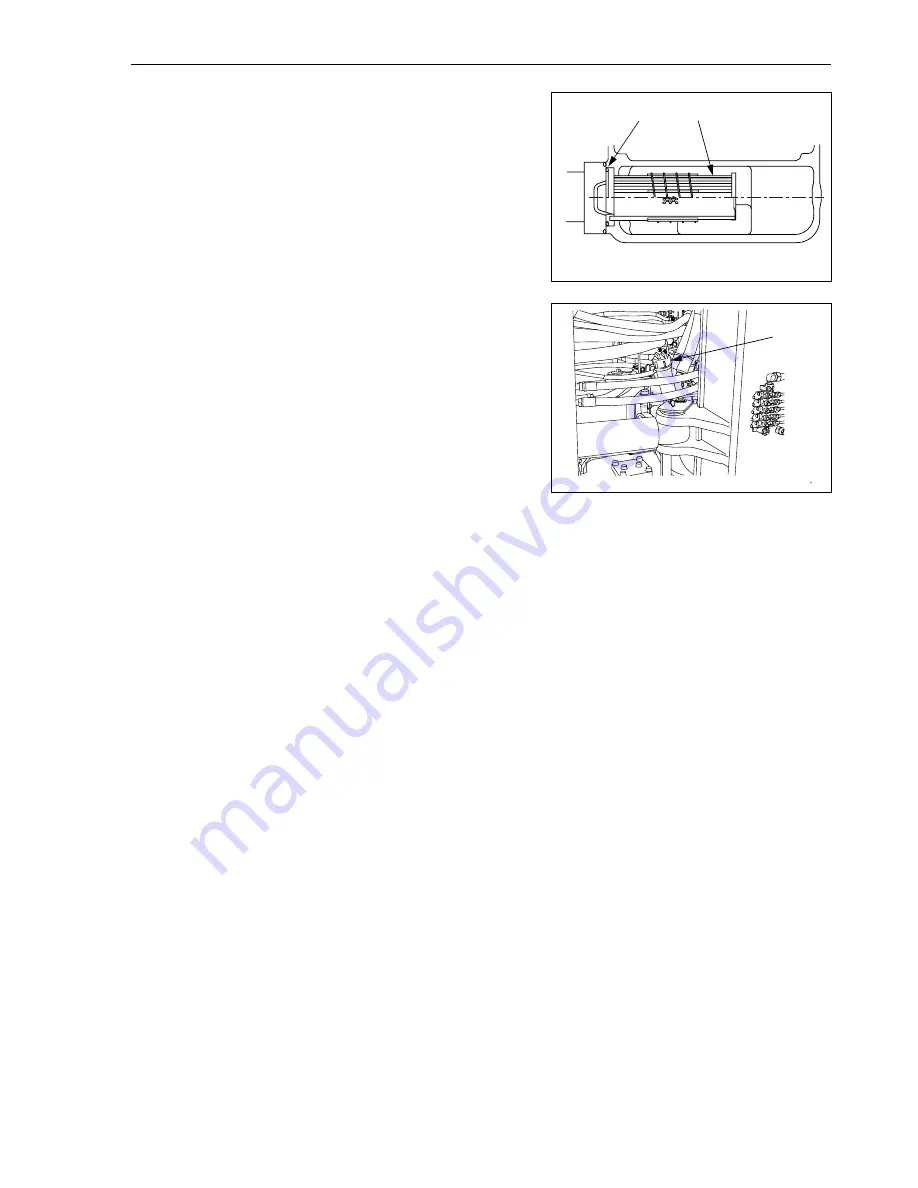
4.9 Service procedure
Maintenance
Every 1000 hours service
WA500-6H – VEAM430100
4-69
8. Pull out strainer (6).
9. Remove the dirt stuck to strainer (6), then wash in clean die-
sel oil or flushing oil. If strainer (6) is damaged, replace it
with a new part.
10. Install strainer (6), tube (5), and U-clamp (4), then tighten
bolts (3).
Replace O-ring (7) at the strainer portion with a new part,
then install the cover.
11. Pour in the specified amount of engine oil from oil filler (F).
12. After adding oil, check that the oil is at the specified level.
For details, see "Check transmission oil level, add oil (4-36)".
13. Check that there is no leakage of oil from the transmission
case or oil filter.
GK050242
7
6
GK050243
F
Summary of Contents for WA500-6H
Page 2: ......
Page 3: ...Foreword WA500 6H VEAM430100 1 1 1 Foreword...
Page 26: ...1 7 CE Conforming equipment Foreword 1 24 WA500 6H VEAM430100...
Page 254: ...3 7 Troubleshooting Operation 3 188 WA500 6H VEAM430100...
Page 344: ...4 9 Service procedure Every 12000 hours service Maintenance 4 90 WA500 6H VEAM430100...
Page 345: ...Technical Data WA500 6H VEAM430100 5 1 5 Technical Data...
Page 347: ...Technical Data 5 1 Technical data WA500 6H VEAM430100 5 3 GK032301 A B H I G C E F D...
Page 352: ...5 4 Limit values for slopes Technical Data 5 8 WA500 6H VEAM430100...
Page 401: ...Index WA500 6H VEAM430100 7 1 7 Index...
Page 407: ...Notes WA500 6H VEAM430100 8 1 8 Notes...
Page 408: ...Notes 8 2 WA500 6H VEAM430100...
Page 409: ...Notes WA500 6H VEAM430100 8 3...
Page 410: ...Notes 8 4 WA500 6H VEAM430100...
Page 411: ...Notes WA500 6H VEAM430100 8 5...
Page 412: ...Notes 8 6 WA500 6H VEAM430100...