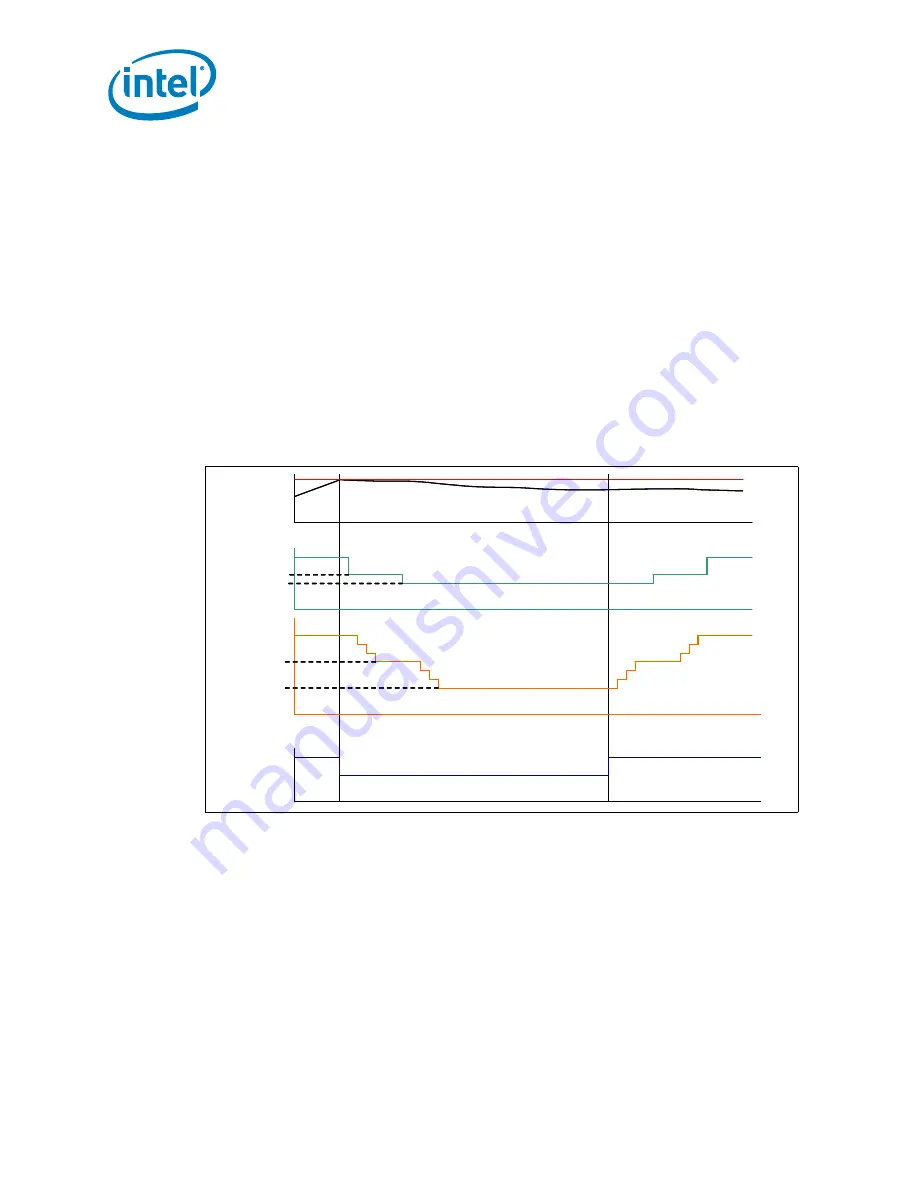
Thermal Specifications
46
Document Number: 424077 Revision: 2.0Thermal/Mechanical
Specifications and Design Guidelines
take place. This sequence of temperature checking and Frequency/VID reduction will
continue until either the minimum frequency has been reached or the processor
temperature has dropped below the TCC activation point.
If the processor temperature remains above the TCC activation point even after the
minimum frequency has been reached, then clock modulation (described below) at that
minimum frequency will be initiated.
There is no end user software or hardware mechanism to initiate this automated TCC
activation behavior.
A small amount of hysteresis has been included to prevent rapid active/inactive
transitions of the TCC when the processor temperature is near the TCC activation
temperature. Once the temperature has dropped below the trip temperature, and the
hysteresis timer has expired, the operating frequency and voltage transition back to
the normal system operating point using the intermediate VID/frequency points.
Transition of the VID code will occur first, to insure proper operation as the frequency is
increased. Refer to
for an illustration of this ordering.
6.2.2.2
Clock Modulation
Clock modulation is a second method of thermal control available to the processor.
Clock modulation is performed by rapidly turning the clocks off and on at a duty cycle
that should reduce power dissipation by about 50% (typically a 30–50% duty cycle).
Clocks often will not be off for more than 32 microseconds when the TCC is active.
Cycle times are independent of processor frequency. The duty cycle for the TCC, when
activated by the Intel
®
Thermal Monitor, is factory configured and cannot be modified.
It is possible for software to initiate clock modulation with configurable duty cycles.
Figure 6-4. Frequency and Voltage Ordering
Temperature
f
MAX
f
1
f
2
VIDf
MAX
VID
Frequency
VIDf
2
VIDf
1
PROCHOT#
Temperature
f
MAX
f
1
f
2
VIDf
MAX
VID
Frequency
VIDf
2
VIDf
1
PROCHOT#
Summary of Contents for BX80605X3440 - Quad Core Xeon X3440
Page 10: ...Introduction 12 Thermal Mechanical Specifications and Design Guidelines...
Page 26: ...LGA1156 Socket 28 Thermal Mechanical Specifications and Design Guidelines...
Page 78: ...Component Suppliers 78...
Page 80: ...Mechanical Drawings 80 Figure B 1 Socket Heatsink ILM Keepout Zone Primary Side for 1U Top...
Page 87: ...87 Mechanical Drawings Figure B 8 Heatsink Compression Spring...
Page 88: ...Mechanical Drawings 88 Figure B 9 Heatsink Load Cup...
Page 89: ...89 Mechanical Drawings Figure B 10 Heatsink Retaining Ring...
Page 91: ...91 Mechanical Drawings Figure B 12 Heatsink Backplate...
Page 92: ...Mechanical Drawings 92 Figure B 13 Heatsink Backplate Insulator...
Page 102: ...Socket Mechanical Drawings 104 Thermal Mechanical Specifications and Design Guidelines...
Page 106: ...Package Mechanical Drawings 108 Thermal Mechanical Specifications and Design Guidelines...