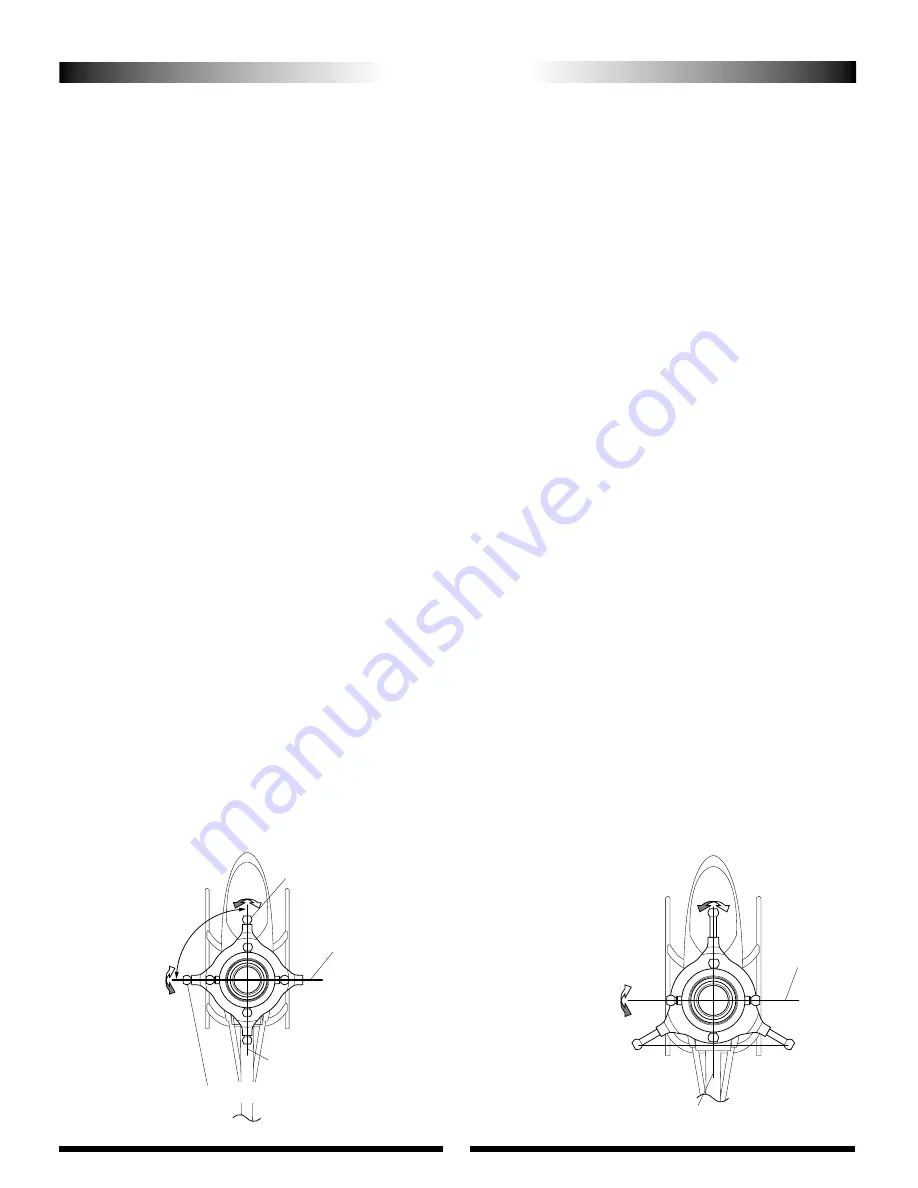
44
UNDERSTANDING SWASHPLATE CONTROL SYSTEMS
Currently, there are several different types of control systems
available on the market. Although the mechanical methods for
transferring control to the swashplate vary, the different control
systems can be broken down into two categories: 1 Servo
(conventional) and CCPM (Cyclic/ Collective Pitch Mixing).
The following is an explanation of the two most popular types of
swashplate control.
