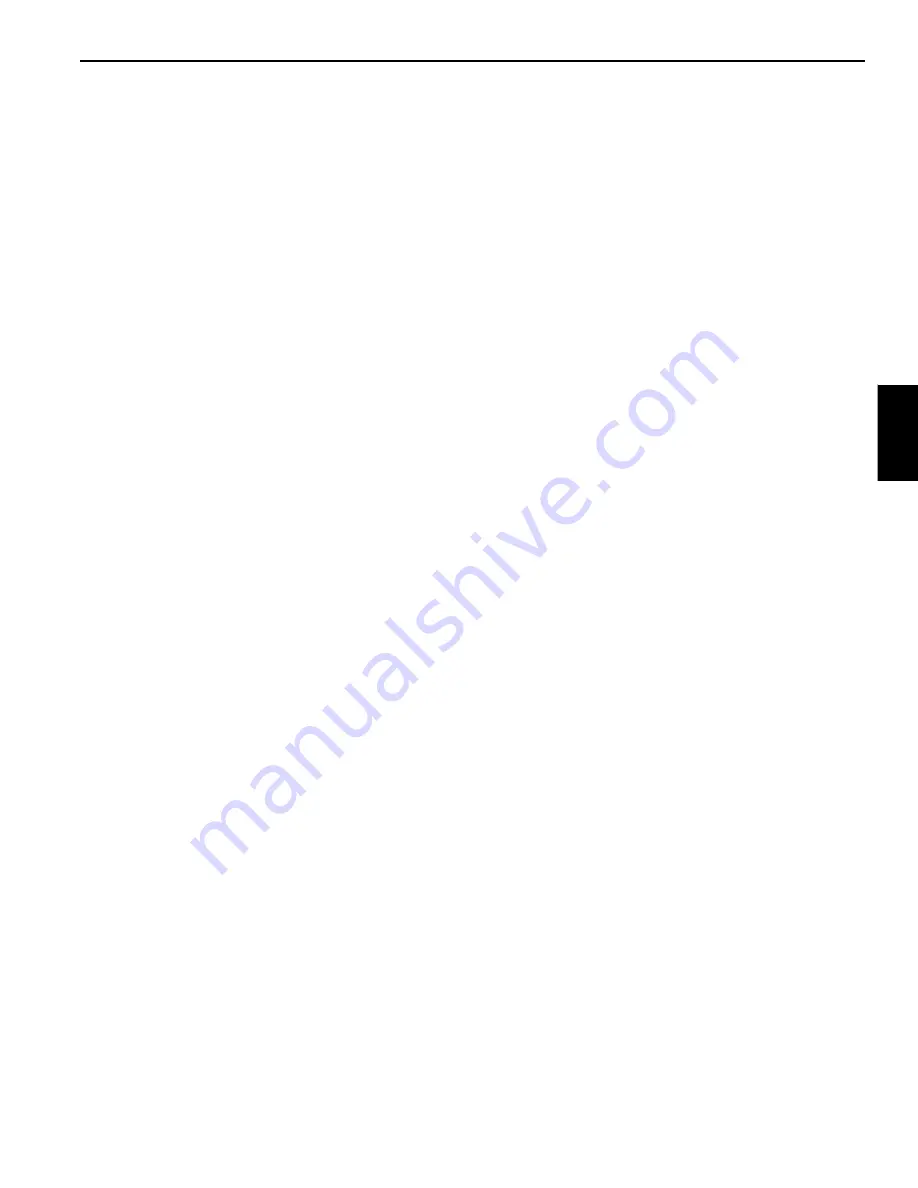
Grove
Published 01-14-2021 Control # 707-01
4-7
TMS9000-2 SERVICE MANUAL
SUPERSTRUCTURE
4
Brake Test Procedure
These planetary hoists have a spring applied, hydraulically
released, multiple disc brake inside the hoist housing. This
brake holds a suspended load when the directional control
valve is in neutral, or when hydraulic power is lost. A load
cannot be lifted or lowered, however, without applying
hydraulic pressure to the release port and releasing the
brake.
