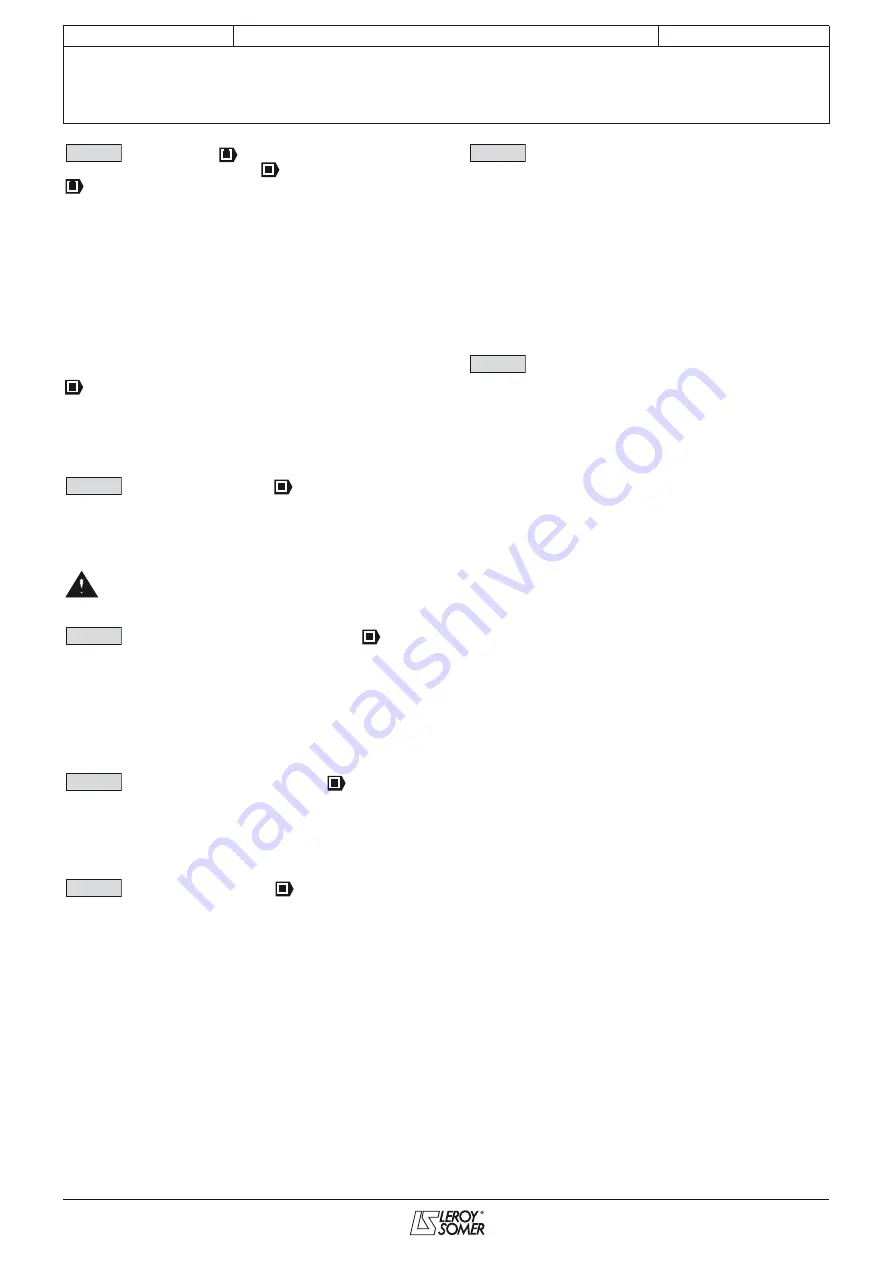
27
COMMISSIONING MANUAL
POWERDRIVE MD
Variable speed drive
PARAMETER SETTING INTERFACE
LEROY-SOMER
3871 en - 2011.05 / h
: V to F select (
)
Drive encoder filter (
)
:
Adjustment range : Linear (0) or Dynamic (1)
Factory setting
: Linear (0)
Linear (0): The V/F ratio is fixed and set by the base
fre
q
uency (
00.10
).
Dynamic (1):
Dynamic V/F ratio.
