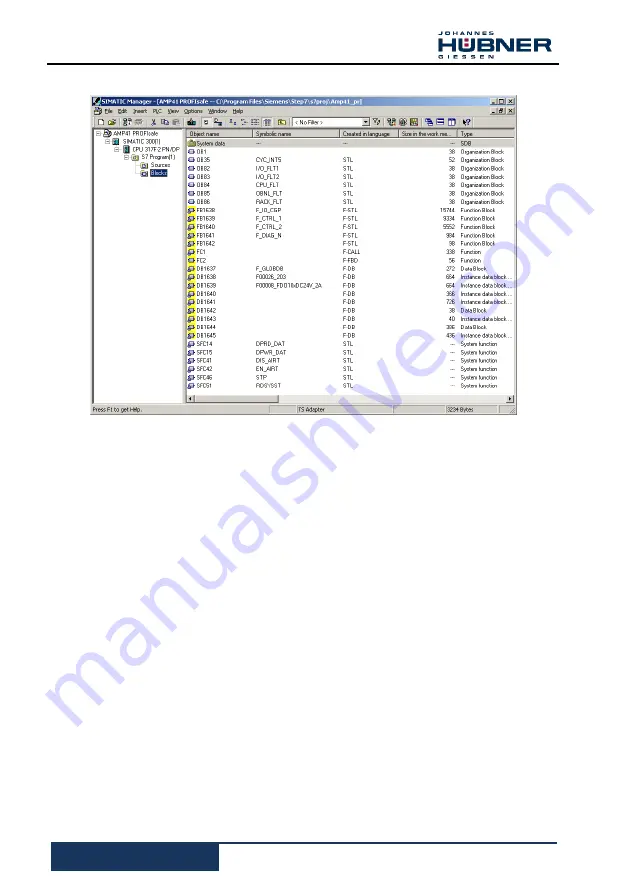
74
AMP(H)41_MANUAL-en_R11 - 2019-03-28
Absolute Encoder AMP(H) 41
All necessary blocks are now displayed in the project window:
8.6
Loading the safety program
When the safety program has been generated, it can be loaded into the F-CPU. It is advisable
to transfer the complete safety program to the F-CPU in STOP operating status. This
guarantees that a consistent safety program is loaded. The program is loaded with the menu
Options
Edit safety program
Download
switch.
8.7
Testing the safety program
After generating the safety program, a complete functional test must be carried out according
to the automation task.
After modifications to an already completely function-tested safety program, it is sufficient to
test the modifications.
9
Access to the safety-oriented data channel
The safety-oriented data channel in the
JHG-PROFIsafe
module is accessed via the process
image, as with a standard periphery. However, direct access is not permitted. The safety-
oriented data channel of the measuring system may only be accessed from the generated F-
Runtime Group.
The actual communication between F-CPU (process image) and measuring system for
updating the process image occurs concealed in the background, by means of the PROFIsafe
protocol.
The measuring system uses a larger area in the process image in the
JHG-PROFIsafe
module, due to the PROFIsafe protocol, than would be necessary for the measuring system
function. The
F-Parameter-block
contained in the process image is not included in the user
data. When accessing the process image in the safety program, only access to the pure user
data is permitted!
Summary of Contents for AMP 41
Page 96: ...96 AMP H 41_MANUAL en_R11 2019 03 28 Absolute Encoder AMP H 41 16 3 T V certificate...
Page 97: ...Absolute Encoder AMP H 41 AMP H 41_MANUAL en_R11 2019 03 28 97 16 4 PROFIBUS DP certificate...
Page 98: ...98 AMP H 41_MANUAL en_R11 2019 03 28 Absolute Encoder AMP H 41 16 5 PROFIsafe certificate...