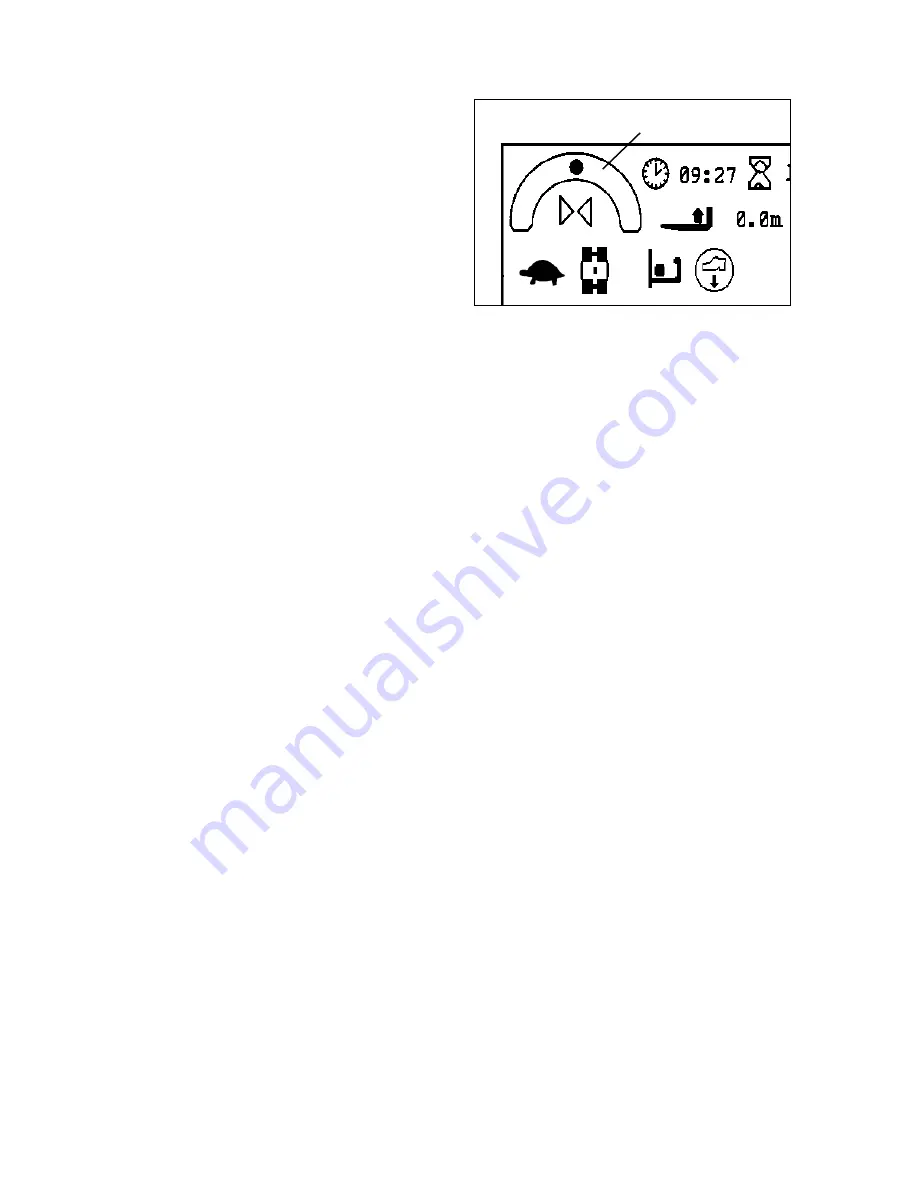
0306
.GB
E 16
4.2.2 Steering
The truck is steered outside of narrow
aisles with the steering wheel.
The drive wheel position is shown in the
display unit (14).
4.2.3 Braking
Z
The truck’s brake pattern depends largely on the ground conditions. The driver must
take this into consideration when handling the truck.
The truck can brake in one of three ways:
- with the service brake
- with the foot switch
- with the EMERGENCY DISCONNECT.
Braking with the service brake
While travelling, set the travel direction switch to the zero position or the opposite
travel direction; the traction controller will cause the truck to brake.
Braking with the foot switch
Releasing the foot switch causes the truck to brake.
Braking with the EMERGENCY DISCONNECT
Applying the EMERGENCY DISCONNECT will cause the truck to brake to a halt.
M
The EMERGENCY DISCONNECT must only be used in dangerous situations.
14
0306
.GB
E 16
4.2.2 Steering
The truck is steered outside of narrow
aisles with the steering wheel.
The drive wheel position is shown in the
display unit (14).
4.2.3 Braking
Z
The truck’s brake pattern depends largely on the ground conditions. The driver must
take this into consideration when handling the truck.
The truck can brake in one of three ways:
- with the service brake
- with the foot switch
- with the EMERGENCY DISCONNECT.
Braking with the service brake
While travelling, set the travel direction switch to the zero position or the opposite
travel direction; the traction controller will cause the truck to brake.
Braking with the foot switch
Releasing the foot switch causes the truck to brake.
Braking with the EMERGENCY DISCONNECT
Applying the EMERGENCY DISCONNECT will cause the truck to brake to a halt.
M
The EMERGENCY DISCONNECT must only be used in dangerous situations.
14
Summary of Contents for EKS 308
Page 1: ...Operating instructions 51009741 EKS 308 G 03 06 07 08...
Page 3: ...0108 GB...
Page 7: ...0708 GB I 4...
Page 9: ...0506 GB 2...
Page 11: ...0306 GB A 2...
Page 17: ...0708 GB B 6...
Page 23: ...0708 GB B 12...
Page 31: ...0306 GB C 8...
Page 87: ...0708 GB F 16...