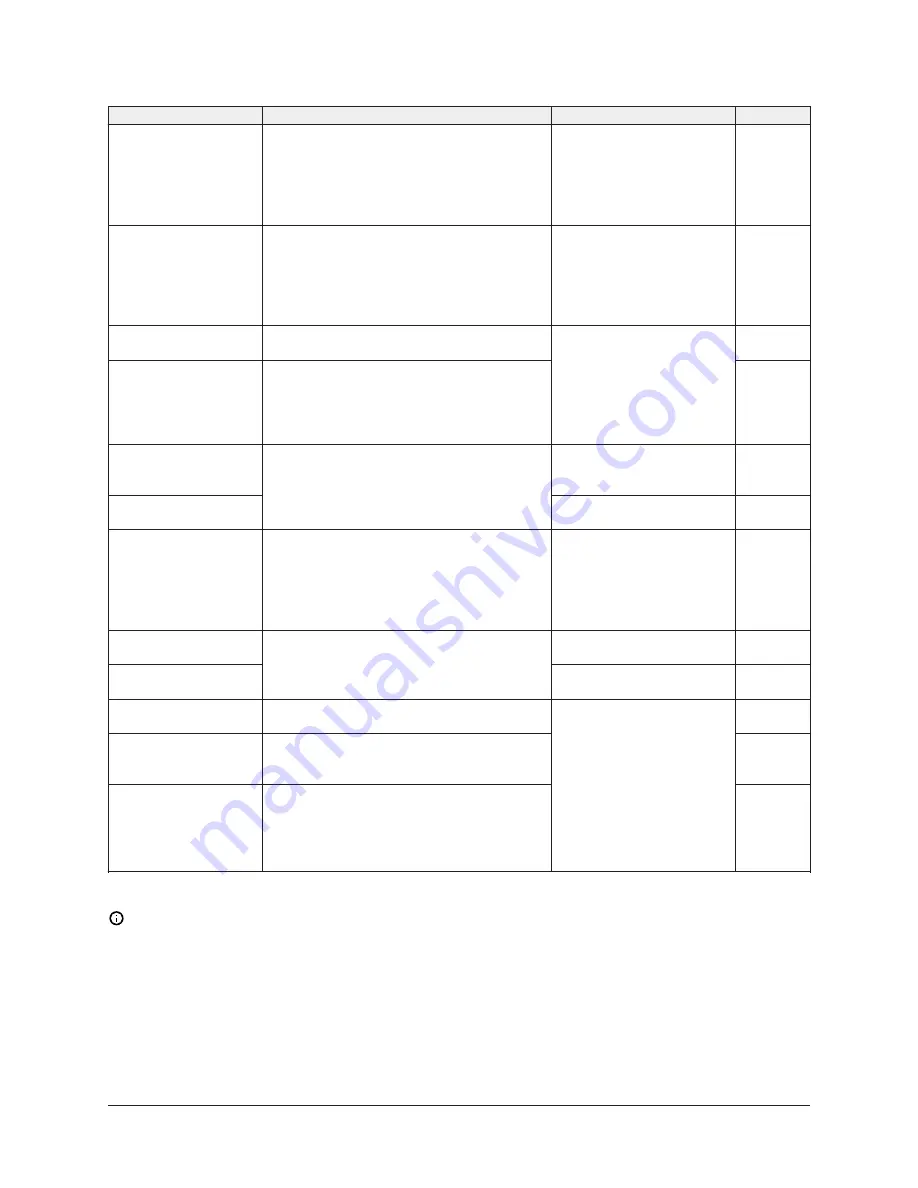
Table 33: Maintenance and inspection
Task
Contents
Frequency
Scope
Addition of surface active
agent
As surface active agent is discharged out of
the machine gradually each time purging is
performed, new agent must be added. If too
much surface active agent is added, it will have
the opposite effect. Add approximately 700 cc per
year.
1 year
S
Filtration and refining of
solution
As the inside of the chiller-heater is corroded,
corrosion particles are increased. Particles
accumulated on the heat exchange tube surfaces
lower the heat exchange rate, that is, the
performance. Accordingly, filter the solution as
directed.
5-6 years
S
Check of operation of
various safety relays
Check the operation of the safety relays.
S
Cleaning of tubes with
brush or water jet
(absorber, condenser)
If foreign matter sticks to the inside of the tubes
of the chiller-heater, refrigerating performance
is lowered and the tubes become corroded.
Accordingly, remove slime, soft scales, and other
foreign matter from the inside of the tubes.
Yearly
S
Chemical cleaning
of tubes (Absorber,
condenser)
Every 2 years
1
S
Chemical cleaning of
tubes (Evaporator)
Since hard scales sticking to the tubes cannot be
removed with a brush or water jet, remove them
chemically, depending on the condition.
Every 4 years
S
Check for slight leakage
Vacuum and airtightness must be maintained
to ensure the reliability and performance of
the absorption chiller-heater. Accordingly,
recommend that the machine should be checked
for slight leakage with a special vacuum and
airtightness diagnostic device.
Every 2 years
S
Eddy current test on tubes
(Absorber, condenser)
Every 4 years or 10,000 hours
S
Eddy current test on tubes
(Evaporator)
Check the inside of the tubes for corrosion caused
by bad quality chilled/hot water, and cooling
water.
Every 6 years
S
Check for leakage of gas
shut-off valves.
Check for leakage to outside and passing through
the valve sheets.
S
Check operation of
combustion system
Check the operation of the ignition system, air
damper, fuel gas damper, capacity control motors,
burner fan, and protect relay (burner controller).
S
Check and adjust
combustion
Measure the concentration of O
2
and CO. Adjust
it if necessary to ensure suitable and efficient
combustion.
Collect the combustion data. Check the data
collected during the commissioning.
Every 6 months
S
1
Note:
*If water quality analysis indicates necessity.
Note:
C = Customer, S = Johnson Controls Service
Refrigerant pump manual stop
The refrigerant pump can be stopped manually for maintenance purposes. It can be stopped even
while the chiller-heater operates.
1. Navigate to the setting screen on the control panel.
2. Press the refrigerant pump
Stop
button.
157
Model YHAU-CGN/H-CXR(M)Double Effect Direct Fired Small Absorption Chiller-Heater