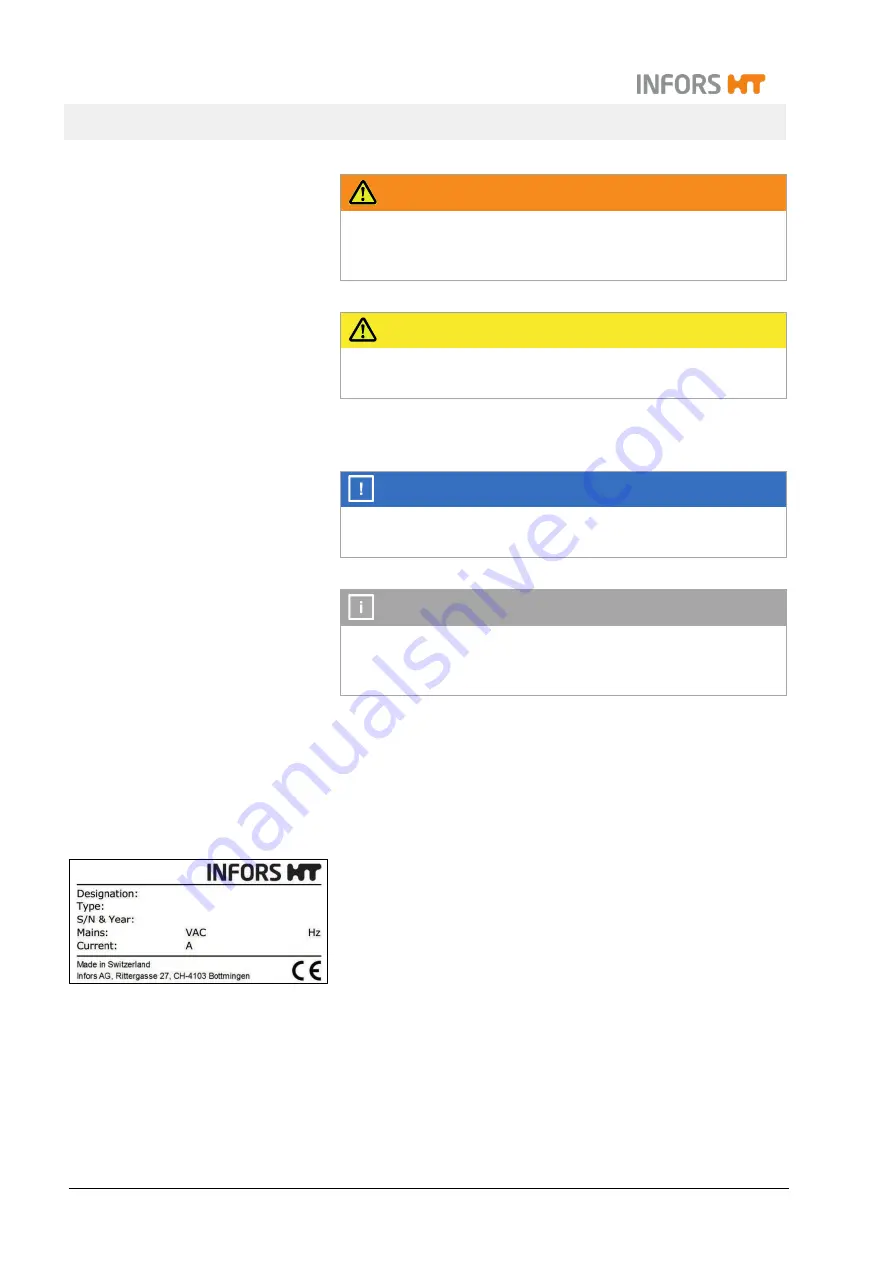
Labfors 5 – Version for Microorganisms
General Information
Page
10
of
205
22 January 2019
WARNING
The signal word “WARNING” indicates a potentially dangerous
situation that may result in severe or even fatal injuries if not
avoided.
CAUTION
The signal word “CAUTION” indicates a potentially dangerous
situation that may result in minor injuries if not avoided.
1.2.2 Other Notices
ATTENTION
The word “ATTENTION” on a blue bar indicates a situation that
may result in significant damage to property if not avoided.
INFORMATION
Texts located below a grey bar bearing the notice “INFOR-
MATION” provide useful tips and recommendations for ensuring
efficient, fault-free operation of the equipment.
1.3 Equipment Identification (Standard Identification Plate)
The identification plate is designed to allow clear identification of
the equipment. It contains the following information:
Manufacturer name
Designation
=
Category of equipment
Type
=
Equipment type (name)
S/N
=
Serial number
Year
=
Year of manufacture
Mains
=
Nominal voltage and frequency
Current
=
Current consumption
Manufacturer address
CE marking
Summary of Contents for Labfors 5
Page 208: ......