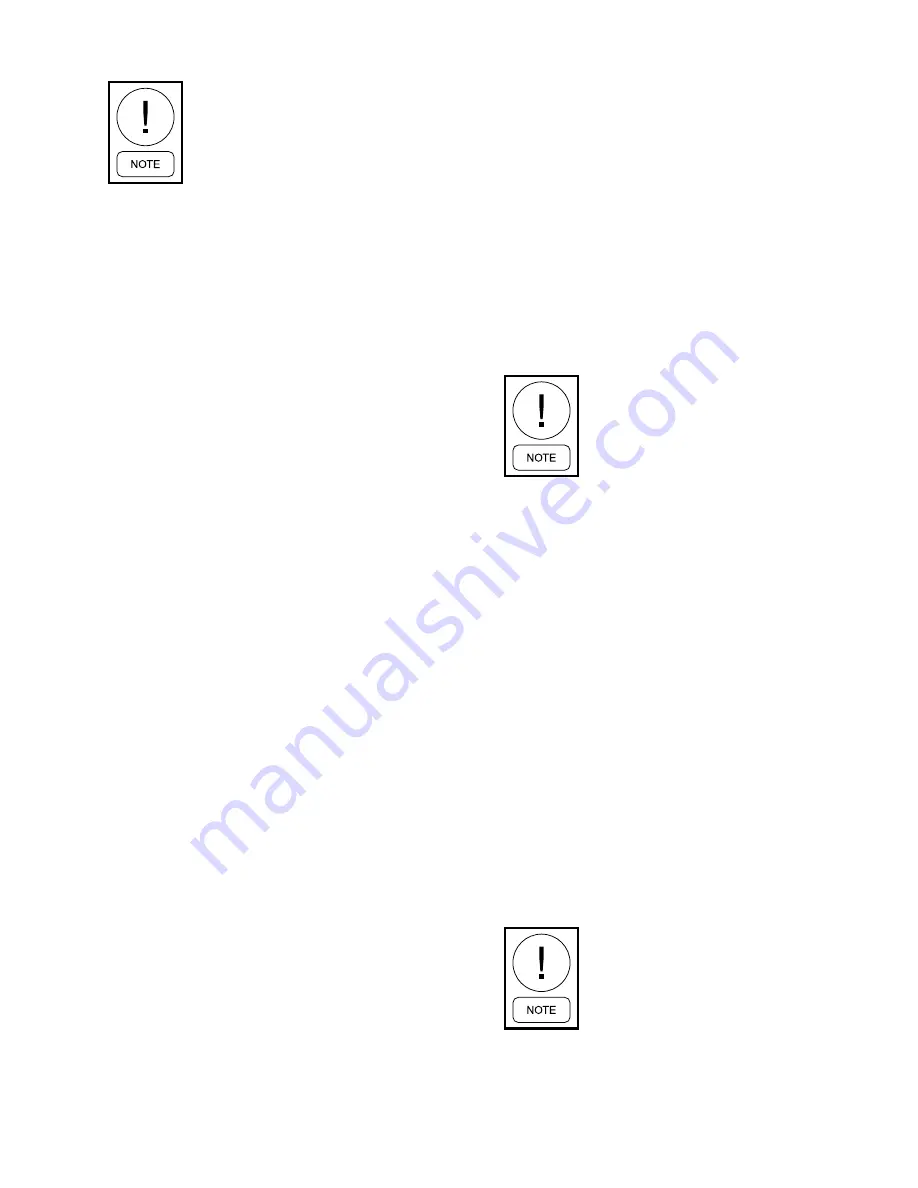
JOHNSON CONTROLS
83
SECTION 2 – INSTALLATION
FORM 145.05-NOM7
ISSUE DATE: 10/31/2019
To avoid confusion between “high” and
“low” tubing, it is recommended that two
different tubing colors be used and that
this information be recorded, along with
the sensing point location, on the master
building blueprints.
DUCT HIGH PRESSURE SAFETY SWITCH
The unit can be ordered with a Duct High Pressure
Safety Switch. The switch contains an adjustable dif-
ferential pressure switch that monitors the pressure be-
tween the positive pressure in the blower compartment
and atmosphere. The switch has a range of 0.08 to 4.0
"W.C. There is a tap with a 1/8 inch FNPT thread on
the post to the right of the control compartment. A fac-
tory tube is connected between this fitting and the low
side of the switch. If the equipment room is used as
a return, an adapter should be installed in this fitting
and tubing run outside the equipment room. See
for operation.
DIRTY FILTER SWITCH
The unit can be ordered with a Dirty Filter Switch.
The switch contains an adjustable differential pressure
switch that monitors the pressure drop across the filter.
The switch has a range of 0.08 to 4.0 "W.C. There is
a tap with a 1/8 inch FNPT thread on the corner post
on the right hand side of the unit. A factory tube is
connected between this fitting and the low side of the
switch. If the equipment room is not being used as a
return, an adapter should be installed in this fitting and
tubing run to the return duct.
When the pressure drop across the filters exceeds the
setting of the switch, the switch closes sending a 24-
volt signal to the Unit Controller. The Unit Controller
posts a warning in the service memory buffer; but does
not shut down the unit. The factory default setting for
the Dirty Filter Switch is 1.0 "W.C.
STATIC PRESSURE TRANSDUCER
INSTALLATION (FLEXSYS
™
UNITS ONLY)
All FlexSys units include a factory mounted static pres-
sure sensor (SPS1). The unit can also have an option
-
al second static pressure sensor, (SPS2). The second
static pressure sensor would be used to get an average
of the static pressure in the under floor space. When
two static pressure sensors are used the control can be
programmed to maintain the lowest input, highest in-
put, or the average of the two inputs. The sensors are
factory wired and require field installation of 1/4 inch
ID sensor tubing to the selected under floor location. A
field supplied static pressure probe and tubing must be
field installed prior to the start up of the unit.
Be sure that tubing complies with lo-
cal code requirements. Flame retardant
plastic or metal tubing may be required.
Carefully select the ductwork sensing
point for the pressure sensor. Improper
location of the sensing point results in
unsatisfactory operation of the entire
variable air volume system.
Installation Instructions
1. Run the tubing from the duct static probe in the
underfloor space back to the unit. This tube should
be connected to the high port on the transducer.
2. A second tube must be run and positioned in an
area that provides an atmospheric reference to the
low side port of the transducer. This is particularly
critical on units where the equipment room is used
as the return.
3.
The duct static transducer(s) (see
) are located in a compartment below
the supply air blower and to the left of the control
compartment. The tubing can be routed through a
7/8" hole in the top the control enclosure, down the
left side of the control compartment and through
the partition to the duct static transducer(s). Make
sure to use tie-wraps to keep the pneumatic tubing
away from the electrical components and wiring.
To avoid confusion between “high” and
“low” tubing, it is recommended that two
different tubing colors be used and that
this information be recorded, along with
the sensing point location, on the master
building blueprints.