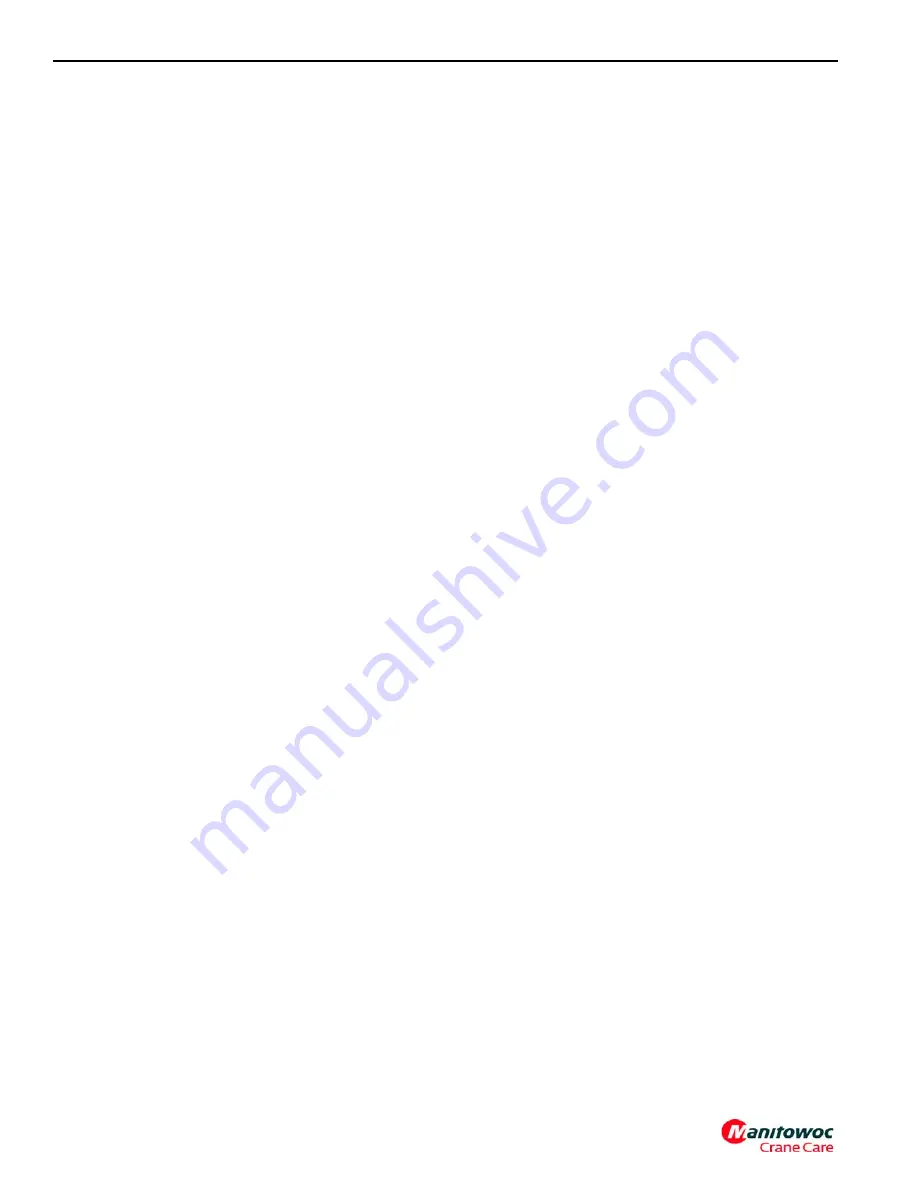
8-32
Published 01-14-2021 Control # 707-01
CARRIER
TMS9000-2 SERVICE MANUAL
1.
Every 900 hours, or 40,000 km (25,000 mi) check for
moisture in the air system by opening the reservoir’s
drain cock or automatic drain valve.
2.
Replacement of the desiccant cartridge may be
necessary if moisture is present; however, the following
conditions can also cause water accumulation and
should be considered before changing the desiccant.
a.
An outside air source has been used to charge the
system that has not been passed through a drying
bed.
b.
Excessively high air demands, which is not normal,
that do not allow the compressor to unload in a
normal fashion. Check for air system leakage.
c.
In areas where the temperature varies 15° C (30° F)
or more daily, small amounts o f wat er can
accumulate in the air system due to condensation.
This is normal and should not be considered as an
indication that the dryer is not performing properly.
3.
Location of the air dryer is too close — less than 1.8 m
(6 ft) — to the air compressor.
4.
Check the electrical connections and mounting bolts for
tightness.
5.
With the ignition switch ON, unplug the electrical
connector at the air dryer and check for power. If there is
no power, check for tripped circuit breaker and broken
wires.
6.
Every 10,800 hrs, 500,000 km (300,000 mi), or
36 months rebuild the air dryer and replace the
desiccant cartridge.
7.
Check the heater and thermostat as follows:
a.
Turn off the engine and let the air dryer end cover
cool to below 4° C (40° F).
b.
Check the resistance across the pins in the female
connector on the bottom of the air dryer. The
resistance should be 6.0 to 9.0 ohms for a 24 volt
system.
c.
Warm the end cover to over 32° C (90° F) and check
the resistance again. The resistance should exceed
1000 ohms.
d.
If the resistance is outside the specified limits,
replace the purge valve housing assembly which
includes the thermostat and heater.
Leak Tests
1.
Test the outlet port check valve in the dryer by observing
the pressure after the governor cuts out. A rapid loss in
pressure indicates a possible failed check valve in the
outlet port.
2.
Test the purge valve by applying a soap solution to the
exhaust. Observe for bubbles during the loading cycle.
3.
Test the safety valve by pulling the stem while the
compressor is loading. Air must exhaust while the stem
is held and stop when the stem is released.
4.
Test all lines and fittings leading to and from the air dryer
with a soap solution for leaking.
Reservoirs
Removal
1.
Chock the wheels and completely depressurize both
systems.
2.
Disconnect and tag all air lines connected to the
reservoir.
3.
Remove the capscrews, washers and nuts and remove
the reservoir from the clamping brackets. If a new
reservoir is to be installed, remove the fittings from the
old reservoir.
Maintenance
Maintenance of the reservoir is limited to inspecting the
mounting hardware. It is not recommended that tanks be
repaired. Damaged tanks need to be replaced.
Cleaning
If the inside of the reservoir has become excessively coated
with sludge that cannot be drained off, remove the reservoir
and clean with solvent, steam, or water. Aerate the reservoir
before reinstalling.
Installation
1.
Install the reservoirs to the brackets and secure with the
nuts, washers and capscrews. Refer to
2.
Connect all air lines to the reservoir.
Low Pressure Indicator Switches
Maintenance is limited to leakage and pressure checks.
Replace faulty switches.
Operating and Leakage Checks
1.
Shut down the engine and slowly reduce the pressure.
2.
The switch should activate at about 520 kPa (75 psi).
The air gauges and indicators in the cab can be used to
test the switch.
3.
With system pressurized, coat the switch with a soap
solution and observe for bubbles. No leaking is
permitted.
Fo
r
Reference
Only