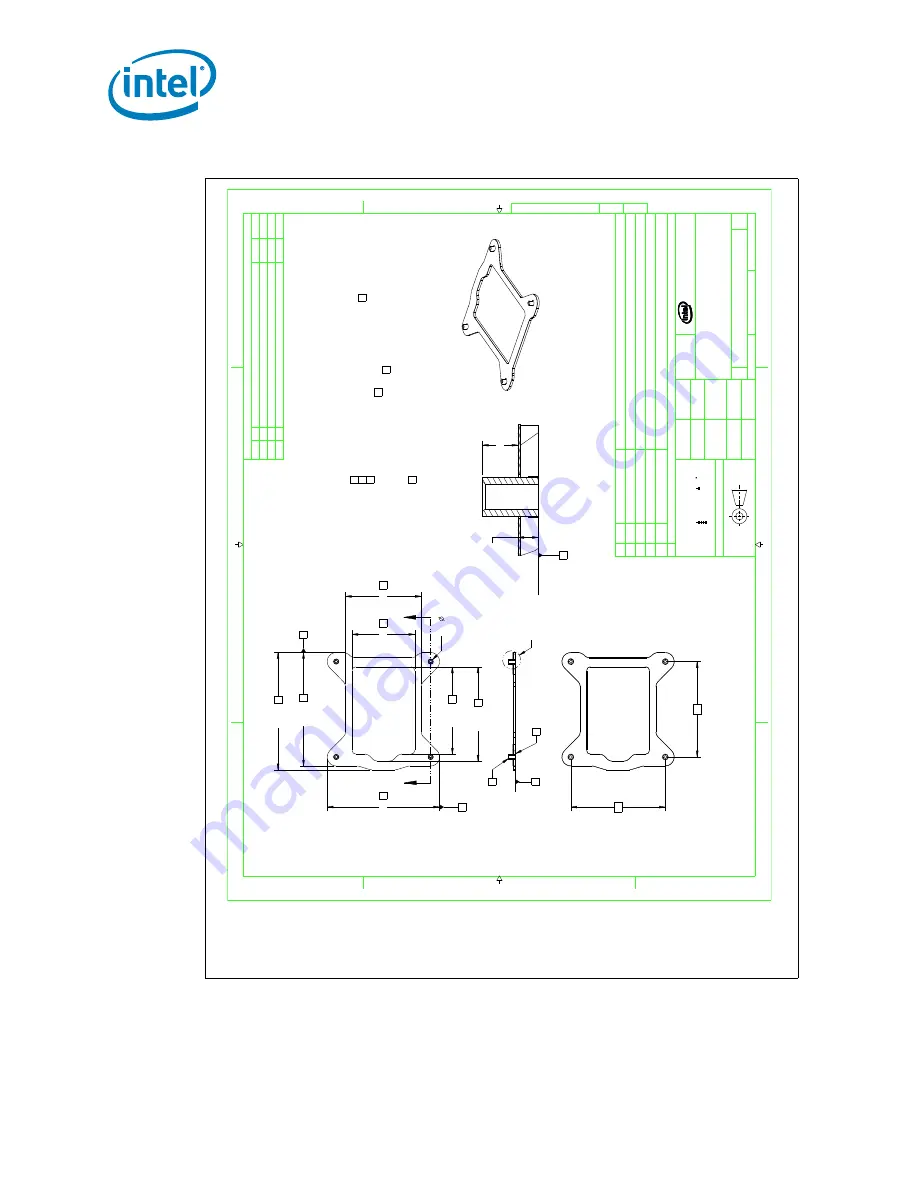
Mechanical Drawings
90
Figure B-11. Heatsink Backplate Assembly
A
4
B
3
C
D
43
21
A
2
C
1
D
A
A
E49060-001
1
C
DWG. NO
SHT.
REV
THIS DRAWING CONTAINS INTEL CORPORATION CONFIDENTIAL INFORMATION. IT IS DISCLOSED IN CONFIDENCE AND ITS CONTENTS MAY NOT BE DISCLOSED, REPRODUCED, DISPLAYED OR MODIFIED, WITHOUT THE PRIOR WRITTEN CONSENT OF INTEL CORPORATION.
