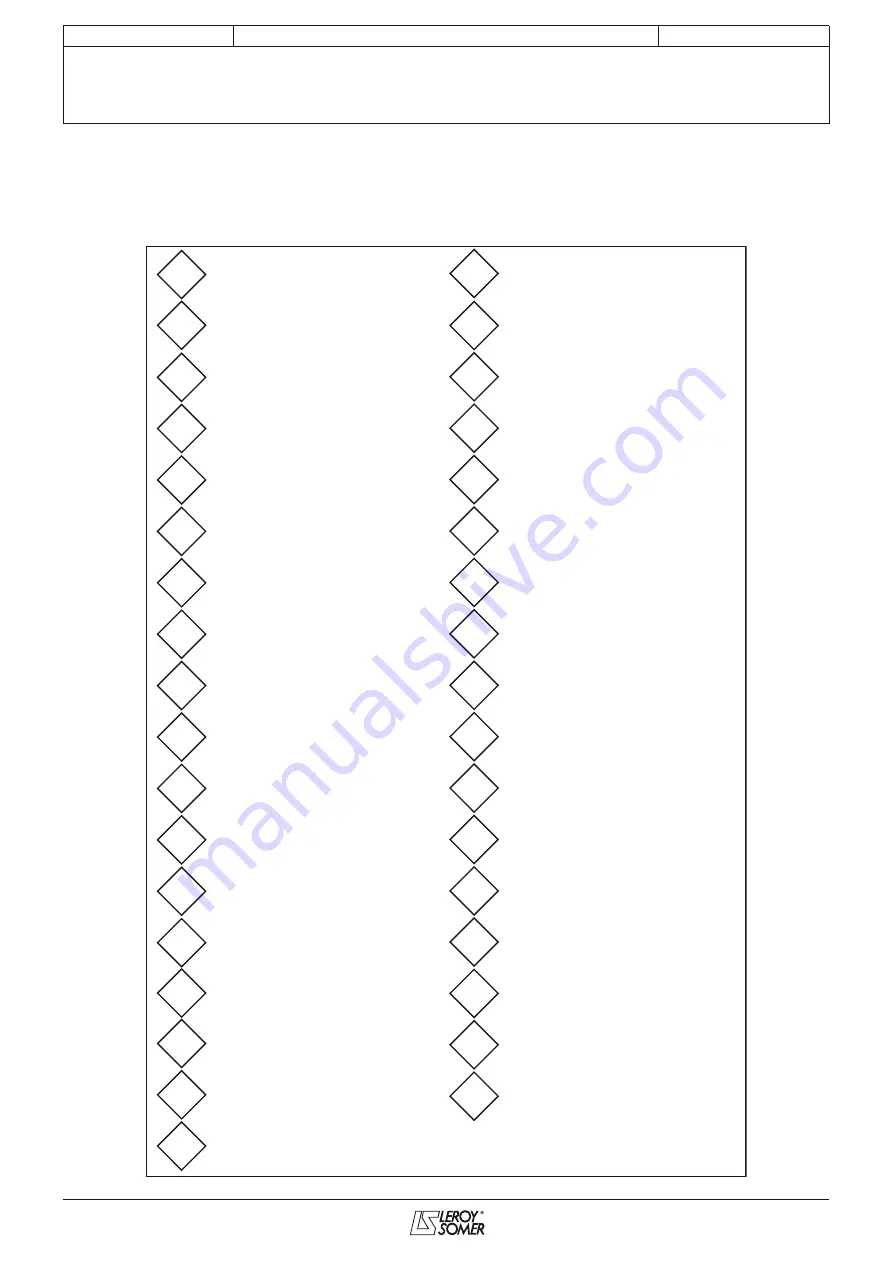
94
COMMISSIONING MANUAL
POWERDRIVE MD
Variable speed drive
MENUS AND DIAGRAMS IN ADVANCED SET UP MODE
LEROY-SOMER
3871 en - 2011.05 / h
5.11 - Menu 10: Status and trips
5.11.1 - Menu 10 dia
g
rams
Drive healthy
Drive active
Zero speed
Running at minimum speed
Below set speed
At speed
Above set speed
Nominal load reached
Drive output at current limit
Drive regenerating
Braking IGBT active
Direction commanded
Direction running
Mains loss
DC bus undervoltage
Motor overload alarm
Drive overtemperature alarm
Drive general warning
Last trip
(most recent trip)
Trip - 2
Trip - 3
Trip - 4
Trip - 5
Trip - 6
Trip - 7
Trip - 8
Trip - 9
Trip - 10
(oldest trip)
Status word
10.01
to
10.15
Vmin alarm
Vmax alarm
Maximum speed
DC bus preload contactor closed
Drive status
Current trip
• Operating states
10.01
10.02
10.20
10.03
10.21
10.04
10.22
10.05
10.23
10.06
10.24
10.07
10.25
10.08
10.26
10.09
10.27
10.10
10.28
10.11
10.29
10.13
10.40
10.14
10.51
10.15
10.16
10.17
10.18
10.19
10.52
10.53
10.76
10.98
10.99