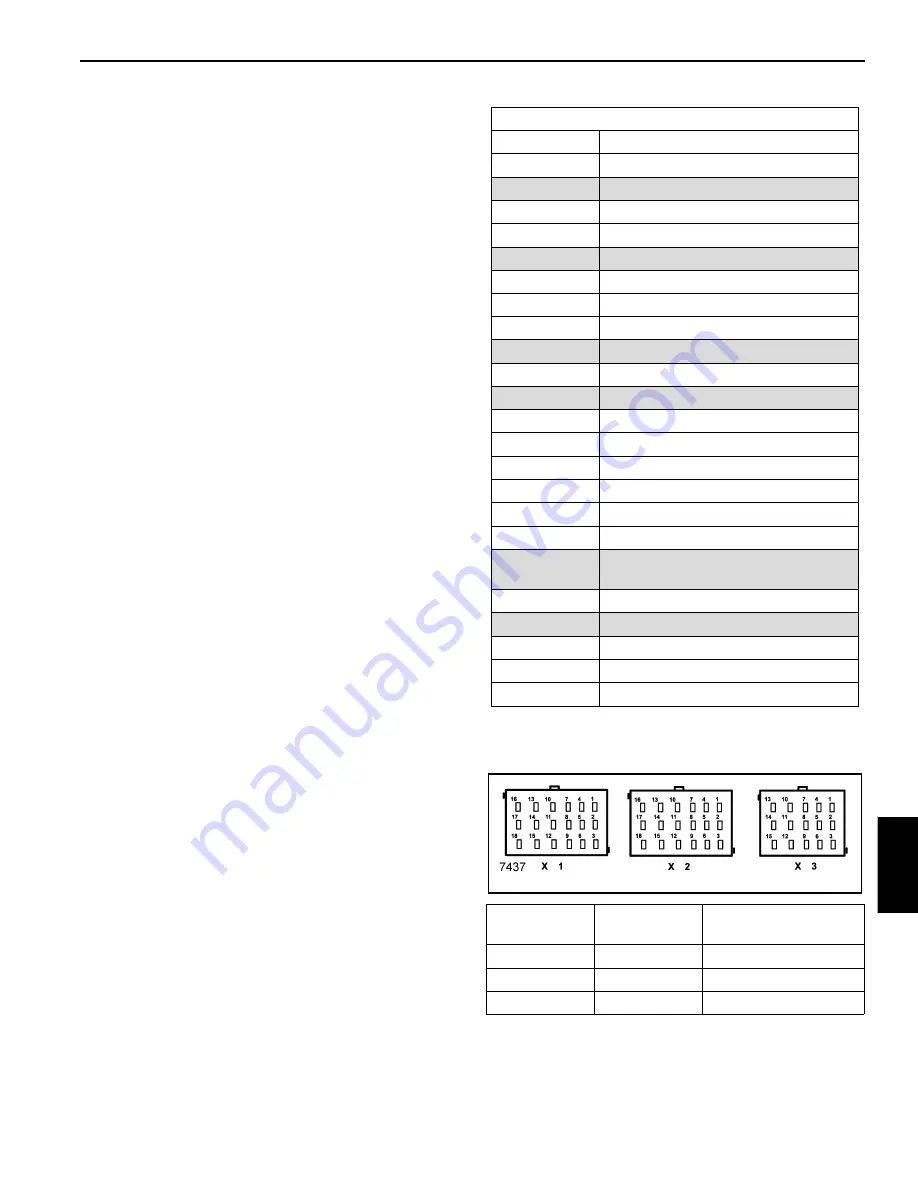
Grove
Published 01-14-2021 Control # 707-01
8-63
TMS9000-2 SERVICE MANUAL
CARRIER
8
commonly referred to as “event history.” When an active
trouble code is cleared, the ECU stores it in the event history
memory as an inactive trouble code.
Using blink codes, the technician may review all inactive
trouble codes stored on the ECU. The ABS indicator lamp
will display inactive diagnostic blink codes when the
diagnostic blink code switch is depressed and released two
times. See Active or Inactive Diagnostic Trouble Codes for
the index showing trouble codes and the troubleshooting
guide page to read for help. Inactive trouble codes, and
event history, may be retrieved and cleared by using a hand-
held or PC-based diagnostic tool.
Clearing Active Diagnostic Trouble Codes
The ECU will clear active trouble codes when the diagnostic
blink code switch is depressed and released three times.
Dynamometer Test Mode
The Dynamometer Test Mode is used to disable ATC when
needed (e.g. when performing any vehicle maintenance
where the wheels are lifted off the ground and moving,
including dyno testing). This mode is not reset by power off,
power on, cycling. Instead a hand-held or PC-based
diagnostic tool must be used to change the setting.
Alternatively, depressing and releasing the blink code switch
three times will cause the ECU to exit the blink code mode.
Reconfigure ECU Mode
NOTE:
To enter the Reconfiguration Mode, the blink code
switch must be held in before the application of
ignition power. Once the power is supplied, the
switch is released and then pressed seven times.
System Configuration Check Mode
The ABS indicator lamp will display system configuration
information when the diagnostic blink code switch is
depressed and released four times. The lamp will blink out
configuration information codes using the patterns listed in
the System Configuration Check table, shaded rows indicate
proper code: “2-6-6-1-5-1”. In this mode the ECU tells the
technician, by means of a series of six blink codes, the type
of ABS system that the ECU has been set up to expect.
EC-60 Controller Wire Harness Connector Pin
Assignments
System Configuration Check
1st Number
System Power
1
12 Volts
2
24 Volts
2nd Number
Wheel Speed Sensors
4
4 Sensors
6
6 Sensors
3rd Number
Pressure Modulator Valves
4
4 Modulators
5
5 Modulators
6
6 Modulators
4th Number
ABS Configuration
1
4S/4M or 6S/6M
2
6S/4M
3
6S/5M
5th Number
Traction Control Configuration
2
No ATC
3
ATC Engine Control Only
4
ATC Brake Control Only
5
Full ATC (Engine Control and Brake
Control)
6th Number
Retarder Configuration
1
No Retarder
2
J1939 Retarder
3
Retarder Relay
4
J1939 Retarder, Retarder Relay
Conn.
Designation
Number of
Contacts
Deutsch Part Number
X1
15
DT16-15SA-K003
X2
18
DT16-18SB-K004
X3
18
DT16-18SC-K004
FIGURE 8-66
Fo
r
Reference
Only