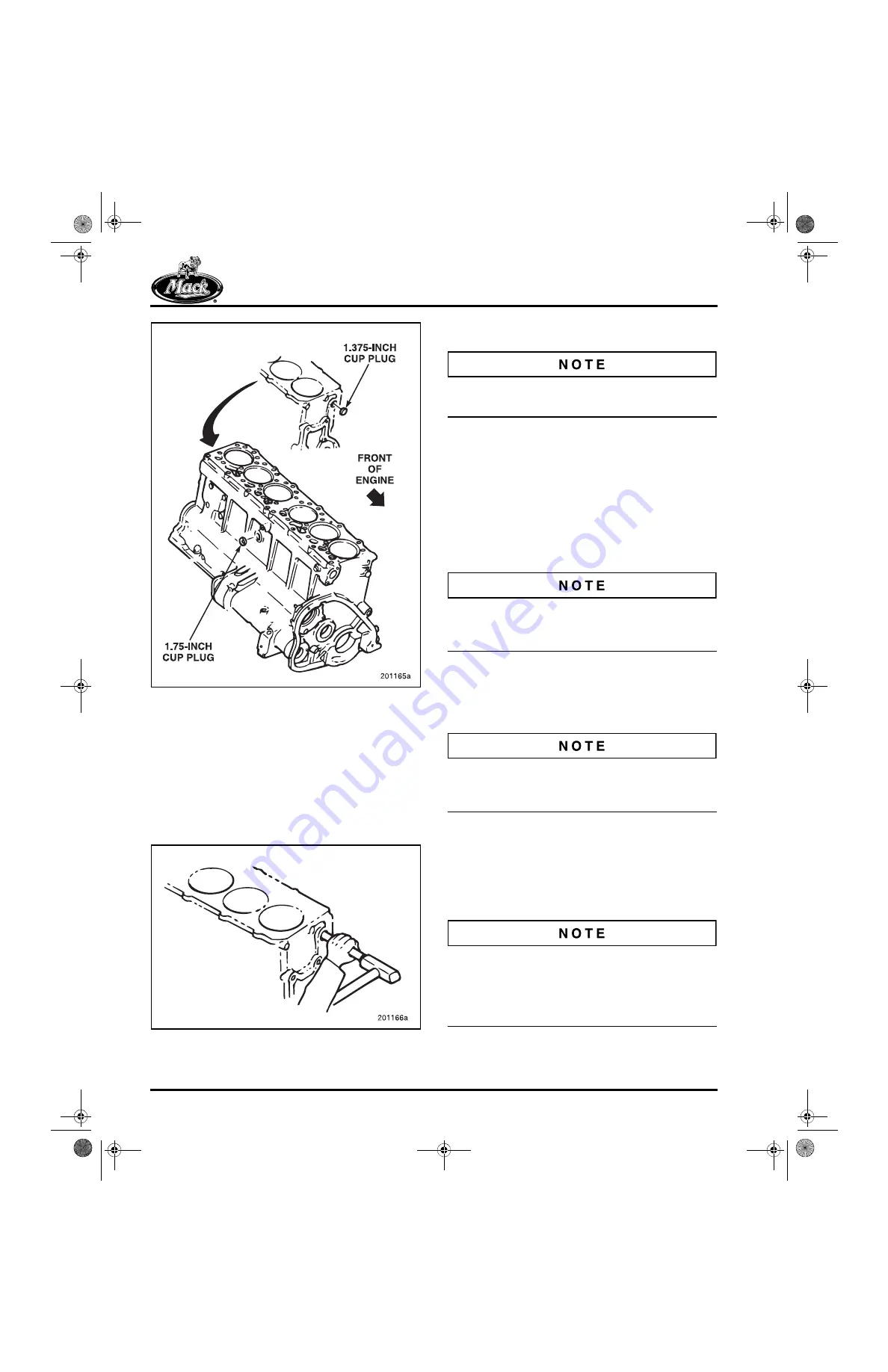
Page 6-4
200 ENGINE ASSEMBLY
Figure 6-2 — Cylinder Block Cup Plugs
INSTALLATION
1. After cleaning the plug hole, apply a thin
coat of Loctite
®
277 to both the surface of
the hole and the outer edge of the plug.
2. Using a proper driver, align the plug in the
hole and drive it inward until the outer lip of
the plug is flush with the cylinder block.
Refer to Figure 6-3.
