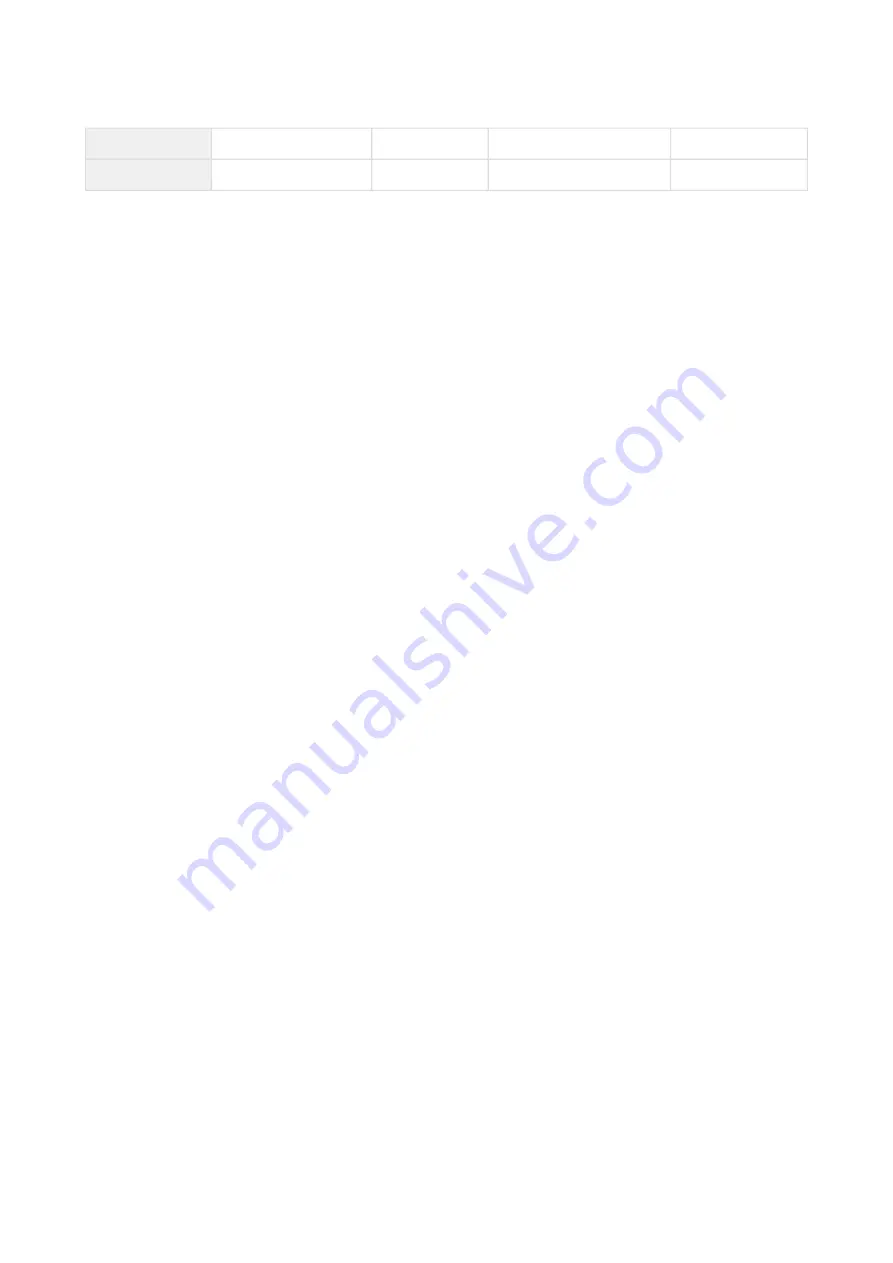
Everest XCR - Product Manual |
Wiring and Connections
INGENIA | 08/04/2019
39
18 A
0.8 mm²
18 AWG
1.3 mm²
16 AWG
12 A
0.5 mm²
20 AWG
0.8 mm²
18 AWG
For best electromagnetic compatibility (EMC) the power supply cable inductance should be minimized. Wiring
recommendations:
•
Minimize area between positive and negative supply voltages. The best practice is by
twisting
them as can
be seen in the wiring diagrams.
• Increase cross section of the cables (Max recommended is 4 mm² CSA, 2.3 mm diameter).
•
Reduce distance between power supply and drive.
Soldering Power Pins
The power wires of the Everest-XCR should be soldered appropriately to ensure a reliable and low resistance
connection. The solder holes are 2.6 mm in diameter. ensure the cable diameter does not exceed this.
Please follow this steps:
1. Cut and peel the power cables in advance with appropriate length. The peeled length can be around 3 mm.
Do not cut them after soldering as it will cause permanent tensions.
2. Pre-tin the stranded wires by applying solder with flux to the wire using a heated soldering-iron tip. This can
be done with a solder bath method. Ensure a minimum solder time of 2 ~ 3 seconds.
a.
Solder shall penetrate the inner strands of stranded wire.
b. Solder shall not obscure the wire contour at the termination end of the insulation.
c. Anti
‐
wicking tools are strongly recommended in order to protect the cable insulation.
3. Apply flux to the pads with a brush to ensure surfaces are clean and there is sufficient flux.
4. Pre-tin the solder pads of the Everest-XCR using Rohs-free solder. Take precautions with the solder balls not
to create any short. Do not fill the hole.
5. Position the wire inside the hole with the desired cable exit direction and solder them with a clean solder tip.
Additional solder may be needed.
6. Clean the flux residues with appropriate solvents like isoporpyl alcohol (IPA).
7. Do not cut the wires after soldering as it may cause permanent stress and long term reliability issues.
Further tips on best practices can be found in ESA standard
.
9.4. Safe Torque Off (STO), Brake and Motor Temperature
Safe Torque Off (STO)
The STO is a safety system that prevents motor torque in an emergency event while Everest XCR remains connected
to the power supply. When STO is activated, the power stage is disabled by hardware (no matter what control or
firmware does), and the motor shaft will slow down until it stops under its own inertia and frictional forces.
In order to activate the power stage, and therefore allow the motor operation, the two STO inputs must energized
(high level, typically 5V to 24V). If the STO inputs are not energized or the wires are not connected, the transistors of
the power stage are turned off and a STO fault is notified. This input should not be confused with a digital input
configured as enable input, because enable input is firmware controlled and does not guarantee intrinsic safety as
it can be reconfigured by a user.
In order to ensure redundancy and safety, the Everest XCR includes 2 separate STO inputs that must be activated or
deactivated simultaneously (maximum 1.4 s mismatch). A difference of state between STO1 and STO2 inputs will be
interpreted as an abnormal situation, after 1.4 s the drive will be latched in fault state.
A power supply reset is
necessary to remove this STO abnormal error.