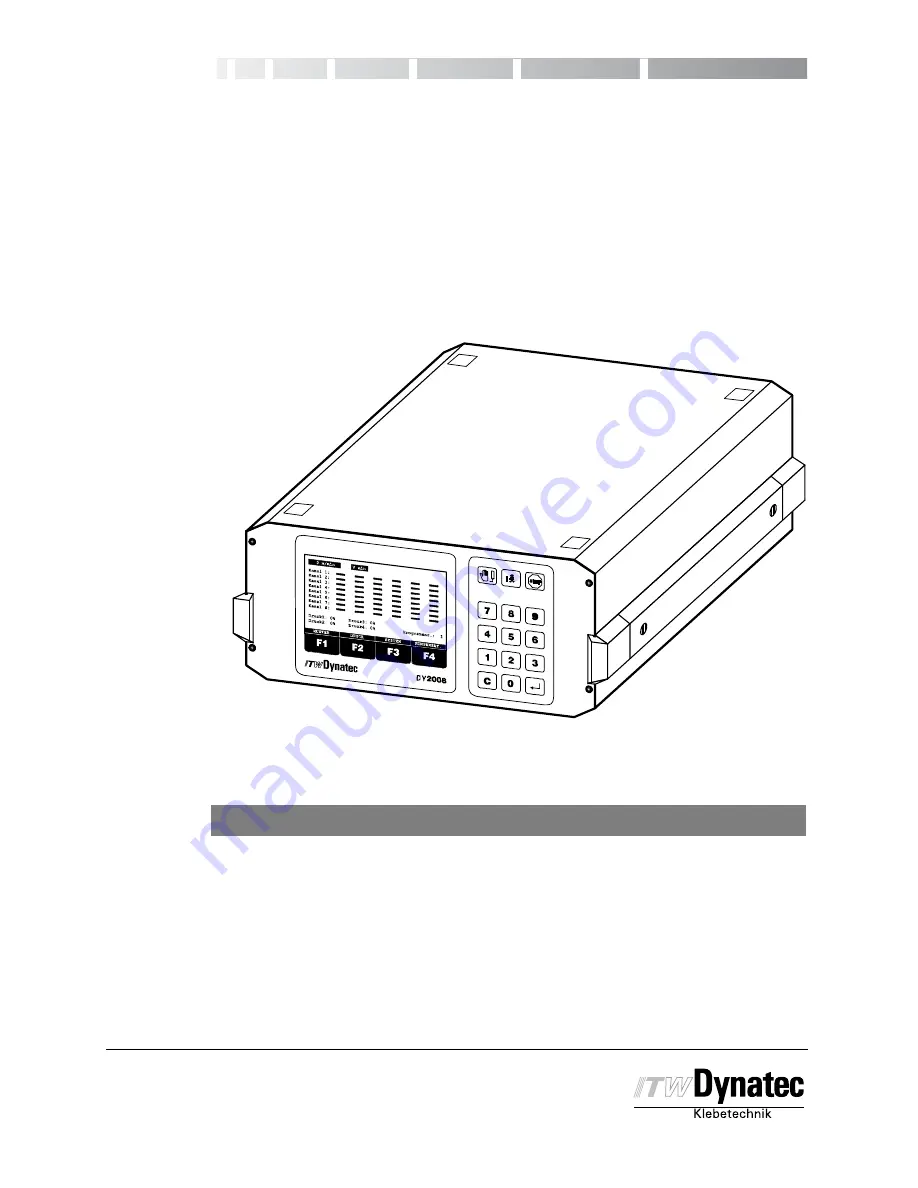
DY 2008
Pattern Controller
CONTROLLER
Operating Manual
2008 D.BOO 11/02
ITW Dynatec
An Illinois Tool Works Company
31 Volunteer Drive
Hendersonville, TN 37075 USA
Tel1 615 824 3634
FAX +1 615 264 5222
dynatec@itwdynatec.com
www.itwdynatec.com
ITW Dynatec K.K.
Daiwashinagawa Bldg., 7-15 Konan, 3-Chome
Minata-Ku, Tokyo 108 Japan
Telephone 81 3 3450 5901
FAX 81 3 3450 8405
info@itwdynatec.co.jp
ITW Dynatec
Industriestraße 28
40822 Mettmann, Germany
Tel.: +49 (0)2104 915-0
FAX: +49 (0)2104 / 915 111
info@itwdynatec.de
Manual #50-14
Rev.11/15
For an online copy of this manual, go to www.itwdynatec.com/manuals.htm
Summary of Contents for DY 2008
Page 2: ......
Page 3: ......
Page 4: ......
Page 91: ...ITW Dynatec c 2003 Appendix B pg 9 DY2008 Controller Manual 50 14 Revised 1 09 ...