SHEET
1 OF
1
DO NOT SCALE DRAWING
SCALE:
1:1
C
E49060-001
C
REV
DRAWING NUMBER
SIZE
ASSY, BACK PLATE, HS, FOXHOLLOW
TITLE
2200 MISSION COLLEGE BLVD. P.O. BOX 58119 SANTA CLARA, CA 95052-8119
R
EASD-SH
DEPARTMENT
SEE NOTES
SEE NOTES
FINISH
MATERIAL
-
-
DATE
APPROVED BY
-
-
-
-
DATE
CHECKED BY
04/10/08
JUN LU
DATE
DRAWN BY
04/10/08
JUN LU
DATE
DESIGNED BY
UNLESS OTHERWISE SPECIFIED INTERPRET DIMENSIONS AND TOLERANCES IN ACCORDANCE WITH ASME Y14.5M-1994 DIMENSIONS ARE IN MILLIMETERS TOLERANCES: .X
0.5 Angles
0.5
.XX
0.25
.XXX
0.025
THIRD ANGLE PROJECTION
PARTS LIST
DESCRIPTION
PART NUMBER
ITEM NO
QTY
-
E49060-001
TOP
HS BACKPLATE
E49062-001
1
1
HS BACKPLATE INSULATOR
E49058-001
2
1
HS BACKPLATE STANDOFF
E49063-001
3
4
REVISION HISTORY
ZONE
REV
DESCRIPTION
DATE
APPR
1
A
INITIAL RELEASE
04/10/08
-
2
B
UPDATE
07/20/08
3
C
ADDED PLATING CORROSION REQUIREMENT
01/21/09
()
6
89.25
()
6
92.25
()
6
89.25
()
6
49.75
()
6
68.55
()
6
74.05
()
6
60.25
75
4 X (
)
3.52
()
AFTER INSULATOR
APPLICATION
2.03
4 X
3.8
75
C
B
A
A
NOTES: 1. THIS DRAWING TO BE USED IN CONJUNCTION WITH SUPPLIED 3D DATABASE. ALL DIMENSIONS AND TOLERENCES ON THIS DRAWING TAKE PRECEDENCE OVER SUPPLIED DATABASE 2. PRIMARY DIMENSIONS STATED IN MILLINETERS. [BRACKETED] DIMESNIONS STATED IN INCHS.
3
CRITICAL TO FUNCTION DIMENSION
4
INSTALL ALL STUDS FLUSH TO THIS S0.00 / -0.25
3
5
HEAT SINK ATTACH STUDS:
-PUSHOUT FORCE > 100LBF
3
-TORQUE TO FAILURE > 20 IN-LBF
3
-FAILURE MODES: STUDS MUST NOT SHEAR, DEFORM, STRIP, CRACK, OR TORQUE OUT BELOW THIS TORQUE LIMIT. -LIMITS BASED ON A 3 SIGMA DISTRIBUTION
6
CRITICAL TO FUNCTION: NO METAL OF THE FLAT PLATE CAN BE EXPOSED
7. CLEAN AND DEGREASE BACKPLATE ASSEMBLY BEFORE ATTACHING INSULATION 8. AFTER APPLICATION THE INSULATOR MUST BE FREE OF BUBBLES, POCKETS, GREASED, AND ANY OTHER DEFORMATIONS. 9. PLATING CORROSION REQUIREMENTS: 48 HRS 85 C / 85% HUMIDITY WITH NO VISIBLE CORROSION
4
SECTION
A-A
SEE DETAIL
A
5
DETAIL
A
SCALE
8:1
Summary of Contents for BX80605X3440 - Quad Core Xeon X3440
Page 10: ...Introduction 12 Thermal Mechanical Specifications and Design Guidelines...
Page 26: ...LGA1156 Socket 28 Thermal Mechanical Specifications and Design Guidelines...
Page 78: ...Component Suppliers 78...
Page 80: ...Mechanical Drawings 80 Figure B 1 Socket Heatsink ILM Keepout Zone Primary Side for 1U Top...
Page 87: ...87 Mechanical Drawings Figure B 8 Heatsink Compression Spring...
Page 88: ...Mechanical Drawings 88 Figure B 9 Heatsink Load Cup...
Page 89: ...89 Mechanical Drawings Figure B 10 Heatsink Retaining Ring...
Page 91: ...91 Mechanical Drawings Figure B 12 Heatsink Backplate...
Page 92: ...Mechanical Drawings 92 Figure B 13 Heatsink Backplate Insulator...
Page 102: ...Socket Mechanical Drawings 104 Thermal Mechanical Specifications and Design Guidelines...
Page 106: ...Package Mechanical Drawings 108 Thermal Mechanical Specifications and Design Guidelines...