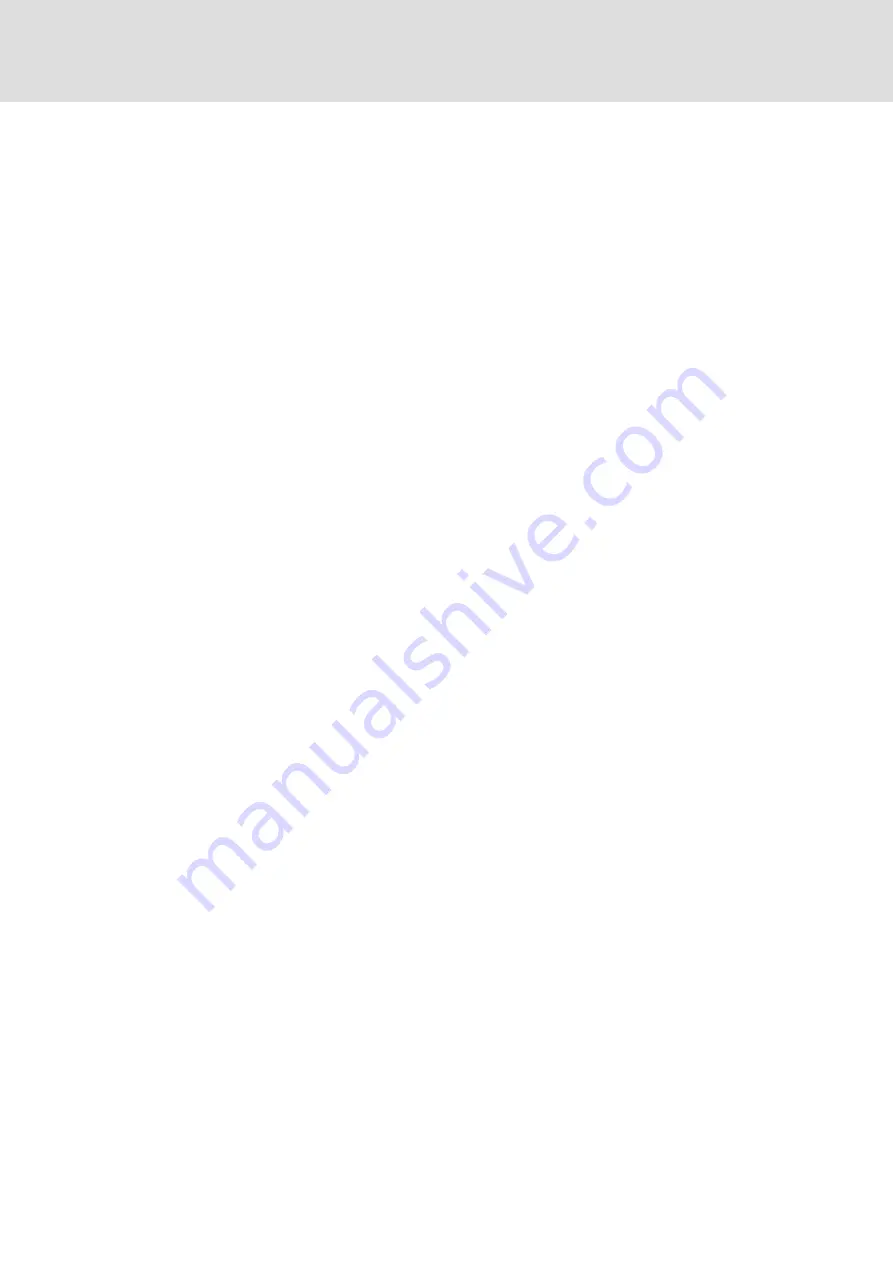
Technical data
Supply concept of control voltage
Internal 24 V supply voltage
61
EDS84DPS424 EN 5.0
4.6
Supply concept of control voltage
8400 protec controllers generate the 24 V supply voltage of the control electronics from
the mains voltage by means of an integrated power supply unit (mains−operated supply).
An external 24 V buffer voltage from a safely separated power supply unit (SELV/PELV)
must be connected in order to implement a self−contained supply of the control
electronics.
The 24 V supply voltage is required for the control electronics and other components such
as fieldbus communication and/or drive−based safety.
In addition, the supply voltage is available at the terminals, irrespective of the fact whether
it is fed internally or externally. Information on the supply voltage at the digital and analog
terminals is provided under:
ƒ
Digital inputs(
ƒ
Digital outputs(
ƒ
Analog inputs(
ƒ
Synchronous serial interface (SSI) (
The supply voltage is preferentially used for:
ƒ
Connecting potential−free contacts to digital inputs
ƒ
Supplying external sensors
At an external 24 V supply voltage, the rated values may deviate according to the voltage
source.
4.6.1
Internal 24 V supply voltage
At an internal 24 V supply voltage, the maximally permissible total current of terminals
X4x, X50/X8x is 1 A.
Summary of Contents for 8400 protec
Page 2: ...0Fig 0Tab 0...
Page 190: ...Appendix Declarations and certificates 13 190 EDS84DPS424 EN 5 0...
Page 191: ...Appendix Declarations and certificates 13 191 EDS84DPS424 EN 5 0...
Page 192: ...Appendix Declarations and certificates 13 192 EDS84DPS424 EN 5 0...
Page 193: ...Appendix Declarations and certificates 13 193 EDS84DPS424 EN 5 0...
Page 194: ...Appendix Declarations and certificates 13 194 EDS84DPS424 EN 5 0...