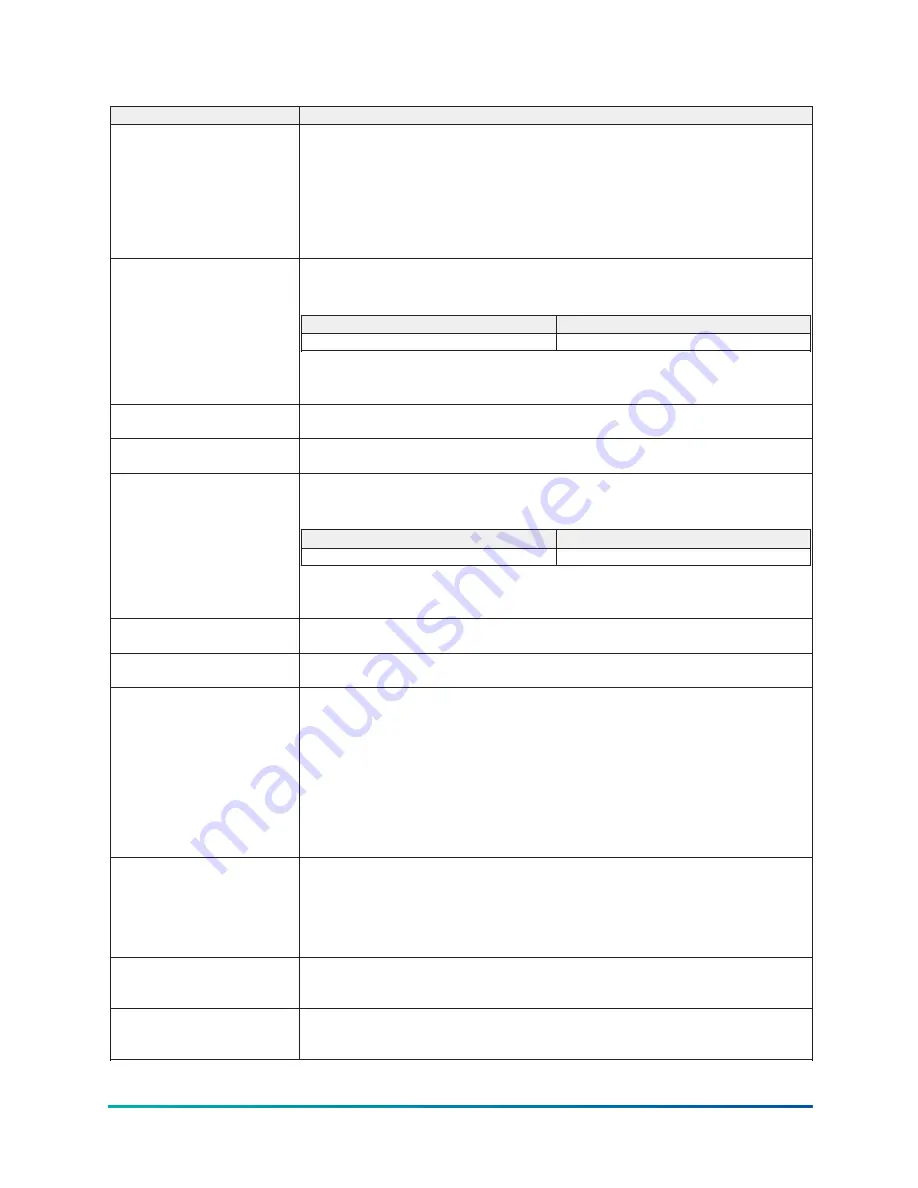
Table 91: Cycling shutdown messages
Message
Description
VSD – HIGH INTERNAL
AMBIENT TEMPERATURE
The variable speed drive contains two temperature sensors, which monitor the unit’s
internal ambient temperature. This shutdown is generated when the higher of the two
ambient temperatures exceeds a high limit of 158°F (70°C). The unit’s fan(s) and water
pump(s) remain energized until the internal temperature drops below 148°F (64°C), after
which they shall be de-energized and the fault can be cleared. Some potential causes
for this shutdown are internal drive fan failure, drive coolant pump failure, entering
condenser water temperature higher than design, condenser water flow lower than
required, fouled drive heat exchanger, or restriction of condenser water to the drive.
