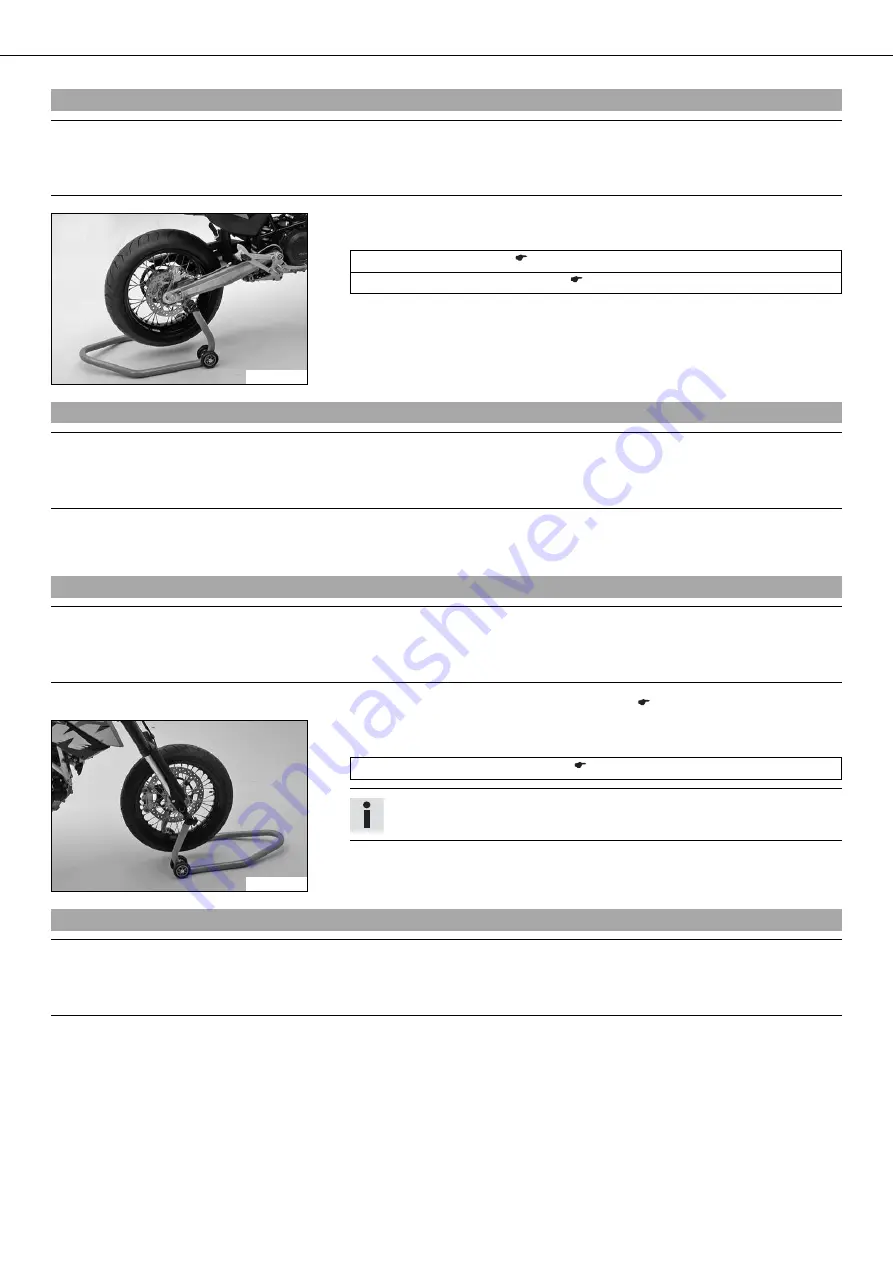
MOTORCYCLE
9
4.1
Raising the motorcycle with the rear wheel stand
Note
Danger of damage
The parked vehicle may roll away or fall over.
–
Always place the vehicle on a firm and even surface.
600492-01
–
Insert the adapter into the rear wheel stand and screw into the swingarm on both
sides.
Adapter (61029055110) (
Rear wheel stand (61029055100) (
–
Position the motorcycle upright, align the stand and raise the motorcycle.
4.2
Taking the motorcycle off of the rear wheel stand
Note
Danger of damage
The parked vehicle may roll away or fall over.
–
Always place the vehicle on a firm and even surface.
–
Secure the motorcycle against falling over.
–
Remove the rear wheel stand and lean the vehicle on the side stand.
4.3
Raising the motorcycle with the front wheel stand
Note
Danger of damage
The parked vehicle may roll away or fall over.
–
Always place the vehicle on a firm and even surface.
–
Raise the motorcycle with the rear wheel stand. (
600493-01
–
Move the handlebar to the straight-ahead position. Align the front wheel stand with
the fork legs using the adapters.
Front wheel stand (61029055300) (
Info
Always raise the rear of the motorcycle first.
–
Raise the front of the motorcycle.
4.4
Taking the motorcycle off of the front wheel stand
Note
Danger of damage
The parked vehicle may roll away or fall over.
–
Always place the vehicle on a firm and even surface.
–
Secure the motorcycle against falling over.
–
Remove the front wheel stand.
Summary of Contents for 690 SMC 2008
Page 1: ...REPAIR MANUAL 2008 690 SMC EU 690 SMC AUS UK 690 SMC USA Article no 3206042en...
Page 2: ......
Page 185: ...183...