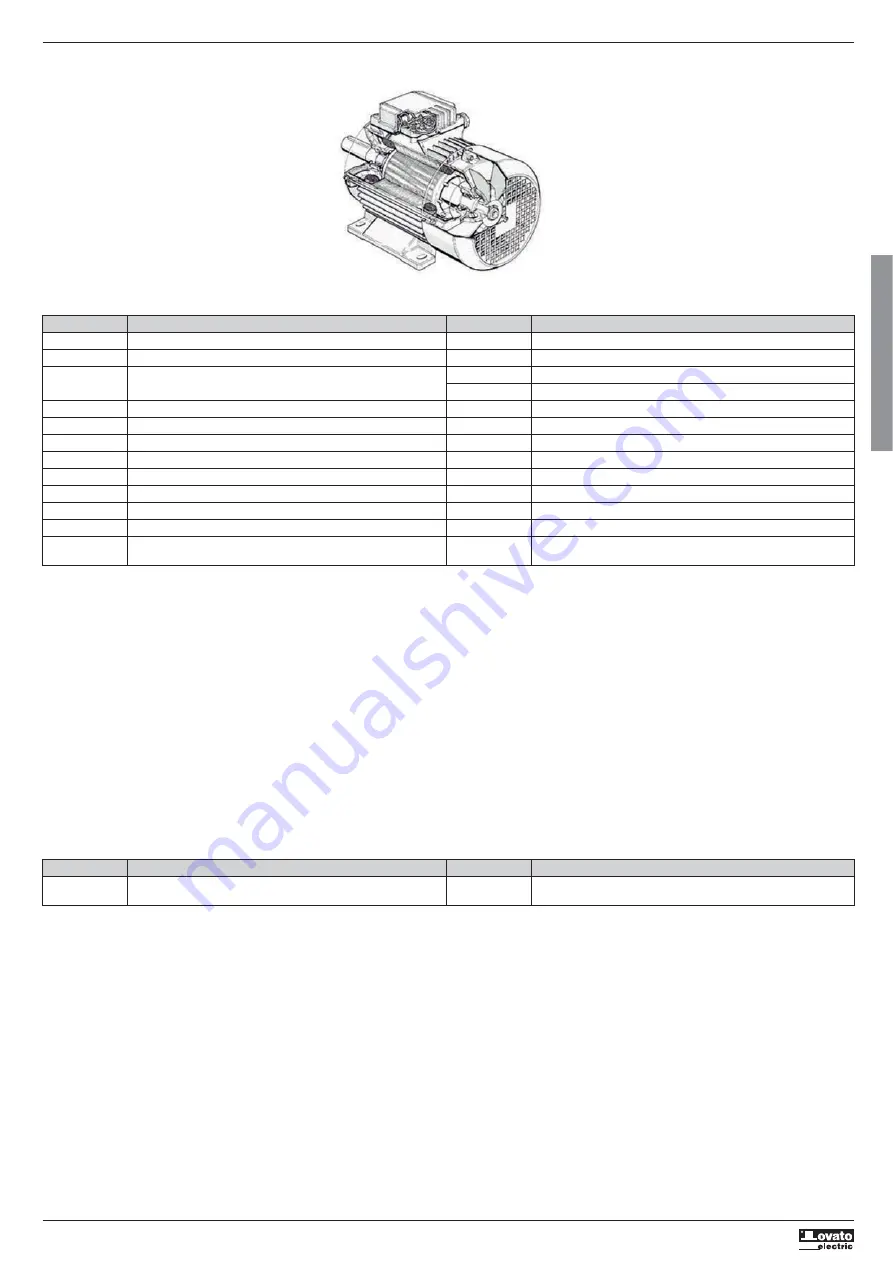
I472 GB I 01 19
31100284
24
G
B
5.5 MOTOR PARAMETERS
Parameter Function Setting Description
P208.01 AC input voltage 400V Insert the value of the supply voltage
P300.00 Motor control mode 6 V/f characteristic control, open loop
P302.00 V/f shape 0 Linear V/f (Applications: conveyor belts, …)
1 Quadratic V/f (Applications: pumps, fans, …)
P303.01 V/f Base voltage 400V Set the same value of the rated voltage of the motor (P320.07)
P303.02 V/f Base frequency 50Hz Set the same value of the rated frequency of the motor (P320.05)
P315.01 Slip compensation 5% Set the suggested value
P320.04 Rated speed of the motor _rpm Insert the rated speed of the motor
P320.05 Rated frequency of the motor __Hz Set the rated frequency of the motor
P320.06 Rated power of the motor __KW Set the rated power of the motor
P320.07 Rated voltage of the motor __V Set the rated voltage of the motor
P320.08 Rated cosphi of the motor __ Set the rated cosphi of the motor
P323.00 Rated current of the motor _A Insert the rated current of the motor.
Setting this parameter, the motor thermic protection will be enabled.
NOTE. If you need to enable the sensorless vector control set P300.00=4.
All the other parameters must be left to default settings
Automatic motor data identification
Following the settings of the rated motor parameters, the automatic identification of the motor data can be performed, which results in the best possible parameter settings.
Preconditions
– The motor must be cold.
– All rated motor data are known and set in the VLB3 (see above table).
– The VLB3 is supplied (DC-bus voltage is available).
– The VLB3 is enabled, error-free and in the "Ready to switch on" or "Switched on" device state.
– The motor is stopped (no start enable).
– No quick stop is active.
Procedure
– Enable the automatic motor data identification: Set P327.04 = 1.
– Issue the start command to start the procedure.
Parameter Function Setting Description
P327.04 Automatic motor data identification 1 1= Start automatic identification of the motor data.
Note. During the procedure, the motor is energized!
As soon as the process has been started, the VLB3 characteristic and the motor equivalent circuit diagram data are automatically identified.
The procedure can take from some seconds to minutes. During and after the procedure, the LED "RDY" (blue) is permanently on. After completing, a renewed start command is required to start the motor.