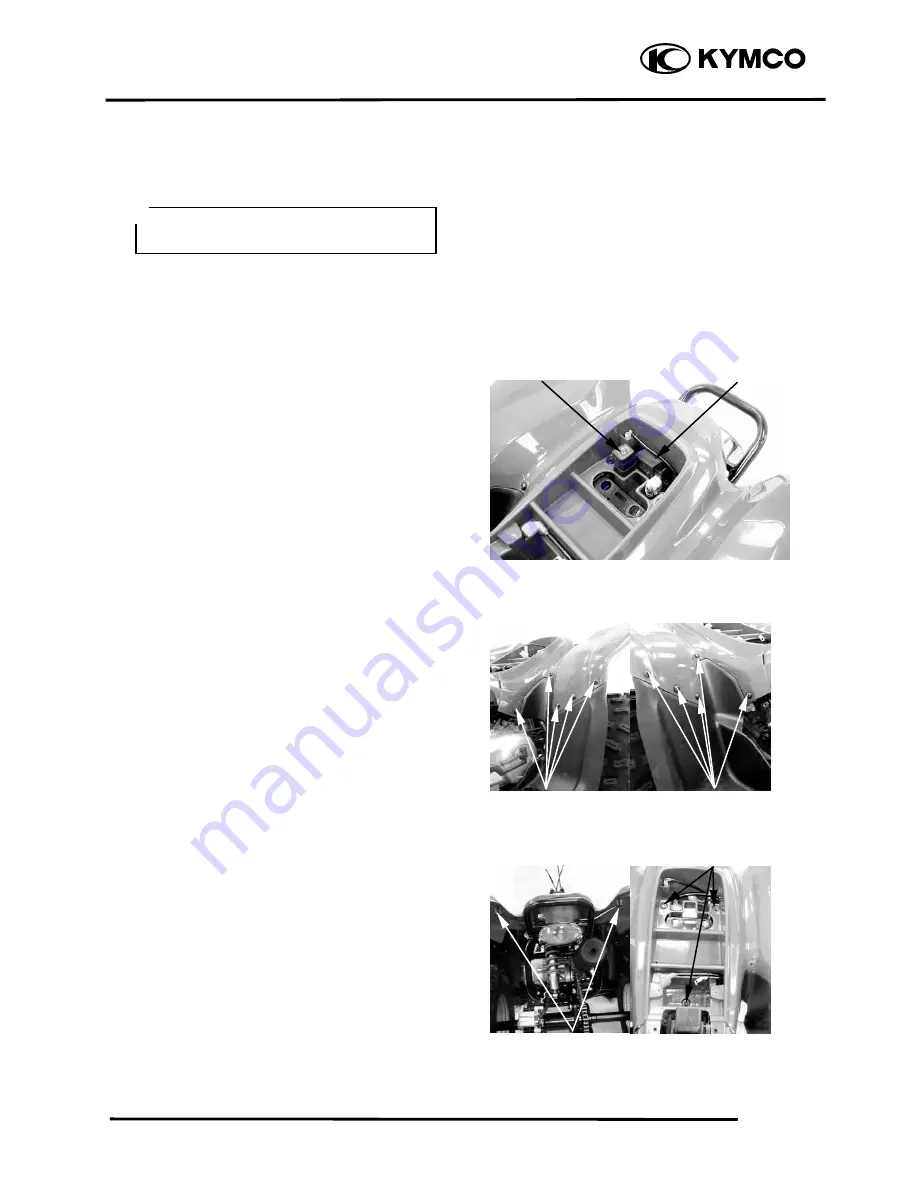
2
. FRAME COVERS/EXHAUST MUFFLER
2-6
INSTALLATION
Reverse the “FRONT FENDER
REMOVAL” procedures.
REAR FENDER REMOVAL
Remove the front fender. (See page 2-5)
Remove the battery.
(See chapter 14)
Remove the starter relay and CDI unit.
Remove the ten screws attaching the rear
fender and foot boards at the right/left side.
Remove the two screws attaching the rear
fender at the rear.
Remove the three bolts attaching the rear
fender at the center and then remove the
rear fender.
After remove, be sure to tighten the fuel
filler cap.
*
Starter Relay
Ignition Unit
Screws
Screws
Screws
Bolts
Summary of Contents for Mongoose 50-2T
Page 26: ...1 GENERAL INFORMATION 1 23 WIRING DIAGRAMS Mongoose 90 MXER 90R Mongoose 50 4T OFF ROAD G...
Page 27: ...1 GENERAL INFORMATION 1 24 MXER 90R ON ROAD...
Page 28: ...1 GENERAL INFORMATION 1 25 Mongoose 70...
Page 29: ...1 GENERAL INFORMATION 1 26 Mongoose 50 2T MXER 50R 2T OFF ROAD...
Page 30: ...1 GENERAL INFORMATION 1 27 MXER 50R 2T ON ROAD...
Page 38: ...2 FRAME COVERS EXHAUST MUFFLER 2 1...
Page 70: ...4 LUBRICATION SYSTEM 4 2 LUBRICATION SYSTEM 50cc 2T...
Page 88: ...5 FUEL SYSTEM 5 1...
Page 111: ...7 CYLINDER HEAD VALVES 90cc 70cc 50cc 4T 7 1...
Page 125: ...8 CYLINDER PISTON 8 1 90cc 70cc 50cc 4T...
Page 126: ...8 CYLINDER PISTON 8 2 50cc 2T...
Page 144: ...9 DRIVE AND DRIVEN PULLEYS 9 1...
Page 160: ...10 FINAL REDUCTION TRANSMISSION SYSTEM 10 1...
Page 167: ...11 CRANKCASE CRANKSHAFT 11 1 90cc 70cc 50cc 4T...
Page 168: ...11 CRANKSCASE CRANKSHAFT 11 2 50cc 2T...
Page 180: ...12 FRONT WHEEL FRONT BRAKE FRONT SUSPENSION STEERING SYSTEM 12 1...
Page 199: ...13 REAR WHEEL SWING ARM HYDRAULIC BRAKE 13 1...
Page 235: ...15 IGNITION SYSTEM 15 1 A C Generator Pulser Coil Spark Plug Ignition Coil...
Page 236: ...15 IGNITION SYSTEM 15 2 IGNITION CIRCUIT 90cc 70cc 50cc 4T IGNITION CIRCUIT 50cc 2T...