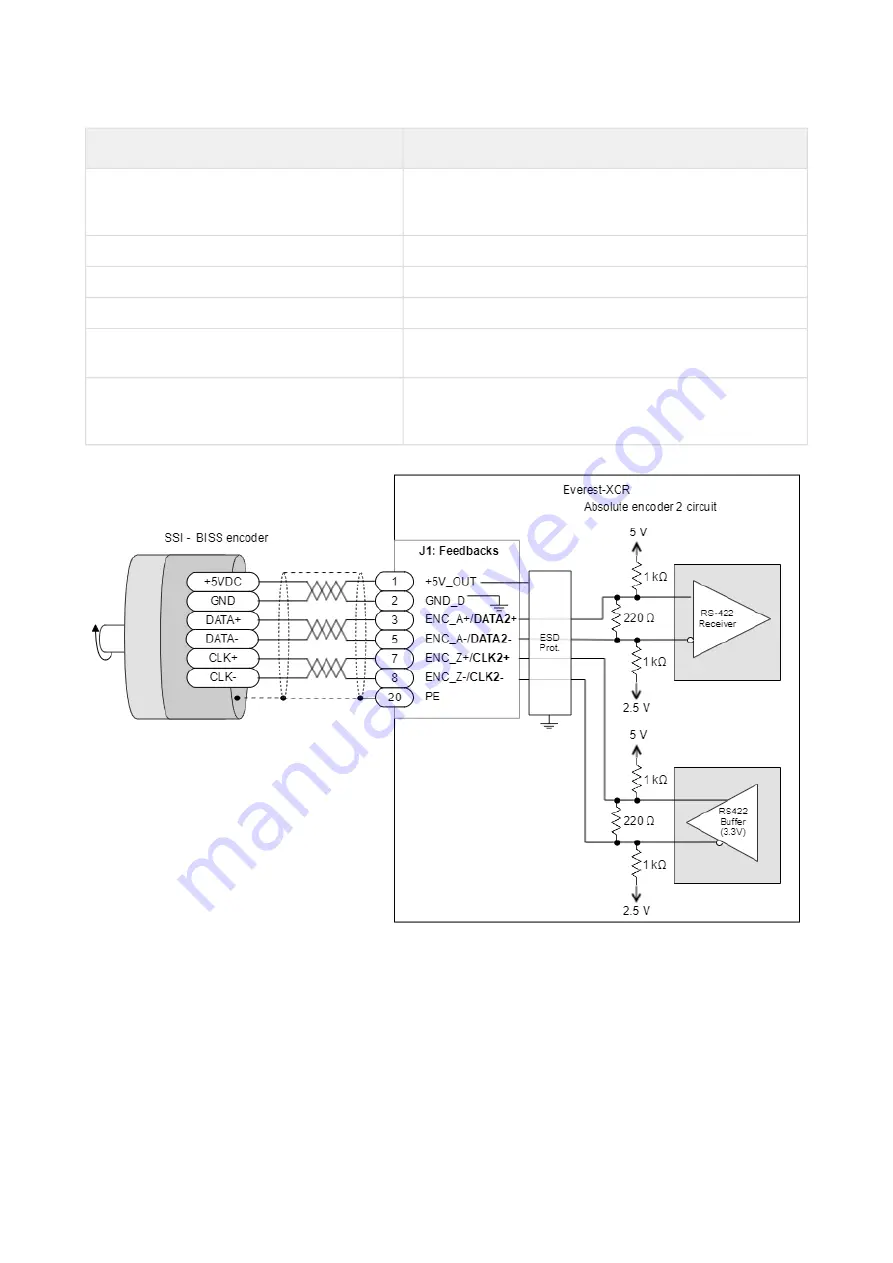
Everest XCR - Product Manual |
Wiring and Connections
INGENIA | 08/04/2019
49
Specification
Value
ESD capability
IEC 61000-4-2 (ESD) ± 30 kV (air), ± 30 kV (contact)
IEC 61000-4-5; tp = 8/20
μ
s 12 A, 200 W
Maximum operating voltage range
-0.5 ~ 5.5 V
Operating frequency
100 kHz to 10 MHz (user configurable)
Receiver hysteresis
min 50 mV typ 80 mV (DATA+ - DATA-)
Termination
220
Ω
differential on data line. Fail safe basing resistors of 1
k
Ω
, see drawings.
Fail safe bias resistors
ENC_x+ (positive input) 1 k
Ω
to 5 V
ENC_x- (negative input) 1 k
Ω
to 2.5 V (equivalent)
The next figure shows how to connect
a secondary SSI or BISS-C absolute encoder
to
the Everest XCR
servo drive
.
9.5.4.
Incremental Encoder
Everest XCR can use single-ended or differential digital incremental encoder inputs (also known as quadrature
incremental encoders) for velocity and/or position control, as well as for commutation purposes. The encoder
provides incremental position feedback that can be extrapolated into precise velocity or position information.
Using high resolution encoders allows Everest XCR to perform sinusoidal commutation. Channel A and channel B
signals should have a phase shift of 90 degrees, indicating the rotation direction. The drive has an optional index
signal input. Index signal (Z) is a single pulse per revolution signal that can be used to know absolute positions and
for homing operations
. The following table illustrates the
digital
encoder inputs main features.