VSD – HIGH PHASE A INPUT
CURRENT
If the A phase input current exceeds the value for the given model of drive, then a cycling
shutdown occurs. If three high input current cycling shutdown faults occur on any phase
within 90 minutes, the third fault in the 90 minute period causes a Safety Shutdown.
Drive model
Input current fault value
0490B
942 Amps
If the safety shutdown occurs, the chiller can be restarted after the Clear Faults button is
pressed.
VSD – HIGH PHASE B INPUT
CURRENT
See the previous message,
VSD – HIGH PHASE A INPUT CURRENT
VSD – HIGH PHASE C INPUT
CURRENT
See the previous message,
VSD – HIGH PHASE A INPUT CURRENT
VSD – HIGH PHASE A MOTOR
CURRENT
If the A phase motor current exceeds the value for the given model of drive, then a cycling
shutdown occurs. If three high motor current cycling shutdown faults occur on any phase
within 90 minutes, the third fault in the 90 minute period causes a Safety Shutdown.
Drive model
Motor current fault value
0490B
776 Amps
If the safety shutdown occurs, the chiller can be restarted after the Clear Faults button is
pressed.
VSD – HIGH PHASE B MOTOR
CURRENT
See the previous message,
VSD – HIGH PHASE A MOTOR CURRENT
.
VSD – HIGH PHASE C MOTOR
CURRENT
See the previous message,
VSD – HIGH PHASE A MOTOR CURRENT
.
VSD INITIALIZATION FAILED
When power is connected, all boards go through the initialization process. At this
time, memory locations are cleared, program jumper positions are checked, and serial
communications links are established. If this process is not completed, the OptiView panel
indicates this fault. There are several causes for an unsuccessful initialization as follows:
•
Serial data communications must be established. If communications between
the drive logic board and control center Microboard does not take place during
initialization, this message will be generated. The Serial communications can be
verified by selecting the VSD Details screen from the Motor screen and observing
the Full Load amps value. A zero displayed for this and other variable speed drive
parameters, indicates a serial communications link problem.
VSD – INVALID SETPOINTS
The drive logic board is able to determine which model of drive can run which model of
motor. If the Control Center provides a model of motor that is not compatible with this
model of variable speed drive, then this shutdown is generated. This shutdown is also
generated when the measured line frequency does not match the programmed input
frequency from the Control Center. When this condition clears, the chiller can be started
after the Clear Faults button is pressed.
VSD – LINE VOLTAGE PHASE
ROTATION
The input voltage to the drive is not phase rotation sensitive, but the drive must be able to
determine the correct input phase rotation. If the drive logic board cannot determine the
correct phase rotation, then this shutdown is generated.
VSD – LOGIC BOARD POWER
SUPPLY
This shutdown is generated by the drive logic board and it indicates that the low voltage
power supplies for the logic boards have dropped below their allowable operating limits.
This message usually means the power to the variable speed drive has been removed.
YVAM Control Center
98
Summary of Contents for YORK YVAM 0350
Page 2: ...2 YVAM Control Center...
Page 10: ...Figure 4 Variable speed drive nomenclature YVAM Control Center 10...
Page 15: ...Figure 8 System piping and instrumentation diagram P ID 15 YVAM Control Center...
Page 154: ...Figure 62 Sample printout status or history YVAM Control Center 154...
Page 155: ...Figure 63 Sample printout status or history continued 155 YVAM Control Center...
Page 156: ...Figure 64 Sample printout setpoints YVAM Control Center 156...
Page 157: ...Figure 65 Sample printout setpoints continued 157 YVAM Control Center...
Page 158: ...Figure 66 Sample printout schedule YVAM Control Center 158...
Page 159: ...Figure 67 Sample printout sales order 159 YVAM Control Center...
Page 160: ...Figure 68 Sample printout security log report YVAM Control Center 160...