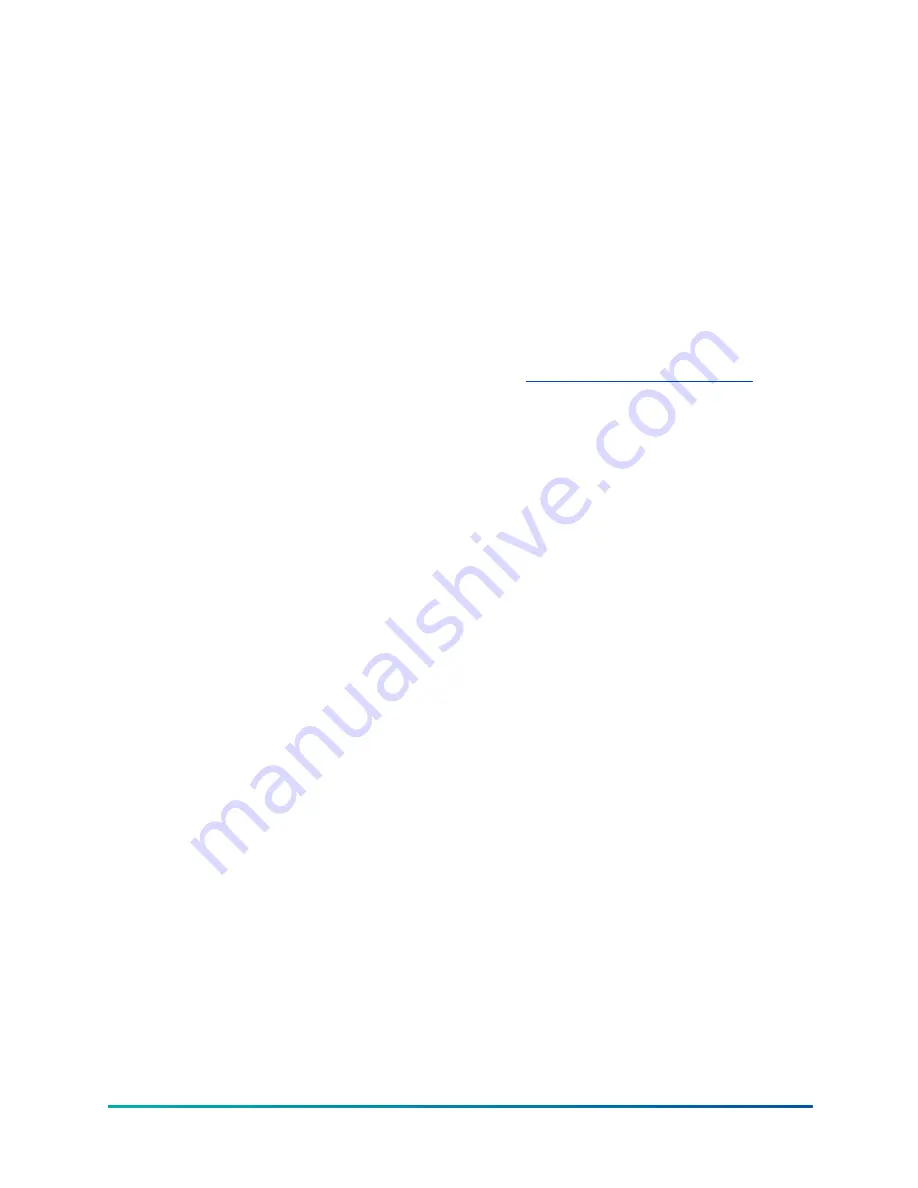
(2)
More frequent service may be required depending on local operating conditions.
For operating and maintenance requirements listed above, refer to appropriate service literature,
Form 160.88-MR1
, or contact your local Johnson Controls Service Office.
Electrical isolation
1. Isolate electrical power supply to the chiller from the facility.
2. Isolate the power panel battery from the uninterrupted power supply (UPS) by opening the
power panel disconnect switch.
3. Isolate plant fluid flow to the chiller at appropriate valves or have refrigerant isolated to
prevent free-wheeling the driveline and generating electrical energy from the permanent
magnet rotor.
Renewal parts
For any required renewal parts, refer to HVAC Navigator at
Operating inspections
By following a regular inspection using the display readings of the OptiView Control Center and a
maintenance procedure, the operator can avoid serious operating difficulty. Use the following list of
inspections and procedures as a guide for maintenance.
Weekly
1. Check the OptiView™ Control Center displays.
2. Check the entering and leaving chilled liquid temperatures and evaporator pressure for
comparison with the job design conditions. Chilled liquid temperatures can be checked on
the System screen.
3. Check the condenser saturation temperature on the System screen. The condenser
saturation temperature is based on condenser pressure sensed by the condenser transducer.
4. Check the compressor discharge temperature on the System screen. During normal
operation, make sure that the discharge temperature does not exceed 220°F (104°C).
5. Check the compressor motor current on the System screen.
6. Check for any signs of dirty or fouled condenser coils. Make sure that the temperature
difference between air temperature leaving condenser and the saturated condensing
temperature does not exceed the difference recorded for a new unit by more than 4°F (2.2°C).
Monthly
1. Leak check the entire chiller.
2. Check the condenser coils and Variable Speed Drive cooling coils for any evidence of dirt or
debris that might block air flow.
Semi-annually
Check the controls semi-annually, or more often, as required.
YVAM Control Center
122
Summary of Contents for YORK YVAM 0350
Page 2: ...2 YVAM Control Center...
Page 10: ...Figure 4 Variable speed drive nomenclature YVAM Control Center 10...
Page 15: ...Figure 8 System piping and instrumentation diagram P ID 15 YVAM Control Center...
Page 154: ...Figure 62 Sample printout status or history YVAM Control Center 154...
Page 155: ...Figure 63 Sample printout status or history continued 155 YVAM Control Center...
Page 156: ...Figure 64 Sample printout setpoints YVAM Control Center 156...
Page 157: ...Figure 65 Sample printout setpoints continued 157 YVAM Control Center...
Page 158: ...Figure 66 Sample printout schedule YVAM Control Center 158...
Page 159: ...Figure 67 Sample printout sales order 159 YVAM Control Center...
Page 160: ...Figure 68 Sample printout security log report YVAM Control Center 160...