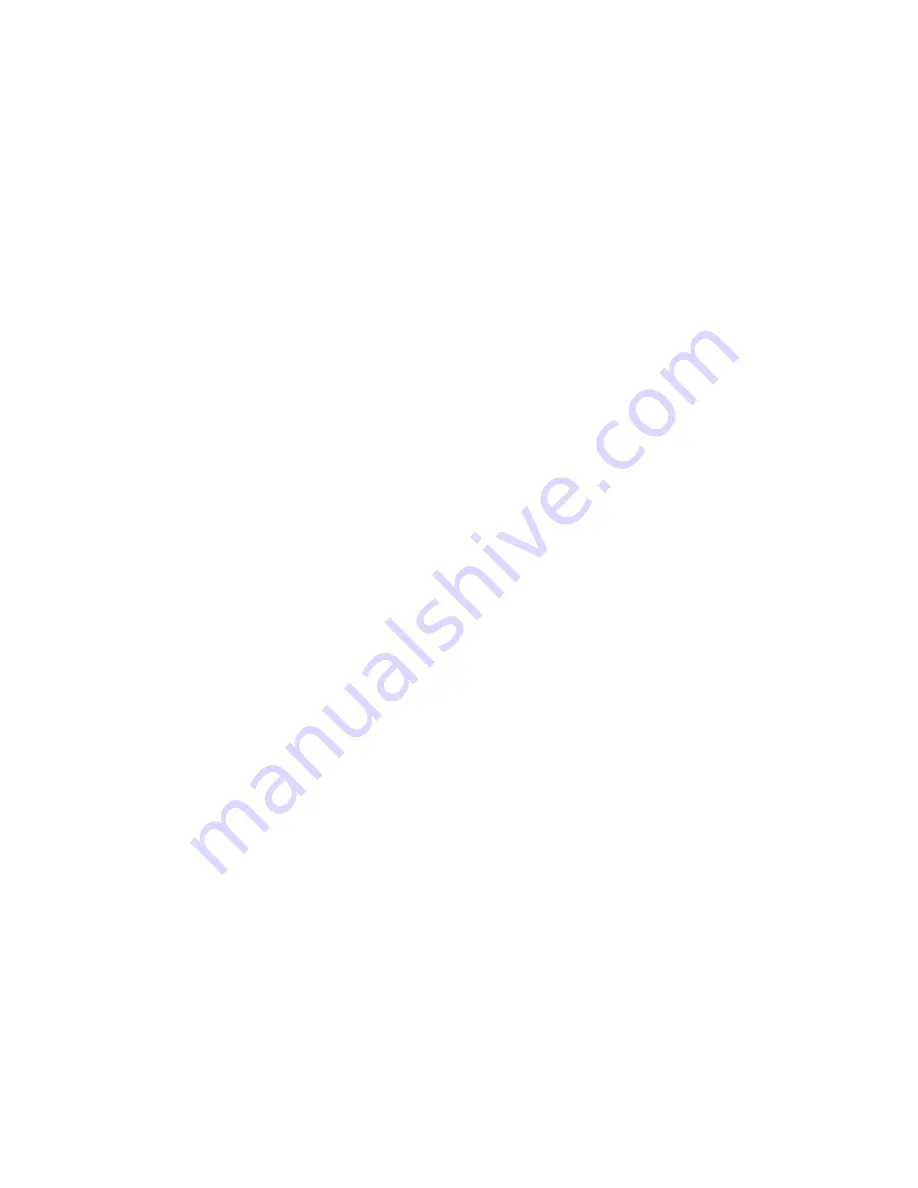
18
c
HAPTER
2:
Cooling System Design and Temperature Control
Model 350 Temperature Controller
4
He reservoir:
reservoir of liquid
4
He at atmospheric pressure that provides bulk cooling
down to 4.2 K. Pre-cools gasses entering the vacuum space and acts as a radiation
shield for refrigeration components.
Vacuum space:
insulates refrigeration components and provides a clear workspace.
1 K pot (
4
He evaporator):
pumped reservoir of
4
He maintained at 1 K. Used in the process
of condensing
3
He gas returning from pumping system. Also used as a heat sink for
measurement leads. Good location for a temperature sensor for cool down monitor-
ing and troubleshooting.
Heat exchangers:
one or more heat exchangers serve to cool returning
3
He liquid to
near the temperature of the
3
He evaporator. Also used to heat sink measurement
leads.
3
He Evaporator:
chamber where cooling action takes place. Liquid
3
He is pumped under
vacuum to reduce its boiling point to approximately 300 mK. This is the best location
for temperature control sensor and resistive heater. The heater output can control
temperature by driving the heater under closed loop PID control or open loop control.
Load (sample holder):
end of the
3
He evaporator where experiments can take place. May
either be part of or attached to the evaporator and is often designed for a unique pur-
pose. Requires a separate temperature sensor if its temperature is different from the
3
He evaporator.
2.4 Model 350
Theory of
Operation
This section explains sensor resistance measurements, excitation modes, resistance
ranges and measurement circuits. It also explains measurement speed and filtering
for the Model 350.
2.4.1 Sensor Resistance
Measurement
The Model 350 uses a four lead, AC square wave measurement technique to achieve
its accuracy with current excitations down to 10 nA.
The Model 350 uses current excitation because controlled current is very stable and
predictable. Current can also be scaled easily, which is necessary to achieve low exci-
tation. The Model 350 has 11 current settings from 1 mA down to 10 nA. These cur-
rents have low noise and almost no DC component to self-heat the sensor.
Precision sensor measurements use a four lead method to eliminate the effect of
nominal lead resistance. Excitation current is driven on one pair of leads while the
resulting signal voltage is measured on the second pair. Measurement errors from
lead resistance are proportional to current flowing in the voltage leads. Instrument
voltage inputs are expected to have high impedance to prevent the unwanted current
from flowing. The Model 350 has high input impedance to both normal mode volt-
ages (created by current source excitation) and common mode voltages (created by
induced noise on the leads).
Offset voltages occur in every electronic circuit both in signal amplifiers and in lead
wire connections that create thermal EMF voltages. Offset voltages affect accuracy
more when the excitation is small because they are a larger percentage of the mea-
sured voltage. Square wave reversing measurements allow higher amplifier gain and
greater sensitivity than DC techniques.
Summary of Contents for 350
Page 4: ...Model 350 Temperature Controller ...
Page 6: ......
Page 14: ...Model 350 Temperature Controller ...
Page 28: ...14 cHAPTER 1 Introduction Model 350 Temperature Controller ...
Page 53: ...Examples of PID control 2 13 4 ManualOutput 39 www lakeshore com FIGURE 2 4 ...
Page 58: ...44 cHAPTER 2 Cooling System Design and Temperature Control Model 350 Temperature Controller ...
Page 118: ...104 cHAPTER 5 Advanced Operation Model 350 Temperature Controller ...
Page 178: ...164 cHAPTER 7 Options and Accessories Model 350 Temperature Controller ...
Page 192: ...178 cHAPTER 8 Service Model 350 Temperature Controller ...