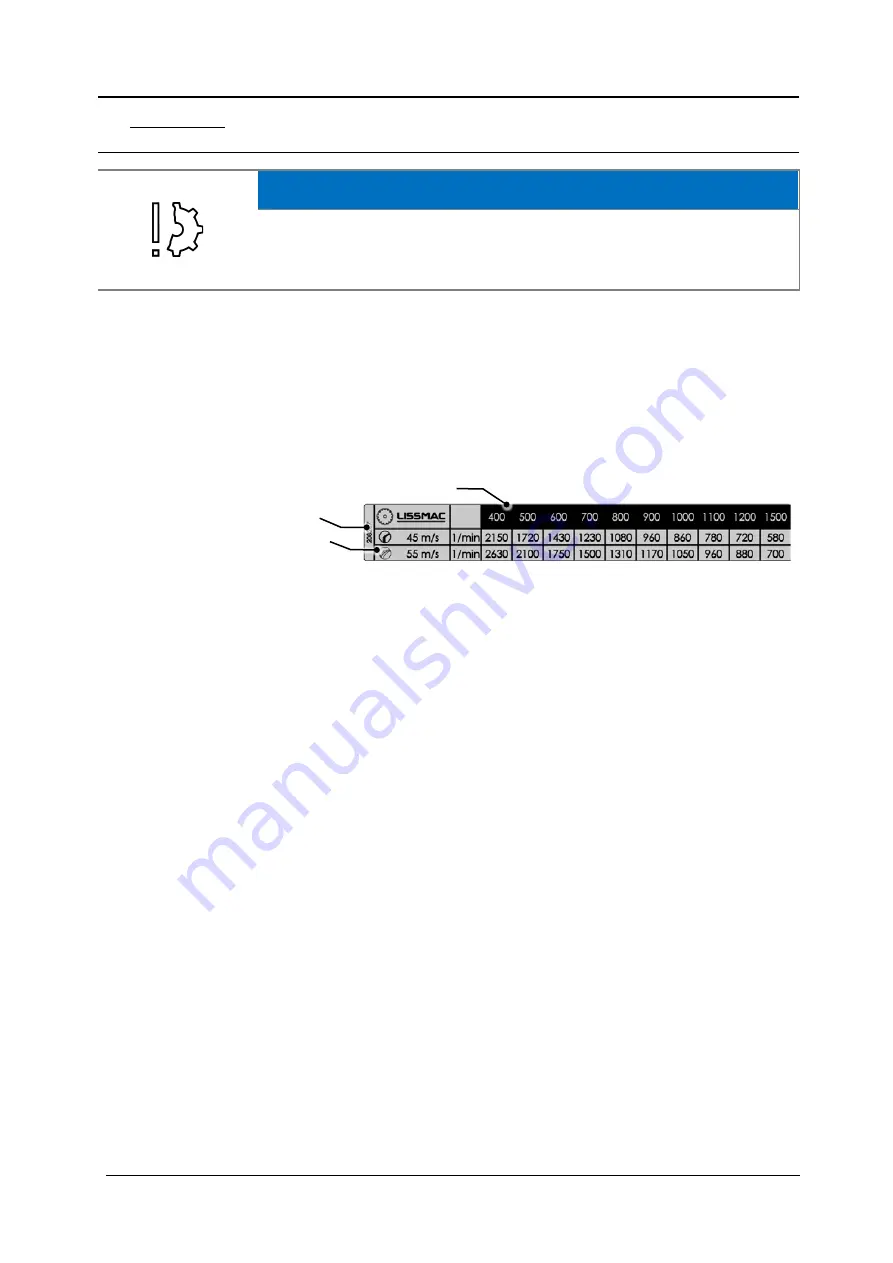
24/92
4.2.
Tools (saw blade)
NOTICE
Tool selection
Never use a rotating tool, with a maximum speed rating lower than the rated speed of the machine.
Defective or broken tools must be replaced immediately.
Selecting a saw blade
See section 9 Tools
Storing tools
The tools used must be protected from moisture. The diamond segments must be protected from damage.
Blade speeds
For best cutting results, the saw blade speed must be adjusted to the aggregate to be cut.
Saw blade speed is governed by the Engine RPM and can be monitored on the multi-function display.
Blade RPM
Concrete
Asphalt
Blade diameter
Summary of Contents for MULTICUT 550 GH
Page 2: ...2 92...
Page 8: ...8 92 Notes...
Page 10: ...10 92 9 Tools 69 10 Warranty 70 11 Circuit diagram 72 12 APPENDIX A ERROR CODE LIST HATZ 76...
Page 32: ...32 92 Speed conversion option Approved belts XPA 1060 1000 1120 antistatic Setup G...
Page 72: ...72 92 11 CIRCUIT DIAGRAM...
Page 73: ...73 92...
Page 74: ...74 92...
Page 75: ...75 92...
Page 76: ...76 92 12 APPENDIX A ERROR CODE LIST HATZ...
Page 77: ...77 92...
Page 78: ...78 92...
Page 79: ...79 92...
Page 80: ...80 92...
Page 81: ...81 92...
Page 82: ...82 92...
Page 83: ...83 92...
Page 84: ...84 92...
Page 85: ...85 92...
Page 86: ...86 92...
Page 87: ...87 92...
Page 88: ...88 92...
Page 89: ...89 92...
Page 90: ...90 92...
Page 91: ...91 92...
Page 92: ...92 92...