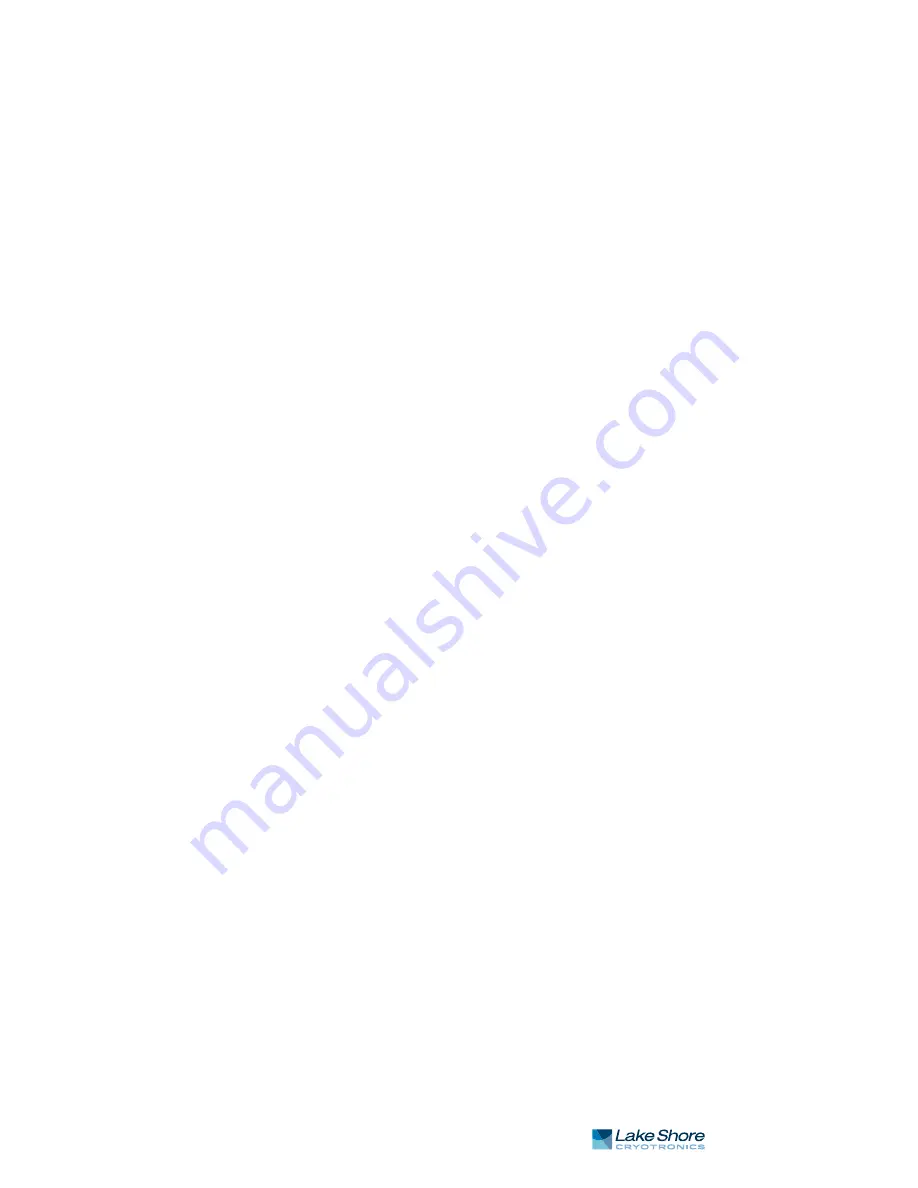
2.4.5 Measurement Speed and Filtering
21
|
www.lakeshore.com
2.4.4.4 Active Common Mode Reduction
It is common for precision measurement equipment to use a differential input as the
first stage of signal conditioning. The differential input offers high impedance on both
input voltage terminals to reduce the effect of common mode voltage (voltage that
acts on both leads at the same time). Common mode voltage can come from many
sources including external noise coupling into the lead wires and the instrument’s
own current source. To reduce the effect of common mode voltage further the
Model 350 includes an active common mode reduction circuit. This circuit dynami-
cally adjusts the operation point of the current source output to minimize the com-
mon mode voltage seen at the measurement input.
2.4.4.5 Matched Impedance Current Source
The two current source output terminals on the Model 350 have the same source
impedance, similar to the voltage input terminals of a differential input that have the
same input impedance. The sensor being measured and all noise sources in the envi-
ronment “see” the same impedance on both current source leads when looking back
into the instrument. Traditional current sources with different impedance on each
lead (one lead grounded) can lessen the common mode rejection of a differential
input especially when measuring sensors with large resistances. The common mode
noise sources have the same effect on both sides of the sensor being measured ensur-
ing that common mode voltages are not turned into normal mode voltages (voltages
are present between measurement leads).
2.4.5 Measurement
Speed and Filtering
The Model 350 has a built in hardware low-pass filter with a -3dB frequency of 16 Hz.
Additional filtering is done in the instrument firmware as a linear average.
The input hardware settles about 100 milliseconds after a temperature (sensor resis-
tance) change if no range change is required. When the firmware filter is turned on,
that filter settling time must be added to the hardware settling time to approximate
overall settling. The firmware filter can be set from 2 point to 64 points. See section
4.4.10 for more details.
Range change requires additional settling because the internal circuits need time to
reestablish their operating point.
The instruments A/D sampling (update) rate is 10 readings per second and all read-
ings are available over the computer interface. This rate allows the A/D to capture any
sensor changes that are able to pass through the input hardware. The temperature
control loop, analog voltage outputs and max/min capture are updated with each A/D
reading.
2.5 Noise Sources
The effect of electrical noise is usually small and can be ignored when making routine
measurements but noise can become important when measuring low temperatures.
The following paragraphs describe the most common noise source encountered with
small signal measurements and some techniques that can help reduce their effect.
More specific installation instructions are given in Chapter 3.
2.5.1 Induced Electrical
Noise
Noise from the environment is typically classified as either electric field (E-field) or
magnetic field (H-field). E-field noise capacitively couples into measurement leads or
the sensor being measured. Voltage is induced on the leads as if the noise source and
lead are two halves of a capacitor. The amount of coupling is related to the voltage
change at the source, the common area between source and receiver (length of lead)
and dielectric0 between them (distance in air). A cable shield is the first line of
defense against E-field noise.
Summary of Contents for 350
Page 4: ...Model 350 Temperature Controller ...
Page 6: ......
Page 14: ...Model 350 Temperature Controller ...
Page 28: ...14 cHAPTER 1 Introduction Model 350 Temperature Controller ...
Page 53: ...Examples of PID control 2 13 4 ManualOutput 39 www lakeshore com FIGURE 2 4 ...
Page 58: ...44 cHAPTER 2 Cooling System Design and Temperature Control Model 350 Temperature Controller ...
Page 118: ...104 cHAPTER 5 Advanced Operation Model 350 Temperature Controller ...
Page 178: ...164 cHAPTER 7 Options and Accessories Model 350 Temperature Controller ...
Page 192: ...178 cHAPTER 8 Service Model 350 Temperature Controller ...