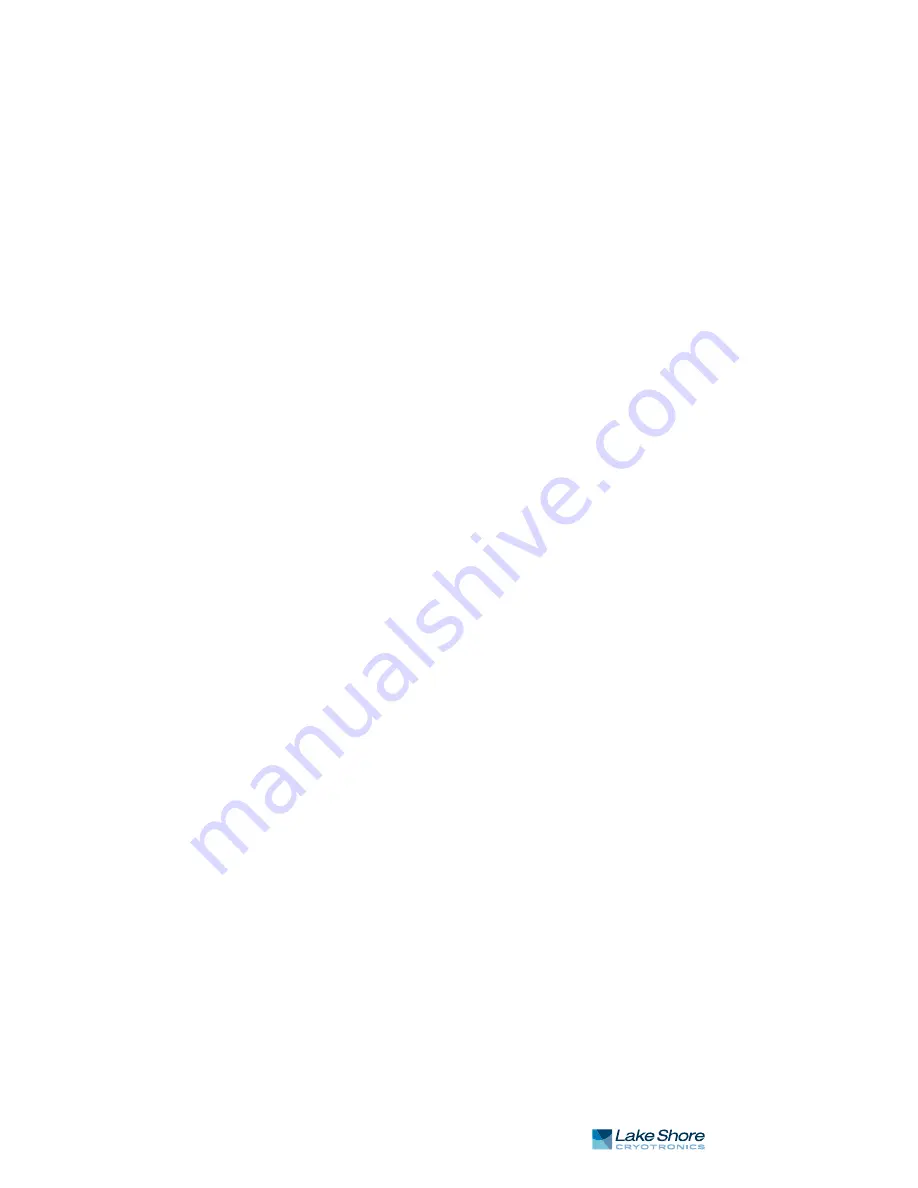
4.5.1 Heater Outputs
79
|
www.lakeshore.com
Menu Navigation:
Output Setup
Q
Output
(1, 2, 3, or 4)
Q
Control Input
Q
(None, Input A, Input B,
Input C, Input D)
Default:
Output 1
Q
Control Input
Q
(Input A)
Output 2
Q
Control Input
Q
(Input B)
Output
(3, 4)
Q
Off
Interface Command:
HTRSET
4.5.1.5.2 Proportional (P)
The proportional parameter (also called gain) is the P part of the PID control equation.
It has a range of 0 to 1000 with a resolution of 0.1. The default value is 50. Enter a
value greater than 0 for P when using closed loop control.
To set P, first configure the front panel display to show the desired control loop infor-
mation, then use the
P
key on the front panel. A quick way to access the setting if the
control loop information is not already being displayed, is to press
A
,
B
,
C
, or
D
on the
front panel to temporarily display the control loop information while the new setting
is entered. Refer to section 4.3 for details on configuring the front panel display.
Menu Navigation:
P
Q
(0 to 9999)
Default: 50
Interface Command:
PID
4.5.1.5.3 Integral (I)
The integral parameter (also called reset) is the I part of the PID control equation. It
has a range of 0 to 1000 with a resolution of 0.1. The default value is 20. Setting I to 0
turns the reset function off. The I setting is related to seconds by:
I
setting
=1000/I
seconds
For example, a reset number setting of 20 corresponds to a time constant of 50 s. A
system will normally take several time constants to settle into the setpoint. The 50 s
time constant, if correct for the system being controlled, would result in a system that
stabilizes at a new setpoint in between 5 min and 10 min.
To set I, first configure the front panel display to show the desired control loop infor-
mation, then use the
I
key on the front panel. A quick way to access the setting if the
control loop information is not already being displayed is to press
A
,
B
,
C
, or
D
on the
front panel to temporarily display the control loop information while the new setting
is entered. Refer to section 4.3 for details on configuring the front panel display.
Menu Navigation:
I
Q
(0 to 1000)
Default: 20
Interface Command:
PID
4.5.1.5.4 Derivative (D)
The derivative parameter (sometimes called rate) is the D part of the PID control
equation. The derivative time constant should normally be somewhere between
p
and
1/i
the integral time in seconds, if used at all. As a convenience to the operator,
the Model 350 derivative time constant is expressed in percent of ¼ the integral
time. The range is between 0% and 200%. Start with settings of 0%, 50%, or 100%,
and determine which setting gives you the type of control you desire. Do not be sur-
prised if the setting you prefer is 0%. Note that by using a percent of integral time,
derivative scales automatically with changes in the integral value and does not have
to be revisited frequently.
Summary of Contents for 350
Page 4: ...Model 350 Temperature Controller ...
Page 6: ......
Page 14: ...Model 350 Temperature Controller ...
Page 28: ...14 cHAPTER 1 Introduction Model 350 Temperature Controller ...
Page 53: ...Examples of PID control 2 13 4 ManualOutput 39 www lakeshore com FIGURE 2 4 ...
Page 58: ...44 cHAPTER 2 Cooling System Design and Temperature Control Model 350 Temperature Controller ...
Page 118: ...104 cHAPTER 5 Advanced Operation Model 350 Temperature Controller ...
Page 178: ...164 cHAPTER 7 Options and Accessories Model 350 Temperature Controller ...
Page 192: ...178 cHAPTER 8 Service Model 350 Temperature Controller ...