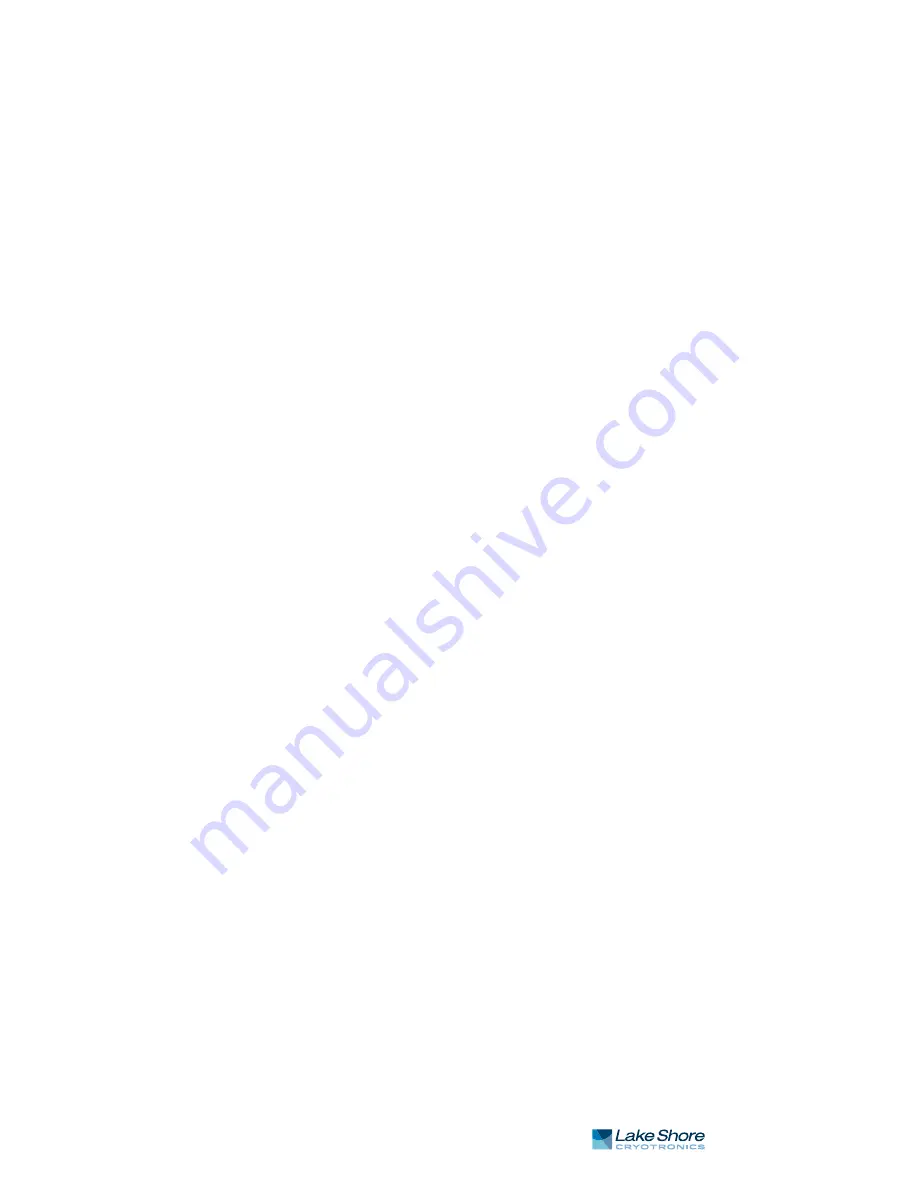
2.7.3 Considerations When Measuring Ultra-Low Temperatures Below 300 mK
25
|
www.lakeshore.com
2.7.3 Considerations
When Measuring Ultra-
Low Temperatures
Below 300 mK
Temperature measurement becomes more difficult as temperatures approach the
bottom of the Model 350’s measurement range. When measuring temperatures
down to about 300 mK, the 1 mV autorange setting usually results in excellent per-
formance. At even lower temperatures you may have to manually select a current
range to minimize measurement errors. Measurement errors come from self-heating,
instrument resolution (noise), instrument uncertainty, and sensor calibration
uncertainty.
