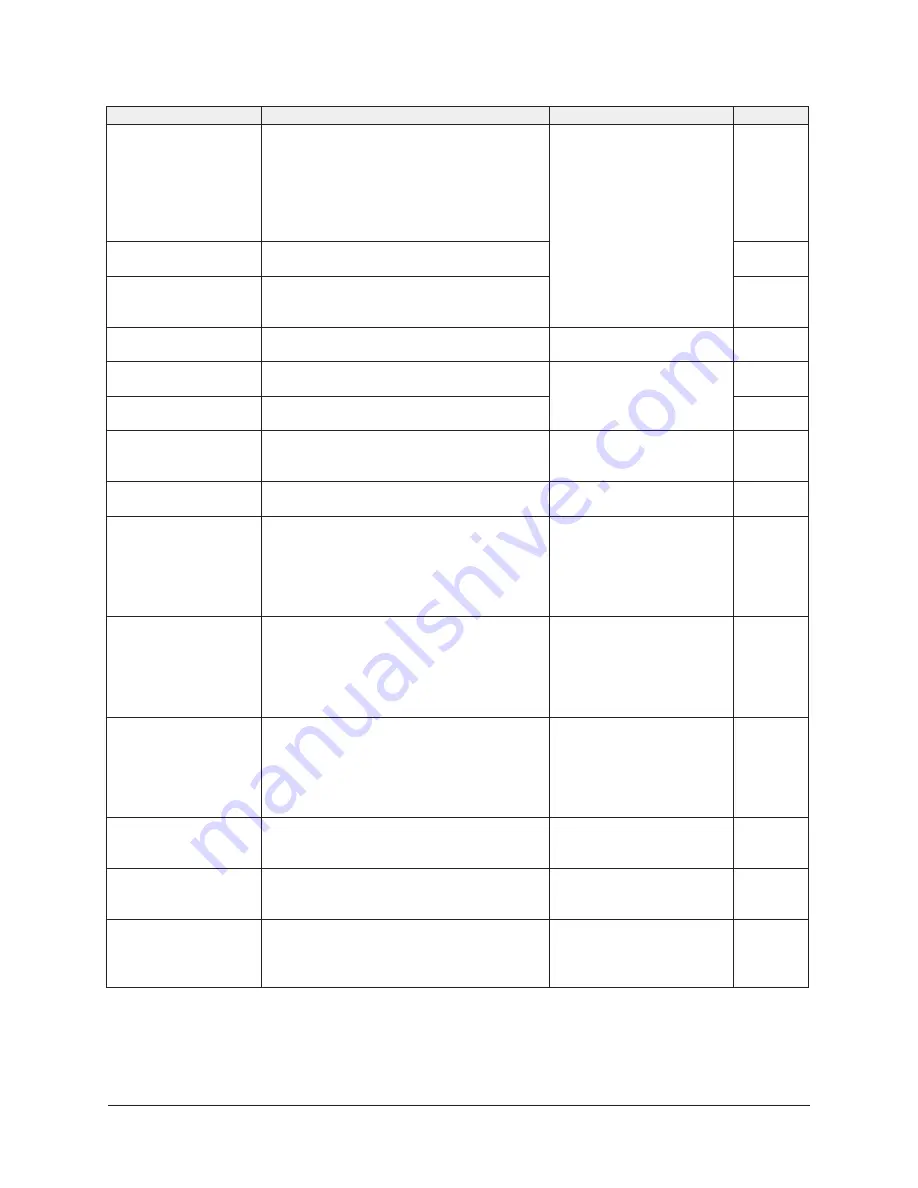
Table 33: Maintenance and inspection
Task
Contents
Frequency
Scope
Measurement of
insulation resistance of
electric devices
Measure the insulation resistance of the main
circuit and motors (solution pump, refrigerant
pump) mainly to check for lowering of insulation.
When measuring the insulation resistance,
disconnect the wires of the temperature controller
and other relevant controllers that can cause
interference.
S
Check of terminals for
looseness
Check each terminal in the control panel for
looseness.
S
Check of operation of
control panel
Check the operation of the control panel to
prevent troubles caused by malfunction of the
control panel.
Yearly
S
Check of capacity of purge
unit
purge unit.
Monthly
S
Check of leakage through
purge solenoid valves
By measuring vacuum down speed, check for
leakage through purge solenoid valves.
S
Overhaul check of purge
solenoid valves
Perform overhaul of purge solenoid valves.
Yearly
S
Check of airtightness
Measure the quantity of non-condensable gas
discharged from the water ejector or additional
service vacuum pump.
Every 2-3 months
S
Check continuity of
protective bonding circuit Check continuity of protective bonding circuit.
Yearly
S
Analysis of quality of
chilled/hot water, and
cooling water
Reliable water treatment companies are available
in most larger cities to supply a water treating
process which will greatly reduce the corrosive
and scale forming properties of almost any type of
water. Request the first analysis within one month
after the test operation is started.
Every 2-3 months
C
Check of quantity of
solution and refrigerant
The solution is not consumed, but the refrigerant
is discharged little by little each time purging
is performed. If the quantity of the refrigerant
becomes insufficient, the condensation preventive
function does not work normally. Accordingly,
check the quantity of the refrigerant.
Yearly (during operation at
100%)
S
Disassembly inspection
and cleaning of solution
pump and refrigerant
pump
Sleeve bearings are used for the solution pump
and refrigerant pump, and they are normally
lubricated with water solution of lithium bromide
and refrigerant. Excessive wear can cause a pump
problem. To prevent this, disassemble and inspect
them. The internal strainer must also be cleaned.
2-3 years or 8,000 hrs
S
Replacement of gaskets of
airtight parts
Replace the gaskets of the airtight parts to
maintain the airtightness of the absorption chiller-
heater.
4 years
S
Inspection of cooling
waterbox and
replacement of gasket
Open the waterbox cover periodically. Check the
inside paint for damage, and check the inside of
the tubes for scales.
Every 1 year
S
Analysis of solution and
addition of inhibitor
The concentration of the inhibitor must be kept
proper to prevent corrosion of inside parts.
Analyze the solution to detect leakage in the early
period.
Every 6 months
S
Model YHAU-CGN/H-CXR(M)Double Effect Direct Fired Small Absorption Chiller-Heater
156