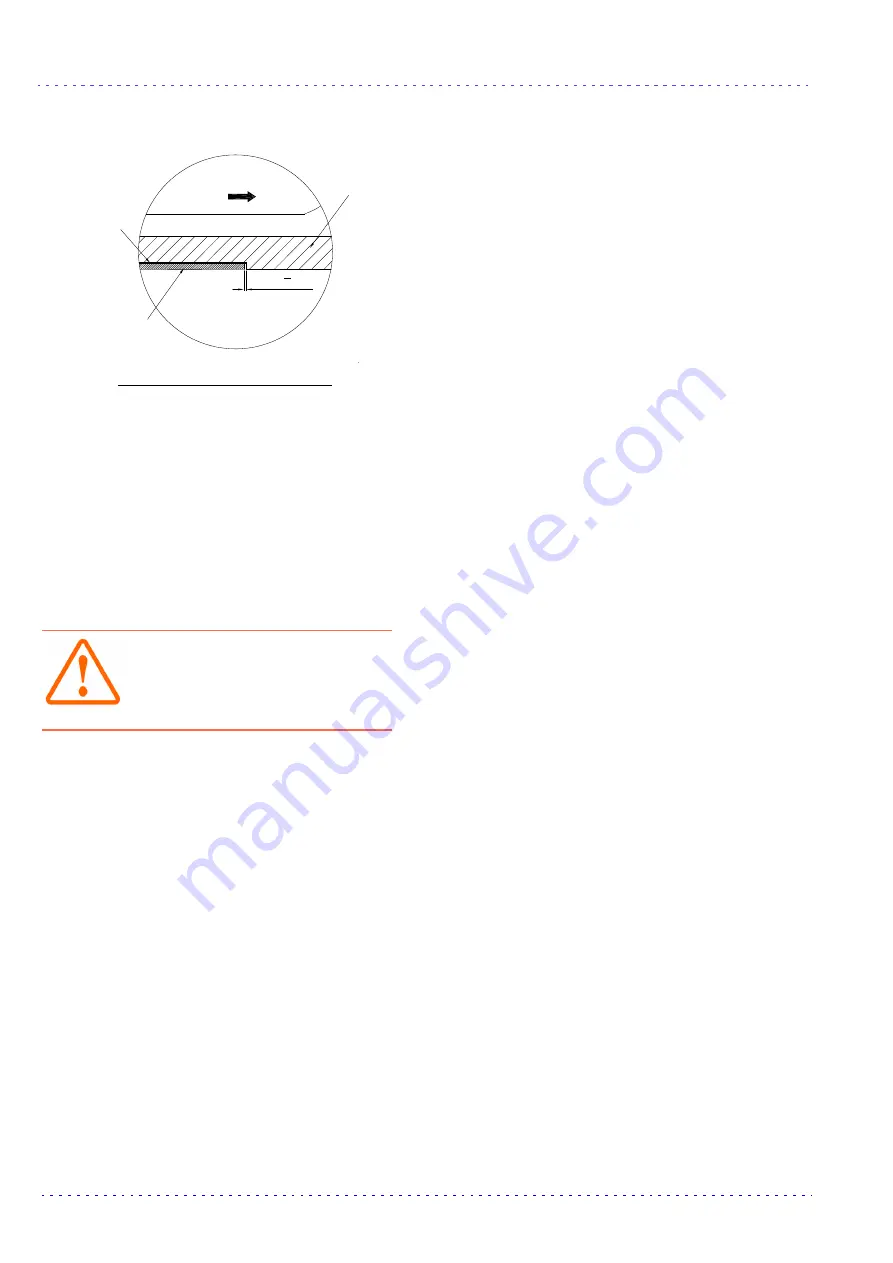
9.24
9 OVERHAUL
9.7 T
AILPIPE
A
REA
- O
VERHAUL
HJ-241 / HSRX
9.7.5 Impeller Area - Overhaul
Minor corrosion damage around the Wear Ring /
Impeller position inside the Tailpipe, such as pitting
may be repaired by welding. Grind the welded
surface flush with the original surface.
If the surface wear is more than 1mm deep, a new
Intake should be fitted.
9.7.6 Impeller Overhaul
NOTE: All welds must be passivated to prevent
corrosion.
Impellers are stainless steel type CF8M conforming
to ASTM A 743 or 316 to BS 3100. Filler metal
should have chemical analysis similar to AISI 316L
(Carbon content less than 0.03%) Post weld heat
treatment is not required. Passivation is required
after welding is completed.
INSPECTION:
1. Inspect all surfaces of the Impeller for any sign of
corrosion or erosion damage. Damaged areas
should be weld repaired and dressed back to a
smooth surface.
2. Check the Impeller leading and trailing edges for
damage. In particular the outer corners of a blade
may be bent if the Impeller has been dropped or
mishandled. Bent or dented blades may be
straightened using suitable tools. Bring the blade
back to it's original smooth profile checking
against undamaged blades.
3. Inspect the leading edges, excessively worn or
blunt leading edges may be built up by welding.
Blunt Impellers cause loss of performance and
sometimes cavitation.
4.
Check the Impeller O.D
.
BLADE LEADING EDGE REPAIR PROCEDURE:
Drawing
desired blade profile. The following information
should also be referred to:
1. Dress the edge back to a smooth curve removing
the minimum amount of metal.
2. Weld repair damaged edges if required.
3. Dress both faces of the blade taking slightly more
metal off the rear side until the leading edge is the
same thickness all along.
Refer to Drawings
82206 Impeller Blade Dressing Instructions and
Balancng Information Sht 1 - 4.
