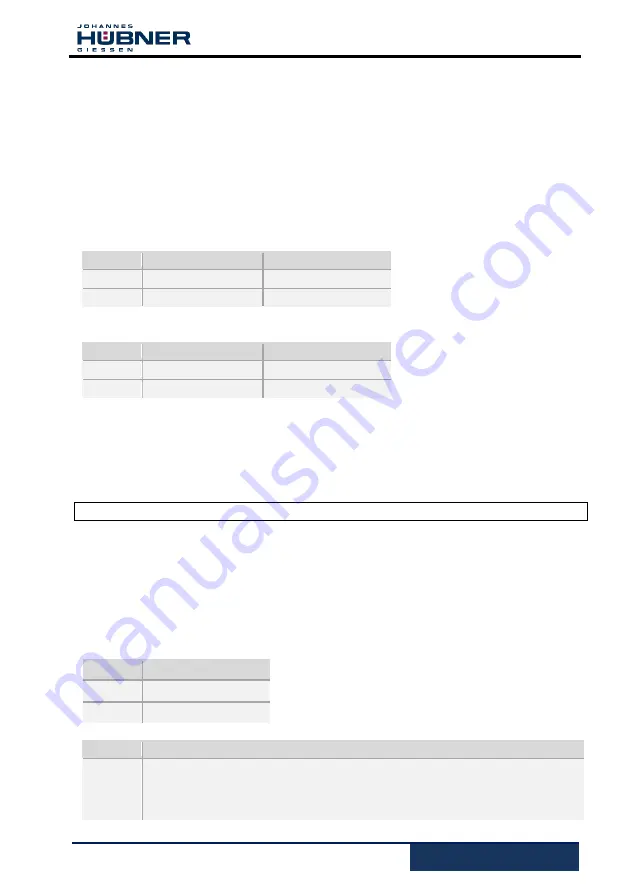
Absolute Encoder AMP(H) 41
AMP(H)41_MANUAL-en_R11 - 2019-03-28
41
–
Looking at the flange connection, turn the shaft clockwise:
negative speed output
If the measured speed exceeds the display range of
–32768…+32767, this results in an overflow, which is reported in the cam register via bit 2
0
. At
the time of the overflow the speed stops at the resp/- maximum value, until the speed is
once again in the display range. In this case the message in the cam register is also cleared.
The speed is specified in
increments
per
Integration time Safe
.
6.6.2.1.4
Multi-Turn / Single-Turn
Multi-Turn, Integer16
Byte
X+6
X+7
Bit
15 – 8
7 – 0
Data
2
15
– 2
8
2
7
– 2
0
Single-Turn, Integer16
Byte
X+8
X+9
Bit
15 – 8
7 – 0
Data
2
15
– 2
8
2
7
– 2
0
As only 16-bit registers have previously been possible on the control side, the position value
must be calculated first. The number of revolutions is noted in the
Multi-Turn
register, and
the current Single-Turn position is noted in steps in the
Single-Turn
register. Together with
the measuring system resolution, max. number of steps per revolution according to type plate,
the actual position can then be calculated
Position in steps = (steps per revolution * number of revolutions) + Single-Turn position
Steps per revolution: 8192
≙
13 Bit
Number of revolution: 0…32767
≙
15 Bit
The output position does not have a preceding sign.
6.6.2.1.5
Safe-Status
Unsigned8
Byte
X+10
Bit
7 – 0
Data
2
7
– 2
0
Bit
Description
2
0
iPar_OK: New iParameter values have been assigned to the F-Device.
The bit is set when a preset request has been successfully completed via the F-
Host (iPar_EN bit), see chapter 10 “Preset Adjustment Function“ on page
80.
Summary of Contents for AMP 41
Page 96: ...96 AMP H 41_MANUAL en_R11 2019 03 28 Absolute Encoder AMP H 41 16 3 T V certificate...
Page 97: ...Absolute Encoder AMP H 41 AMP H 41_MANUAL en_R11 2019 03 28 97 16 4 PROFIBUS DP certificate...
Page 98: ...98 AMP H 41_MANUAL en_R11 2019 03 28 Absolute Encoder AMP H 41 16 5 PROFIsafe certificate...