1. 1 Servo Standard Swashplate Control
The 1 Servo Standard System is found in a wide variety of radio
controlled helicopters. The term “1 Servo” means that the control
system requires one servo to operate each separate swashplate
function. With this system, a total of three servos is required to
operate the three main swashplate functions, which are aileron
(roll), elevator (pitch), and collective functions. With this type of
control system, each servo works independently and is assigned
to a specific function. In other words, the aileron (roll) servo is
assigned to move only the aileron (roll) function, as is the
elevator (pitch) servo, etc. Since these servos operate completely
independently of each other, the servo torque to each control
surface is limited to the maximum torque rating of the
servos used.
The 1 Servo Standard System swashplate is designed so that the
lower swashplate ring control balls are spaced at 90° to each
other. This system is also most commonly arranged so that the
aileron (roll) axis of the swashplate is positioned at 90° to the
main mechanics of the helicopter, and the elevator (pitch) axis is
parallel to the mechanics. Please refer to the diagram at right
for clarification.
With this type of system, it is necessary for the helicopter to be
designed using an intermediate mechanical mixing system so that
the control inputs can be transferred from the three independent
servos to the swashplate in such a manner that the three controls
can be achieved. This mechanical mixing system allows the
swashplate to both roll (aileron) and pitch (elevator), as well as
slide up and down the main rotor shaft for collective pitch inputs.
These mechanical mixing systems generally require the use of
many ball bearings and control rods to achieve this result.
2. 120 3-Servo CCPM Swashplate Mixing
The JR 120° CCPM or Cyclic/Collective Pitch Mixing System offers
the user a control system that can accomplish the same control
inputs as the 1 Servo Standard System mentioned above, but with
increased precision and reduced complexity.
The JR CCPM System utilizes three servos for the three main
controls: aileron (roll), elevator(pitch) and collective. The CCPM
lower swashplate ring is designed with only three control balls,
spaced at 120° from each other, hence the 120° CCPM
designation. Although the control balls are not at 90° as in the
Standard System, the aileron (roll) axis is still parallel to the main
mechanics of the helicopter, and the elevator (pitch) axis still
functions at 90° to the mechanics as does the 1 Servo System.
Please refer to the diagram below for clarification.
The main difference in the way that these two systems operate is
that unlike the 1 Servo System where the three servos work
completely independent from each other, the CCPM Systems work
as a team to achieve the same control inputs. For example, if an
aileron (roll) input is given, two servos work together to move the
swashplate left and right. If an elevator (pitch) input is given, all
three servos work together to move the swashplate fore and aft.
For collective, it’s also the strength of three servos that will move
the swashplate up and down the main rotor shaft. With two to
three servos working at the same time during any given control
input, servo torque is maximized and servo centering is also
increased. In addition to these benefits, CCPM achieves these
control responses without the need for complex mechanical
mixing systems that require many more control rods and parts
to set up.
This amazing CCPM control is achieved through special CCPM
swashplate mixing that is preprogrammed into many of today’s
popular radio systems. Since the 120° CCPM function is
preprogrammed, CCPM is no more complicated to set up than a
conventional 1 Servo Standard System. When you factor in the
reduced parts count and easy programming, CCPM is actually
easier to set up and operate than many conventional systems.
For JR radio owners, please refer to the radio information
contained at the front of this manual or on the following page to
determine if your radio
system has the
CCPM function.
For other brands
of radio systems,
please contact the
radio manufacturer
for CCPM
information.
Please note that it
is not possible to
program a non-
CCPM radio
system for
CCPM operation.
Elevator control ball is in
line with helicopter frame
Aileron Axis
Elevator Axis
Aileron control ball
is 90° to elevator
control ball and
helicopter frame
Standard “1 Servo” Swashplate System
Elevator Axis
Aileron Axis
JR 120° 3 Servo CCPM Control System
120°
JRP9012.46 Robinson R22 Manual 10/6/00 5:06 PM Page 44