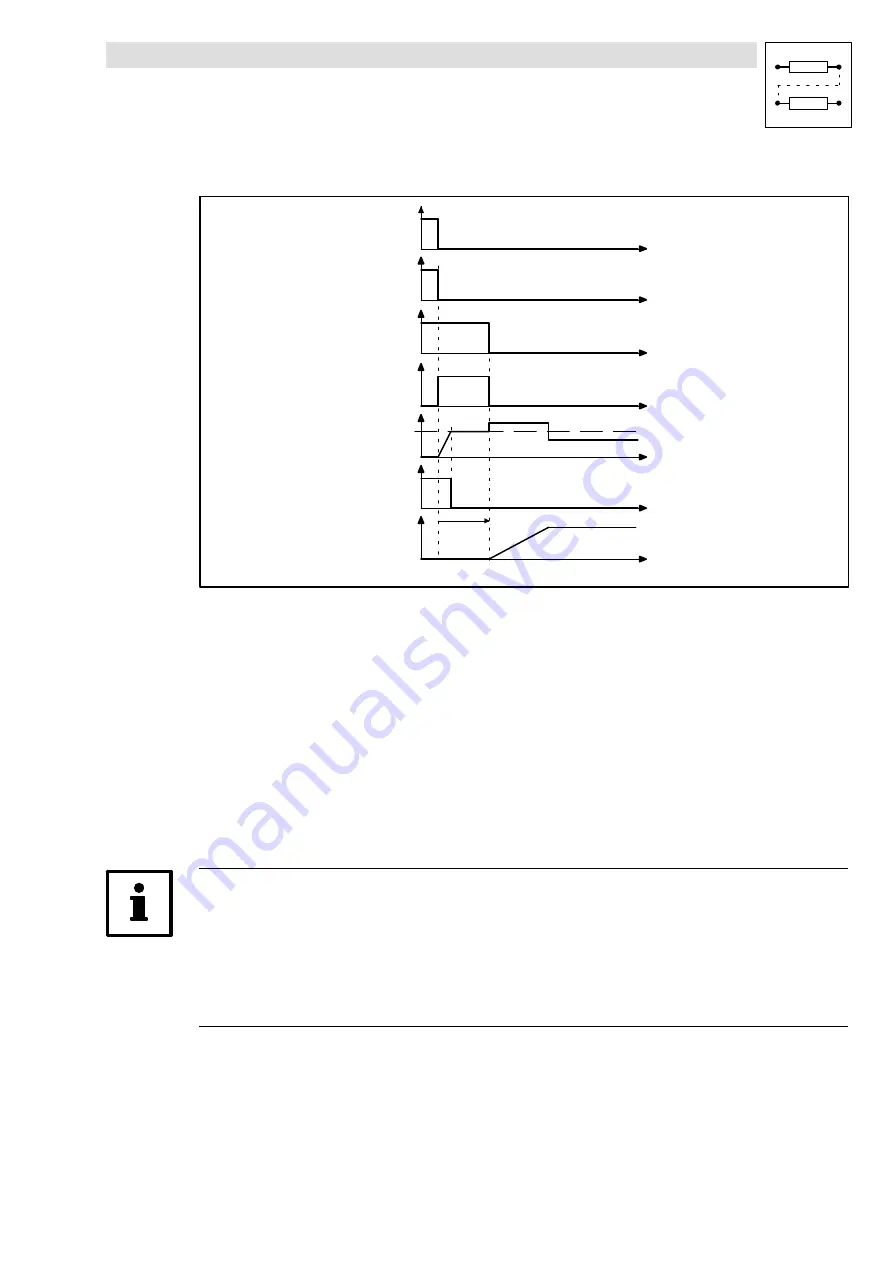
Configuration
2−65
l
EDSVF9383V−EXT EN 2.0
2.4.13.2
Open the brake
t
t
BRK1
−
SET
MCTRL
−
NSET2
BRK1
−
OUT
BRK1
−
CINH
MCTRL
−
MACT
MCTRL
−
MACT = C0244
C0196
t
t
BRK1
−
M
−
STORE
t
BRK1
−
QSP
t
t
Fig. 2−47
Signal sequence when the brake is opened (released)
Function procedure
1. With BRK−SET = LOW, BRK−CINH is immediately set LOW. At the same time, BRK−M−STORE
is set HIGH.
– You can use this signal to create a defined torque in the drive, before the brake opens. In
hoists, for instance, a "lowering" during the load transfer is thus avoided. The signal is reset
only after the time set under C0196 has elapsed.
2. Once the torque has reached the value (holding torque) set under C0244, BRK−OUT = LOW.
3. When the input is reset, a time element is triggered. After the time set under C0196 has
elapsed, BRK−QSP = LOW.
– This signal is used e.g. to enable the setpoint integrator after the brake disengaging time has
elapsed.
Tip!
l
When the brake is disengaged before the brake disengaging time (C0196) has elapsed and an
actual speed is detected which is higher than the value at BRK−Nx, BRK−QSP = LOW and
BRK−M−STORE = LOW. The drive can immediately operated speed−controlled.
l
For an optimum starting behaviour, the time under C0196 should not be much longer than the
actual brake disengaging time.