(Test to be performed with no load on the hoist)
Remove and cap or plug the brake release line from fitting in
the hoist brake release port.
With hydraulic power unit running, move directional control
valve handle slowly to the full open, lowering position.
Increase the engine speed, if necessary, to bring system
pressure up to the relief valve setting. The hoist drum should
remain stationary.
If the hoist drum rotates, the hoist should be disassembled
and the brake components should be examined for wear. In
addition, the brake springs should be measured for the
correct free length in those hoist using helical compression
springs.
Replace any parts showing excessive wear and any spring
whose length is shorter than the minimum shown in the
applicable hoist Service Manual.
Reassemble the brake and hoist and repeat the above steps.
When testing is complete, reattach the brake release line to
the brake release port.
Motor, Motor Control Valve, and Brake
Description
Each hoist has a hydraulic motor, a motor control valve, a
brake cylinder, and a brake clutch which controls motion of
the hoist’s drum. These parts mount on or in the gearbox.
The hydraulic motor connects to the hoist’s brake, which in
turn connects to the gear train of the hoist. The entire hoist
assembly must be removed from the crane to service the
brake cylinder and clutch.
Removal
1.
Power-wash the hoist on the motor side to wash away
potential contaminants from the drive components of the
hoist.
2.
Drain the oil from the hoist gearbox. Once oil is drained,
reinstall the plug or hose at bottom of sight glass.
3.
Tag and disconnect the hydraulic lines from the motor
and the motor control valve. Cap or plug all lines and
openings.
4.
Remove the bolts and washers to free the motor and
motor control valve from the brake cylinder and brake
clutch, which are in the motor control valve gearbox.
Remove the motor and motor control valve as a unit.
Discard the O-ring.
5.
Cover the motor opening in the brake cylinder to protect
drive components inside the hoist drum. As needed,
secure the brake clutch from inside the brake cylinder.
Installation
1.
Uncover the motor opening in the gearbox. Verify these
parts are clean.
2.
Install a replacement O-ring on the motor’s pilot after
lubricating it with gear oil or petroleum jelly.
3.
Engage the motor shaft to the input shaft of the gearbox.
Secure the motor and brake valve to the gearbox with
bolts and washers. Torque bolts to 40 Nm (29.5 lb-ft).
4.
Connect the hydraulic lines to the motor and brake valve
as tagged during removal.
5.
Fill the gearbox with oil. Refer to the hoist filling
procedures on page
Hoist Rotation and Minimum Wrap Indicator System
Description
The main and auxiliary hoists are each equipped with an
encoder (Figure 4-3) and (Figure 4-4) that is part of the hoist
rotation and minimum wrap indicator systems. The encoder
is mounted to the end of each hoist and senses the rotation
of the drum.
Hoist Rotation Indicator
The hoist rotation indicator system provides the operator
with a touch indication of the hoist drum rotation so he or she
knows if and at what speed the hoist drum is rotating. The
system also displays symbols on the rated capacity limiter
(RCL) display and crane control system (CCS) display
indicating which hoist is operating and in what direction it is
rotating (hoist up or hoist down).
The hoist rotation indicator system uses a solenoid to
provide a physical indication to the operator of hoist
operation. Actuation of the indicator is controlled by the CAN
bus modules from input supplied by the hoist drum encoder.
The pulsing solenoid is located in the main and auxiliary
hoist joystick handles and provides feedback proportional to
the hoist line speed by pulsing
the back of the hoist
joystick
. The solenoid will cease operation at high line
speeds to prevent damage to the solenoid.
Minimum Wrap Indicator
The minimum wrap indicator system uses the main and
auxiliary hoist encoders to indicate when there are a
minimum number of wraps of cable remaining on the
respective hoist. When a minimum number of wraps of cable
are reached on the main or auxiliary hoist, the crane control
Fo
r
Reference
Only