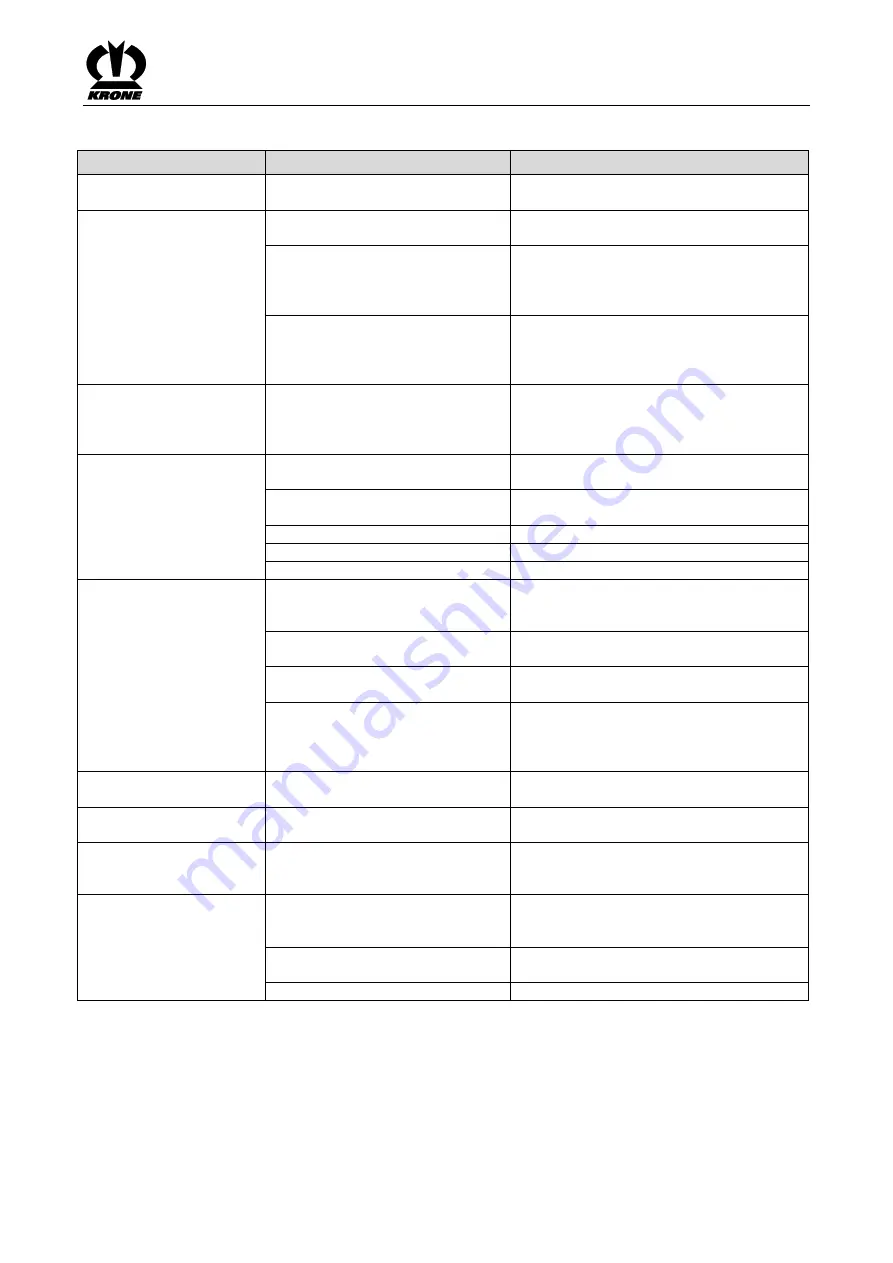
Malfunctions - Causes and Remedies
339
Pos: 56.5 /Überschriften/Überschriften 2/A-E/AAllgemei ne Stör ung en @ 24\mod_1241775122213_78.docx @ 248807 @ 2 @ 1
19.2
General malfunctions
Pos: 56.6 /BA/Störungen - Ursachen und Behebung/Rundballenpr essen/T abellarische Auflistung Allgemein Forti ma @ 235\mod_1394192969884_78.docx @ 1870010 @ @ 1
Malfunction
Possible cause
Remedy
Pick-up cannot be
lowered.
Hydraulic hose is not inserted.
Insert hydraulic hose into the appropriate
coupling.
Blockages in the feed
area. In case of
blockages, stop
immediately and turn off
the PTO shaft as the floor
conveyor strips can be
damaged otherwise.
Remove blockages.
Swaths are of uneven height or
too large.
Divide swaths.
Travelling speed too high.
Reduce travelling speed. Slow down at
the beginning of the baling process until
the picked up crop rolls in the bale
chamber.
The machine is not hitched
horizontally.
Hook in machine higher at the front.
Adjust drawbar height so that the transfer
from the pick-up to the channel is more
even.
The transfer of short crop
from pick-up to cutting
roller is poor.
The machine is too low at front.
Hook in machine higher at the front.
Adjust drawbar height so that the transfer
from the pick-up to the channel is more
even.
The wrapping material
tears in the middle if the
bales are barrel-shaped.
The bale chamber is filled
unevenly.
Drive over the swath on alternate sides.
The number of wrappings is too
low.
Increase number of wrappings.
Net brake is too tight.
Loosen net brake.
Net spreader is aggressive.
Adjust wide spreader.
Floor conveyor switches too late.
Change switching time.
Bale is formed conically.
The bale chamber is filled one-
sided.
Make sure when baling that the bale
chamber is filled evenly. Slow down
especially at the end of the bale.
Speed is too high at the end of
baling process.
Slow down at the end of baling process.
Twine or wrapping material torn.
Just use twine or wrapping material of
specified quality.
The number of wrappings is not
sufficient. Twine or wrapping
material loosens.
The tying distance of twine tying system
must be set closer or the number of
wrappings of the wrapping material must
be increased.
When starting, twine is
not shot in.
Pressure rollers on the starter are
too stiff.
Oil bearing or slightly loosen screw on
pressure rollers and lock them again.
Twine slips off the bale
edges.
Crop is very dry and crumbly.
Position twine limiter on tying unit further
to the inside.
Twine guide slide of
double tying is not
transported.
Chain of double tying is too loose. Retighten chain with chain tensioner.
Net tears off directly after
starting process or during
the wrapping process.
Blade bar has fallen down again
immediately after starting
process.
Remove impurities.
Setting of roller brake is too
strong.
Check setting of braking device.
Blade bar is too low.
Check blade bar setting.