4. Blend well back into the original blade surface.
5. Both front and rear surfaces are to be a smooth
uniform curve with no sudden bumps or change
in direction.
6. Grind or file a smooth radius along the leading
edge.
Refer to Drawings
Dressing Instructions and Balancng Information
Sht 1 - 4.
IMPELLER OUTSIDE DIAMETER (O.D.) REPAIR
PROCEDURE:
1. If the Impeller OD is excessively worn it may be
built up by welding. After welding turn the
Impeller on a mandrel to the correct OD. Use
light cuts to avoid blade distortion. Dress the
faces back flush with the original surfaces.
2.
Turn the outside diameter to 239.55 - 239.40 mm
(9.431" - 9.425")
making sure that it is
concentric with the bore. (Light cuts should be
taken when turning outside diameter to avoid
deformation of the Impeller Blades).
3. File and polish the Impeller Blades.
Figure 33: Wear Ring Aft Position
C
AUTION
Avoid using excessive heat during
welding.
AFT
0.8mm(
1
32
") GAP
INTAKE
INSULATOR
WEAR RING
Summary of Contents for HJ241
Page 3: ...www hamiltonjet co nz Installation and Service Manual HJ241 Jet Unit Manual R3A31...
Page 10: ...x INTRODUCTION HJ 241 HSRX...
Page 14: ...xiv INTRODUCTION HJ 241 HSRX...
Page 15: ...Introduction and Product Description System Operation Part A Operator Information...
Page 16: ......
Page 22: ...1 6 1 INTRODUCTION PRODUCT DESCRIPTION 1 3 GENERAL ASSEMBLY DRAWINGS HJ 241 HSRX...
Page 32: ...2 10 2 SYSTEM OPERATION 2 11 HSRX REVERSE SYSTEM HJ 241 HSRX...
Page 34: ......
Page 36: ...3 2 3 DESIGN BASICS 3 2 HULL DESIGN HJ 241 HSRX Figure 9 Loads on the Hull for HJ 241 Jet Unit...
Page 54: ...3 20 3 DESIGN BASICS 3 8 DESCRIPTION OF THE DRY RUN SYSTEM OPTIONAL EXTRA HJ 241 HSRX...
Page 72: ...5 12 5 INSTALLATION 5 8 INSTALLING THE HSRX REVERSE SYSTEM HJ 241 HSRX...
Page 76: ...6 4 6 COMMISSIONING 6 5 AFTER INITIAL TRIALS AFTER ENGINE SHUT DOWN HJ 241 HSRX...
Page 77: ...Fault Finding Maintenance Overhaul Part C Servicing Information...
Page 78: ...HM 811...
Page 104: ...8 18 8 MAINTENANCE 8 8 RECOMMENDED OILS AND LUBRICANTS HJ 241 HSRX...
Page 138: ...9 34 9 OVERHAUL 9 11 HSRX HYDRAULIC REVERSE SYSTEM HJ 241 HSRX...
Page 139: ...Supplementary Technical Information Appendix...
Page 140: ......
Page 142: ...A 2 Appendix HJ 241 HSRX A 2 Loctite Application Guide...
Page 143: ...A 3 Appendix HJ 241 HSRX...
Page 144: ...A 4 Appendix HJ 241 HSRX...
Page 145: ...A 5 Appendix HJ 241 HSRX...
Page 146: ...A 6 Appendix HJ 241 HSRX...
Page 147: ...A 7 Appendix HJ 241 HSRX...
Page 159: ...A 19 Appendix HJ 241 HSRX Comments...
Page 161: ...Technical Drawings Drawings...
Page 162: ......
Page 168: ...SERVICING DRAWINGS D 6 HJ 241 HSRX HJ 241 06 000 Steering Assembly General Arrangment Sht2...
Page 170: ...SERVICING DRAWINGS D 8 HJ 241 HSRX HJ 241 07 001 Reverse Assembly Sht1...
Page 172: ...SERVICING DRAWINGS D 10 HJ 241 HSRX HJ 241 07 002 Blanking Plus No Reverse...
Page 173: ...HJ 241 HSRX SERVICING DRAWINGS D 11 HJ 241 08 001 Installation Details GRP Hull...
Page 177: ...HJ 241 HSRX SERVICING DRAWINGS D 15 HJ 241 09 001 Blanking Plugs For Screen Rake...
Page 178: ...SERVICING DRAWINGS D 16 HJ 241 HSRX HJ 241 09 002 Screen Rake Assembly...
Page 179: ...HJ 241 HSRX SERVICING DRAWINGS D 17 HJ 241 10 004 Hatch Extension...
Page 180: ...SERVICING DRAWINGS D 18 HJ 241 HSRX HJ 241 11 000 Tool Kit...
Page 181: ...HJ 241 HSRX SERVICING DRAWINGS D 19 HJ 241 12 000 Sandtrap engine Cooling...
Page 182: ...SERVICING DRAWINGS D 20 HJ 241 HSRX HJ 241 13 002 Anode Locations...
Page 183: ...HJ 241 HSRX SERVICING DRAWINGS D 21 HJ 241 30 001 General Arrangement...
Page 187: ...HJ 241 HSRX SERVICING DRAWINGS D 25 CT HSE 12 001 Hose Kits...
Page 189: ...HJ 241 HSRX SERVICING DRAWINGS D 27 CT SJK 02 005 Steering Cylinder Seastar...
Page 190: ...SERVICING DRAWINGS D 28 HJ 241 HSRX 61483 Rotary Seal...
Page 200: ...SERVICING DRAWINGS D 38 HJ 241 HSRX 85114 Earth Bonding System Recommendations and layout...
Page 201: ...Notes...