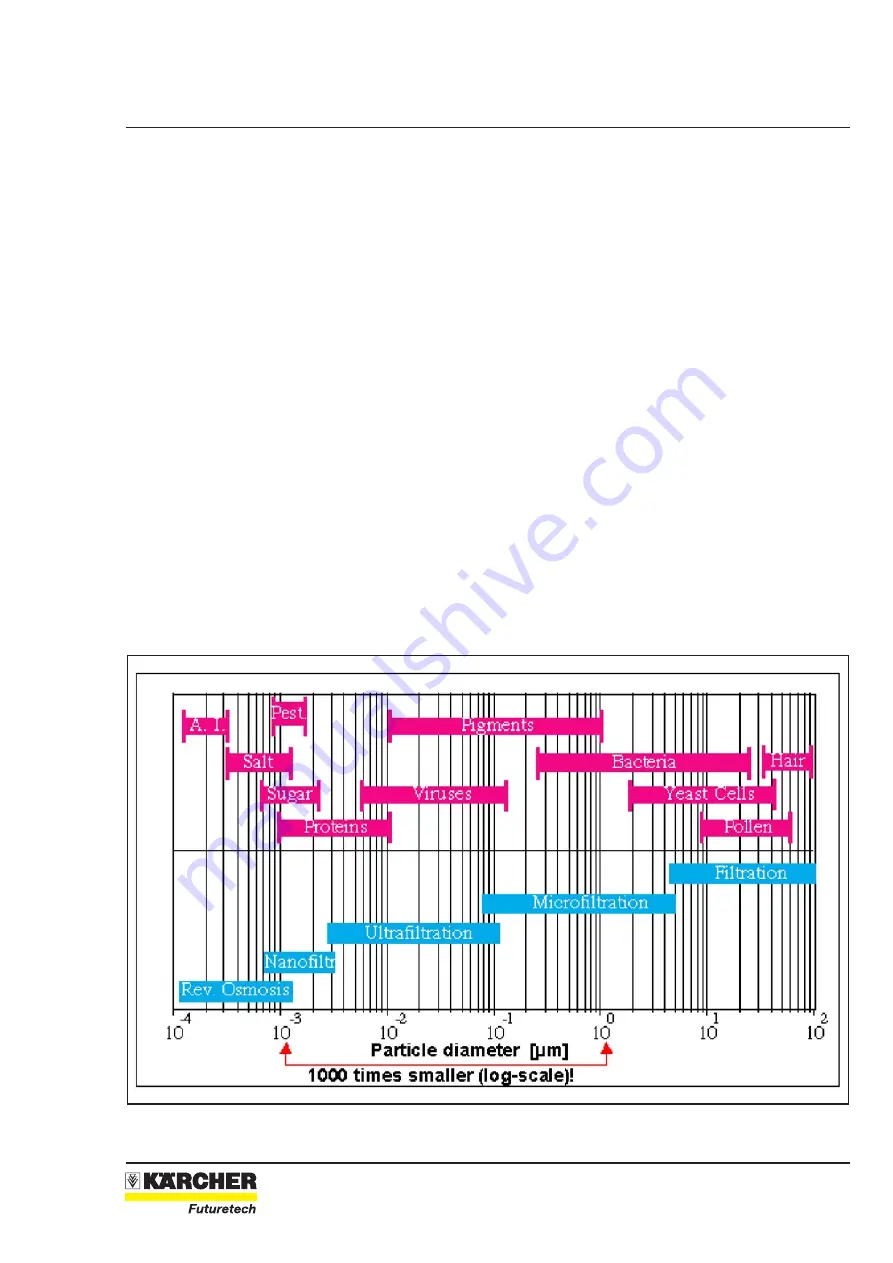
WATERCLEAN 1600
Version 03/2008
GENERAL
- 5 -
1.4
Raw Water
1.4.1
Types of Pollutants
The raw water can generally be polluted by:
1.
Biological contamination
• Bacteria, viruses, toxins
2.
Chemical contamination
• Inorganic salts (heavy metals, nitrates, asbestos, etc.)
• Organic compounds (benzenes, solvents, etc.)
• Pesticides, herbicides, etc.
3.
Salt in sea water and brackish water and other mineral salts and solid
matters
1.4.2
Retention Capabilities of the Waterclean 1600 System
The effective retention capability depends on the grade of contamination.
As standard, the WTC 1600 plant is equipped with reverse-osmosis
(RO) membrane. Optionally, nano-filtration (NF) spiral-wound memb-
ranes can also be installed in the pressure tubes. The retention capa-
city of the two different membrane types is indicated in the following
figure.
Summary of Contents for WATERCLEAN 1600
Page 2: ......
Page 14: ...GENERAL Version 03 2008 WATERCLEAN 1600 8 ...
Page 28: ...DESCRIPTION Version 03 2008 WATERCLEAN 1600 22 Fig 13 Anti scalant mounting kit 1 2 ...
Page 48: ...DESCRIPTION Version 03 2008 WATERCLEAN 1600 42 ...
Page 82: ...OPERATION Version 03 2008 WATERCLEAN 1600 76 ...
Page 106: ...APPENDIX Version 03 2008 WATERCLEAN 1600 100 ...
Page 108: ......
Page 110: ......