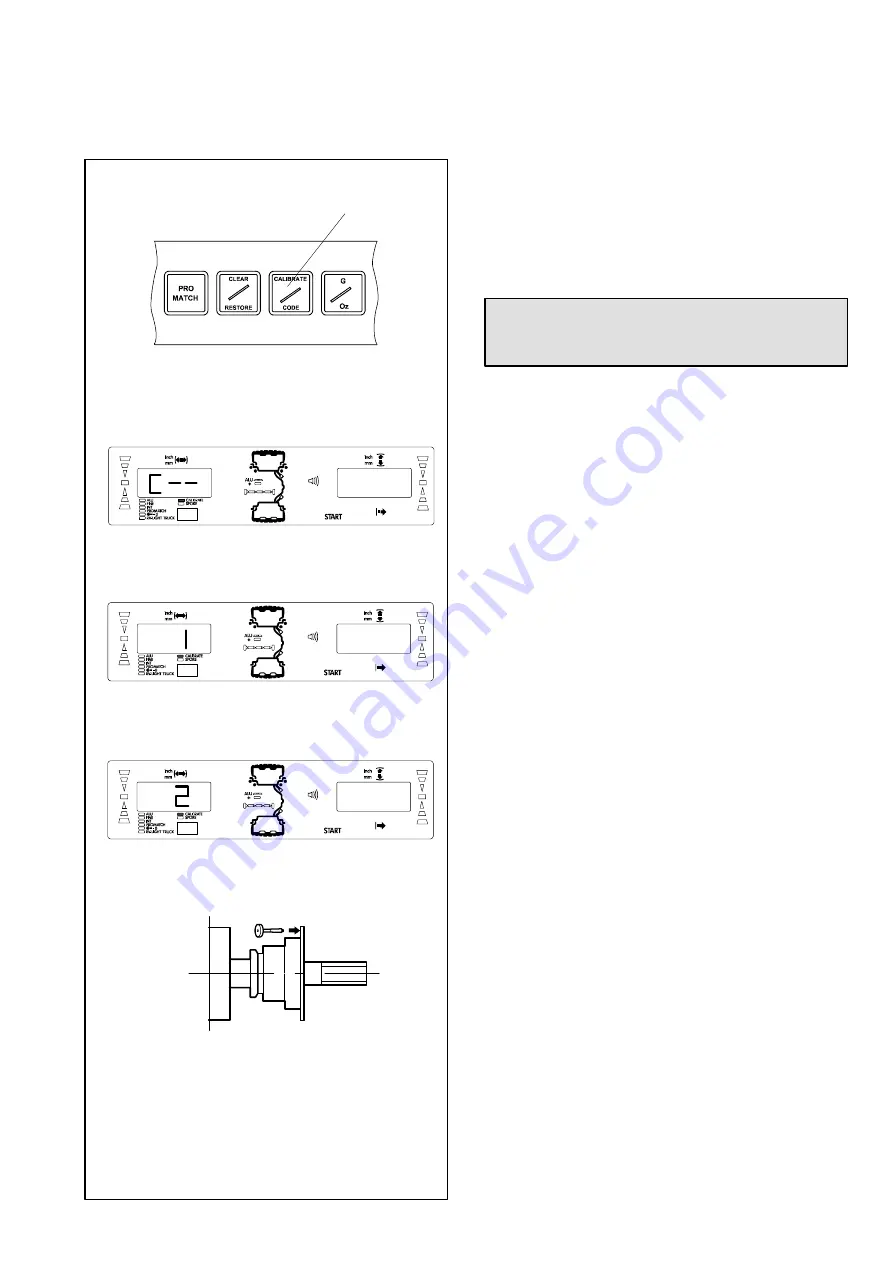
59
Operation manual geodyna 2350 - 9413 126
User calibration
135
136
137
138
139
1
.
.
13. User calibration
If several measuring runs are necessary to balance a wheel be-
cause balance weight size and position have to be changed re-
peatedly, it may be necessary to readjust the machine.
For readjustment by the operator a calibration weight is sup-
plied with the machine (ref. no. 6418 416 - kept on the rear of
the weight tray).
Important:
Readjustment must be carried out using the clamping
adapter supplied with the machine.
Readjustment
(Code C14)
D
Make sure no wheel or other clamping means is clamped
on the machine.
D
Press and hold the CODE key
(Fig. 135, pos. 1)
.
The basic reading C -- is read out
(Fig. 136)
.
D
Release the CODE key.
Reading 1. and START are read out
(Fig. 137)
.
D
Close the optional wheel guard, and press the START
key to carry out a readjustment run.
On completion of the first run reading 2. and START are read
out
(Fig. 138)
.
D
Screw the calibration weight into the threaded bore pro-
vided for this purpose in the basic body of the wheel
adapter
(Fig. 139)
.
D
Press the START key to carry out a second readjustment
run with the calibration weight fitted on the adapter (to de-
tect the correction values).
On completion of the processing operation a three-tone signal
is given and readjustment is completed. The machine is now
operative and the basic readings come back
(Fig. 135)
.
D
Remove the calibration weight from the wheel adapter
and put it back in its designated place.