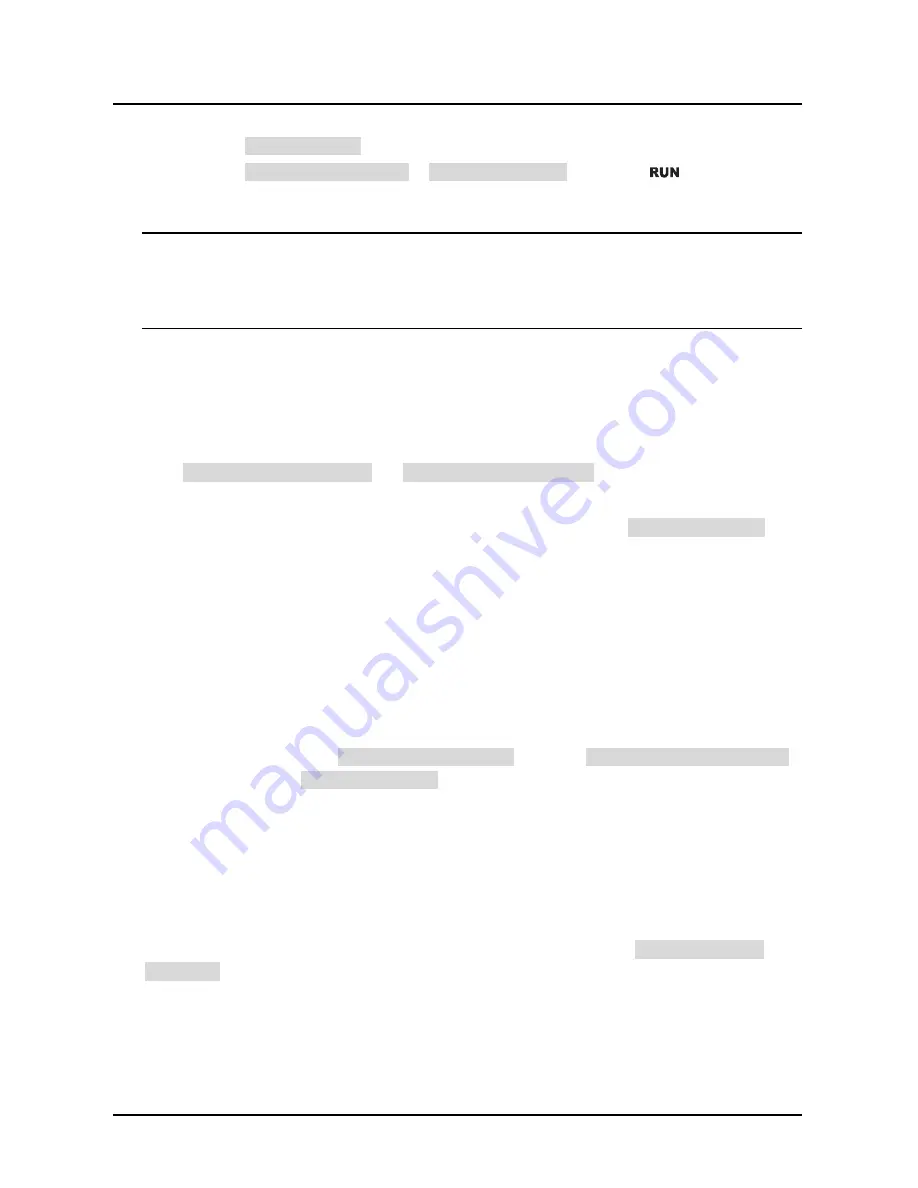
Chapter 7 Elevator application guidance
Shenzhen Hpmont Technology Co., Ltd.
―
70
―
HD3L Series Controller User Manual
7.1.3
Motor Auto-tuning
1. Set F00.05 as 0 (keypad control).
2. Set F07.06 as 1 (stationary auto-tuning) or 2 (rotary auto-tuning), then press
key to start
parameter auto-tuning. The motor will rotate at rotary auto-tuning, while it will not rotate at stationary
auto-tuning.
Note:
1. The crane car is needed for the rotary auto-tuning but not for the stationary auto-tuning.
2. When auto-tuning, it needs open the run contactor; if at rotary auto-tuning, it needs open the brake
contactor manually too.
7.1.4
Inspection Running
Preparation before Inspection Running
1. After motor parameter auto-tuning, motor output U/V/W connections and encoder connection are
not changed.
2. Set F03.06 (inspection Acc speed) and F03.07 (inspection Dec speed).
Inspection Running
1. If the actual running direction of motor is not the command direction, set F00.08 (run direction) = 1.
2. Make sure that the motor can run normally.
3. Make sure the motor can run normally and the signals of the brake and power circuit etc. can act
normally, then it will do high speed running.
7.1.5
High Speed Running
1. Give the floor normal run command so that the elevator can run normally. Then set Group F02 of
start & stop parameters, start stopping parameters, adjust starting & stopping brake and motor
running time sequence to make sure that the elevator does not shake at start & stop.
2. If the elevator has slight shake at running, properly adjust Group F08.
3. To adjust leveling precision, Acc / Dec curve (Group F03) can adjust terminal MS control (F00.05 = 2)
to unify level and adjust F03.13 (stop Dec jerk) to make leveling precision.
7.2
Terminal MS Run Application
The elevator controller can calculate the motor present running direction (digital) and objective speed
(digital) according to the elevator control logic and send them to HD3L. HD3L receives the objective
speed of MS form and calculate the speed curve according to the S-curve parameter setting, then
control the motor to run.
Example:
A certain elevator with rated speed of 1.750m/s uses a controller in terminal MS control
(F00.05 = 2).
The brake of elevator controller and the contactor are controlled by signal which comes from HD3L.
Receiving signal of “HD3L is running”, the brake opens; receiving “HD3L is in zero-speed running”, the
brake closes.
The inspection running is controlled by inspection MS command of elevator controller, and the
running speed is obtained by speed combination of MS terminal.