When measuring a sensor, a user should choose the highest excitation current possi-
ble without causing significant self-heating in the sensor. Higher current results in
the largest signal which creates the best signal to noise ratio and gives the highest
instrument accuracy. As the temperature approaches 100 mK, self-heating, via I
2
*R
Joule heating, begins to dominate overall measurement uncertainty.
There are several ways to decrease self-heating such as increasing the sensor's ther-
mal transfer, selecting a sensor with lower resistance (lower power dissipation), and
reducing the excitation current (by changing the instrument range). Many times, the
sensor thermal characteristics are defined by the type of sensor selected and cannot
be changed. Magnetic fields, sensitivity requirements, noise performance, mounting
considerations, cost, and availability may drive a sensor selection. Once a sensor is
selected, the excitation current should be chosen to balance errors from self-heating
and other sources of resolution, and uncertainty.
Self-heating calculations are explained in section 2.x.x. For a typical CX-1010 at
100 mK with electronic resistance (R
e
) equal to 21,389
)
, the thermal resistance (R
t
)
is 2E+9
)
(see Appendix E: Temperature Measurement System in the Temperature
Control Catolog). At 10 nA excitation current, the typical self-heating error would be
,
T
SH
= I
2
R
e
R
t
= 10 nA
2
* 21,389 * 2E+9 = +4.3mK.
Instrument electronic accuracy can be calculated from the specifications listed in
TABLE 1-3. The accuracy depends on the range selected and the sensor reading,
TABLE 1-3 lists this as a reading and range error (such as ±100
)
±0.04% rdg for NTC
RTD 1mV, 0
)
to 100 k
)
input range, 10nA excitation current). The accuracy in ohms
can then be converted to temperature using the sensitivity of the sensor being used.
For instance, if a typical Cernox™ CX-1010 is used at 100 mK and 10 nA drive, the
instrument electronic accuracy would be ±100
)
±0.04% * 21,389
)
or ±108.6
)
.
This can then be converted to temperature by using the typical sensitivity at 100 mK
(-558,110
)
/K), ±108.6
)
÷ -558,110
)
/K = ±0.2 mK.
The sensor calibration uncertainty is usually listed on the sensor’s data sheet. For the
CX-1010 at 100 mK, the uncertainty is ±4 mK. Contact Lake Shore for more informa-
tion concerning the uncertainties surrounding calibration, drift, and other sources of
error that determine the uncertainties associated with the sensor.
The total measurement uncertainty is the sum of the self-heating offset error ±
instrument accuracy ± sensor calibration uncertainty. For a typical CX-1010 sensor
driven with 10 nA current at 100 mK, the total uncertainty is
+4.3 mK ± 0.2 mK ± 4 mK = +4.3 mK ± (0.2 mK + 4 mK).
This total uncertainty can be calculated for other excitation currents and other sen-
sors, which may result in different uncertainties. Note that in this analysis, these
uncertainties are simply added together; another common method of adding uncer-
tainties is to add the sum of squares method. Either method of combining uncertain-
ties will illustrate the errors used to evaluate the various sensors and excitation
currents.
Summary of Contents for 350
Page 4: ...Model 350 Temperature Controller ...
Page 6: ......
Page 14: ...Model 350 Temperature Controller ...
Page 28: ...14 cHAPTER 1 Introduction Model 350 Temperature Controller ...
Page 53: ...Examples of PID control 2 13 4 ManualOutput 39 www lakeshore com FIGURE 2 4 ...
Page 58: ...44 cHAPTER 2 Cooling System Design and Temperature Control Model 350 Temperature Controller ...
Page 118: ...104 cHAPTER 5 Advanced Operation Model 350 Temperature Controller ...
Page 178: ...164 cHAPTER 7 Options and Accessories Model 350 Temperature Controller ...
Page 192: ...178 cHAPTER 8 Service Model 350 Temperature Controller ...