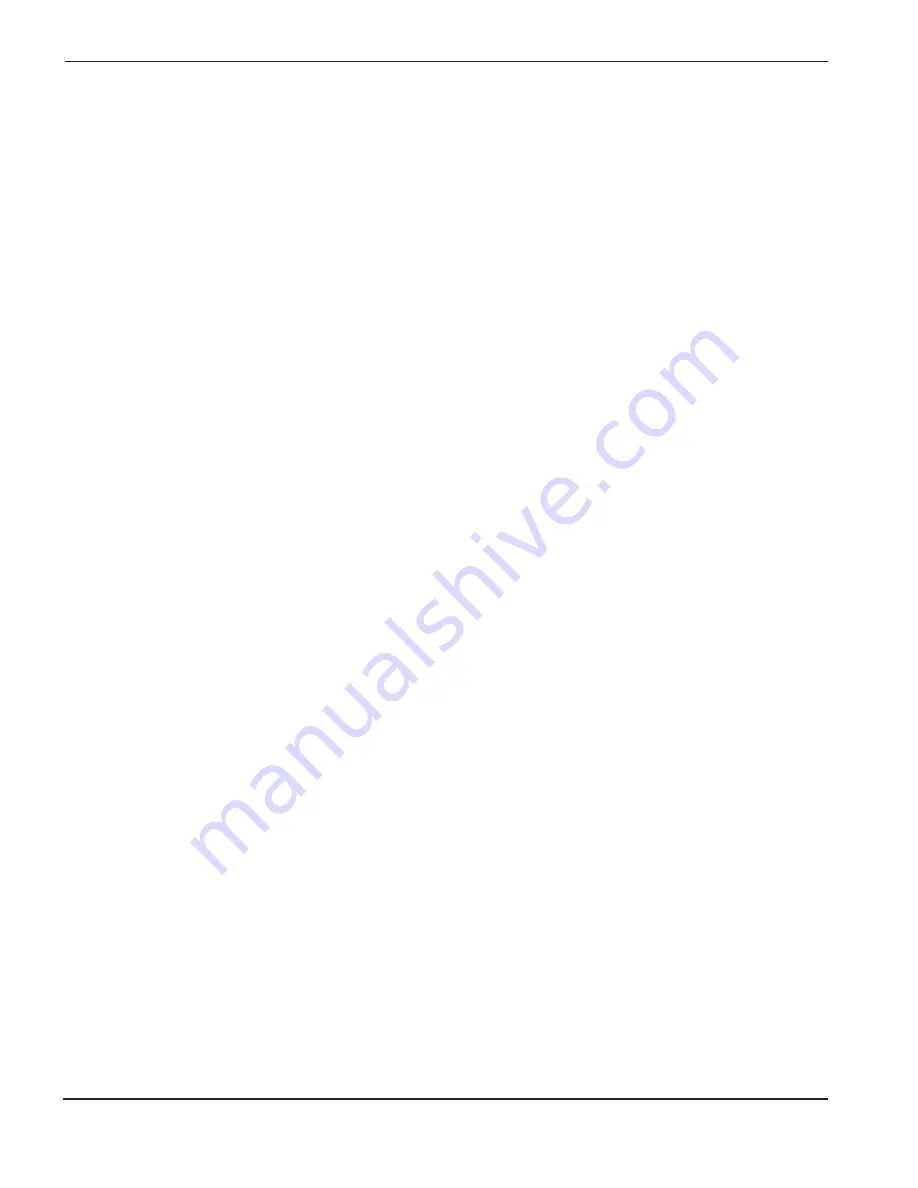
SETUP
3-18
CommandTHC for X-Y Table
Instruction Manual
11
CommandTHC serial protocol
Commands can be sent over a serial link to control the function of the torch height control. The interface is 4 wire
RS422 on the MACHINE INTERFACE CABLE (pins (1) RX–, (20) RX+, (2) TX–, (21) TX+).
The serial frame runs at:
Old protocol (041507 control PCB) – 9600 baud, 8 data bits, 2 stop bits, and even parity
New protocol (041706 control PCB) – 19200 baud, 8 data bits, 1 stop bit, and no parity
All bytes in a serial message are ASCII characters. A message consists of a start of message character (>, 0x3E),
2 byte message ID (all message ID’s should be capitalized), variable length data, 2 byte checksum, and end of message
character (<, 0x3C). For example to put the THC into remote mode >RM1D0<. ‘RM’ is the message ID, ‘1’ is the data
field, and 0xD0 is the checksum (2 hex digits sent as 2 ASCII characters). The response to an accepted command is
(^, 0x5E) and the response to an invalid command is (#, 0x23).
Some of the commands can be queried by using (?, 0x3F) as the data. For example to query the actual arc voltage
>AV?D6<. The response to this query would be >AV100058<, which represents an actual arc voltage of 100.0 volts
with a checksum of 0x58.
Errors can be retrieved over the serial link. There is a discrete output on the machine interface cable (THC Error pins
14,33) which indicates an error has occurred. Using the command >CL8F< errors can be cleared and retrieved.
A typical response might be >ERR-Motor Current Fault46< or if there is no error (^, 0x5E) is returned.
Command listing:
Command
ID
Data
Query
Notes
Pierce Delay
PD
0 – 9000 (0 to 9.000 seconds)
yes
Delay before motion output
Pierce Height Factor
PH
50 – 300 (50% to 300%)
yes
Used to set pierce height
Preflow During IHS
PF
0,1 (0 = off, 1 = on)
yes
Improves cycle time
IHS Stall Current
SC
1 – 10 (1 = least force)
yes
Used to set stall force
IHS Speed
IV
1 – 10 (1= slowest)
yes
Used to set IHS speed
IHS Test
IH
0,1 (0 = run, 1 = test)
no
Perform IHS test
Nozzle Contact Active
NC
0,1 (0 = off, 1 = on)
yes
Enable nozzle contact IHS
Machine Acceleration
MA
0 – 9000 (0 to 9.000 seconds)
yes
Delay voltage control
Maintenance Mode
MT
No data
no
Maintenance mode
Auto Kerf
AK
0,1 (0 = off, 1 = on)
yes
Disable voltage control in kerf
Actual Arc Voltage
AV
? (query only)
yes
Returned value is 1/10 volts
Automatic Voltage Control AA
0,1 (0 = manual, 1 = auto)
yes
Voltage control or manual
Retract
RE
0,1 (0 = full, 1 = partial)
yes
Full or partial retract
Retract Distance
RH
0 – 8000 (0 to 8.000 inches)
yes
Must be in partial retract
Remote Mode
RM
0,1 (0 = off, 1 = on)
yes
Must be ON to use serial link
IO Rev
RI
? (query only)
yes
IO revision
RT Rev
RR
? (query only)
yes
Real Time revision
Homing Speed
HS
1 – 10 (1 = slowest)
yes
Home speed
Unit Conversion
UN
0,1 (0 = inches, 1 = metric)
yes
Units
Lifter Test
LT
No data
no
Perform lifter test
Cut Height
CH
0 – 1000 (0 to 1.000 inches)
yes
Used to set cut height
Arc Voltage Setpoint
VS
500 – 3000 (50.0 to 300.0 volts) yes
Used to set voltage control
Step Up
S+
No data
no
Move up fixed increment
Step Down
S–
No data
no
Move down fixed increment
Jog Up
J+
No data
no
Continuous movement up
Jog Down
J–
No data
no
Continuous movement down
Clear Error
CL
No data
no
Clear error, send error string
Flush Buffers
FL
No data
no
Reset RX and TX buffers
Error code
EC
? (query only)
yes
Send error code number