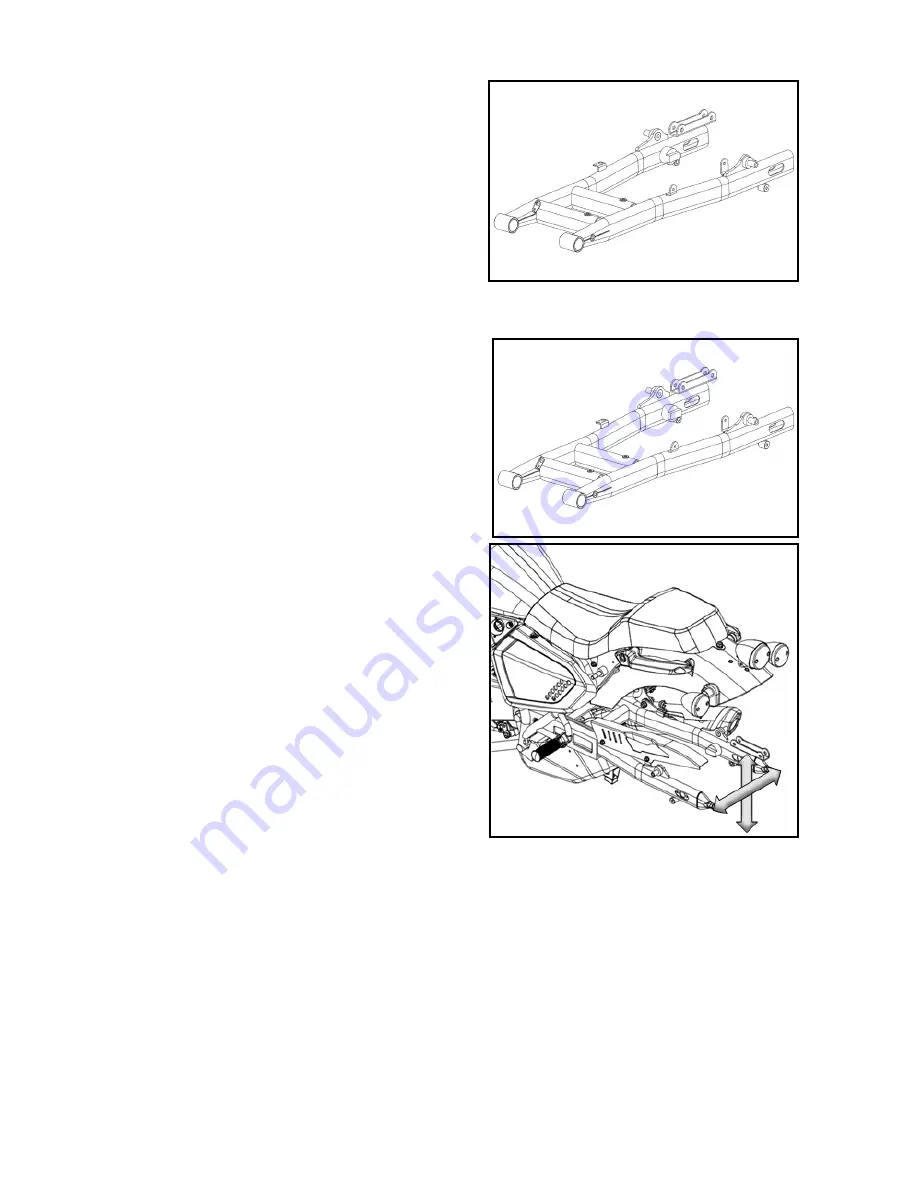
Remove
Rear rocker arm
8.5.2 Inspection
Check
Rear rocker arm
Bending/damage→replacement
Check
Tightness of rear rocker arm
If it is loose→tighten the rear rocker arm nut or
replace the collar
Vertical movement of rear rocker arm
If the movement is not smooth, or there is any
bent or rough parts → replace the axle sleeve
- 169 -
KS MOTORCYCLES - https://ksmotorcycles.com
Summary of Contents for K-LIGHT125
Page 1: ...Maintenance Manual of Two wheeled Motorcycle K LIGHT125 KS MOTORCYCLES https ksmotorcycles com...
Page 20: ...19 KS MOTORCYCLES https ksmotorcycles com...
Page 63: ...62 KS MOTORCYCLES https ksmotorcycles com...
Page 107: ...Front rear fluid brake 106 KS MOTORCYCLES https ksmotorcycles com...
Page 243: ...Emission Control 242 KS MOTORCYCLES https ksmotorcycles com...
Page 244: ...243 KS MOTORCYCLES https ksmotorcycles com...
Page 245: ...244 KS MOTORCYCLES https ksmotorcycles com...
Page 246: ...245 KS MOTORCYCLES https ksmotorcycles com...
Page 251: ...Electronic Injection Pars 250 KS MOTORCYCLES https ksmotorcycles com...