Generates a voltage/frequency characteristic which varies with
theload. It is for use in quadratic torque applications
(pumps/fans/compressors). It can be used in constant torque
applications with low dynamics to reduce motor noise.
CAUTION:
00.16
is only active if
00.14
= LINEAR V/F (2).
:
Adjustment range : 0 to 10
Factory setting
: 3
This parameter is used to filter the noise on the speed
feedback.
The filter is inactive if
00.16
= 0.
: Encoder phase an
g
le (
)
Adjustment range : 0 to 359.9°
Factory setting
: 0.0°
Indicates the result of the phasing test (see
00.42
). It is stored
when the drive is powered down and will be modified
automatically only after a new phasing test.
• The phase an
g
le, where it is known, can be entered
manually. Any incorrect value can cause the motor
to rotate in the wron
g
direction or trip the drive.
: Speed loop proportional
g
ain (Kp1) (
)
Adjustment range : 0 to 32000
Factory setting
: 200
Sets the stability of the motor speed in the event of sudden
variations in the reference.
Increase the proportional gain until vibration occurs in the
motor, then reduce the value by 20 to 30%, checking that the
stability of the motor is acceptable in the event of sudden
variations in speed, both at no load and on load.
: Speed loop inte
g
ral
g
ain (Ki1) (
)
Adjustment range : 0 to 32000
Factory setting
: 100
Sets the stability of the motor speed on load impact.
Increase the integral gain so that the same speed is obtained
on load and at no load in the event of load impact.
: Current demand filter (
)
Adjustment range : 0 to 10
Factory setting
: 2
This filter is used to introduce a time constant aimed at
reducing any noise generated by the speed loop, such that:
time constant = 2
00.20
ms.
: Current loop proportional
g
ain
Adjustment range : 0 to 250
Factory setting
: 40
Due to a number of factors internal to the drive, oscillations
may occur in the following cases:
- Frequency control with current limiting around the rated
frequency and on load impacts.
- Torque control on machines with a low load and around the
rated speed.
- On a mains supply break or on a controlled deceleration ramp
when control via the DC bus is requested.
To reduce these oscillations, increasing the proportional gain
00.21
is recommended.
: Start stop lo
g
ic select
Adjustment range : Latched Run/Stop (0), Pulsed Run/Stop (1),
Run-Fwd/Rev (2),
Controlled Run/Stop (3)
Factory setting
: Controlled run/stop (3)
Used to choose one of 4 Run/Stop command and Direction of
rotation management modes.
Run no latch (0):
Command for FWD/Stop and REV/Stop via
stay-put contacts.
Terminal DI4 preset to FWD/Stop.
Terminal DI5 preset to REV/Stop.
On power-up or after a trip reset, if a run command is already
selected, the motor starts as soon as the reference appears.
Pulsed Run/Stop (1):
Command for Run and Stop via jog
contacts.
In this mode, use DIO3 to give the Stop command.
To do this, configure:
-
00.34
=
06.39
(DIO3 assigned as Stop input).
Terminal DI4 preset as Run FWD.
Terminal DI5 preset as Run REV.
If the user wishes to assign DIO1 and DIO2 to other functions,
provide stay-put contacts on these inputs.
To change from FWD to REV or vice versa, go via a stop
command.
Run-Fwd/Rev (2):
Command for Run/Stop via stay-put
contact.
In this mode, use DI4 as Run/Stop, and DI5 to give the direction
of rotation. To do this, configure:
-
00.35
=
06.34
and
00.36
=
06.33
.
CONTROLLED RUN/STOP (3): Operation is identical to the
Latched Run/Stop (0) mode if
00.24
= SECUR. DISAB. (1)
(factory settin
g
). To use the specific features of this mode,
00.24
must be set to DRIVE ENABLE (0). In this case, if
the drive is powered up with the run command present,
the motor does not start. The run command must be
cycled for it to have effect. Similarly, upon clearin
g
of a
trip, if the run command is present, it is not taken into
account. It must be cycled to have effect.
If, in one of these configurations, an input is not used by the
application (no Reverse operation for example), the
corresponding input can be reassigned using menu 8
(see section 5.9).
Note:
Modifications to
00.22
must be made with the drive
disabled.
00.16
00.17
00.18
00.19
00.20
00.21
00.22