Figure 6-3 — Cylinder Block Cup Plug Installation
Pipe Plug Replacement
Any rust around a pipe plug is an indication of a
leak and the plug should be replaced.
REMOVAL
1. Using an appropriate wrench, remove the
plug.
2. Clean the threads in the block by running a
tap into the hole, just far enough to remove
any rust on the threads without expanding
the diameter of the hole. Use compressed
air to remove any chips from the block.
It is best to replace a leaking pipe plug. However,
if reusing the same plug, clean thoroughly, paying
special attention to the threads.
3. Using a wire wheel, clean the threads of the
plug. Visually check the thread surfaces for
burrs or damage. Then clean and check the
remaining surfaces.
New plugs already have a sealer applied to the
threads. Applying a Teflon sealer to the threads
will not adversely affect the precoating.
INSTALLATION
Apply appropriate Teflon thread sealant to the
threads and install the plug. Torque to
specification. Refer to Torque Chart in the
SPECIFICATIONS section of this manual.
When checking or assembling engine
components, refer to the Fits and Limits Chart
and Torque Chart in the SPECIFICATIONS
section of this manual for specified dimensions
and torque settings.
5-101.bk Page 4 Friday, March 17, 2006 11:05 AM
Summary of Contents for E7
Page 1: ...E7 ENGINE OVERHAUL AUGUST 1997 ENGINE 5 101...
Page 2: ...Page 0 front fr5 Page 0 Friday March 17 2006 11 04 AM...
Page 5: ...E7ENGINE OVERHAUL MARCH 2006 2 5M REP AUGUST 1997 10M MACK TRUCKS INC 1997 ENGINE 5 101...
Page 13: ...ABOUT THIS MANUAL Page ix ABOUT THIS MANUAL front fr5 Page ix Friday March 17 2006 11 04 AM...
Page 15: ...TABLE OF CONTENTS Page xi TABLE OF CONTENTS front fr5 Page xi Friday March 17 2006 11 04 AM...
Page 24: ...Page xx NOTES front fr5 Page xx Friday March 17 2006 11 04 AM...
Page 31: ...200 SPECIFICATIONS Page 2 1 SPECIFICATIONS 5 101 bk Page 1 Friday March 17 2006 11 05 AM...
Page 55: ...200 ENGINE REMOVAL Page 3 1 ENGINE REMOVAL 5 101 bk Page 1 Friday March 17 2006 11 05 AM...
Page 58: ...Page 3 4 NOTES 5 101 bk Page 4 Friday March 17 2006 11 05 AM...
Page 90: ...Page 4 32 NOTES 5 101 bk Page 32 Friday March 17 2006 11 05 AM...
Page 91: ...200 BENCH PROCEDURES Page 5 1 BENCH PROCEDURES 5 101 bk Page 1 Friday March 17 2006 11 05 AM...
Page 158: ...Page 5 68 NOTES 5 101 bk Page 68 Friday March 17 2006 11 05 AM...
Page 159: ...200 ENGINE ASSEMBLY Page 6 1 ENGINE ASSEMBLY 5 101 bk Page 1 Friday March 17 2006 11 05 AM...
Page 240: ...Page 6 82 NOTES 5 101 bk Page 82 Friday March 17 2006 11 05 AM...
Page 272: ...Page 8 10 NOTES 5 101 bk Page 10 Friday March 17 2006 11 05 AM...
Page 273: ...200 TROUBLESHOOTING Page 9 1 TROUBLESHOOTING 5 101 bk Page 1 Friday March 17 2006 11 05 AM...
Page 292: ...Page 9 20 NOTES 5 101 bk Page 20 Friday March 17 2006 11 05 AM...
Page 293: ...200 APPENDIX Page 10 1 APPENDIX 5 101 bk Page 1 Friday March 17 2006 11 05 AM...
Page 295: ...200 APPENDIX Page 10 3 E7 LUBRICATION SYSTEM 5 101 bk Page 3 Friday March 17 2006 11 05 AM...
Page 296: ...Page 10 4 200 APPENDIX E7 COOLING SYSTEM 5 101 bk Page 4 Friday March 17 2006 11 05 AM...
Page 297: ...INDEX Page 11 1 INDEX INDEX FR5 Page 1 Friday March 17 2006 11 04 AM...
Page 302: ...Page 11 6 NOTES INDEX FR5 Page 6 Friday March 17 2006 11 04 AM...
Page 303: ...E7 ENGINE OVERHAUL PRINTED IN U S A ENGINE 5 101 MACK TRUCKS INC 1997...