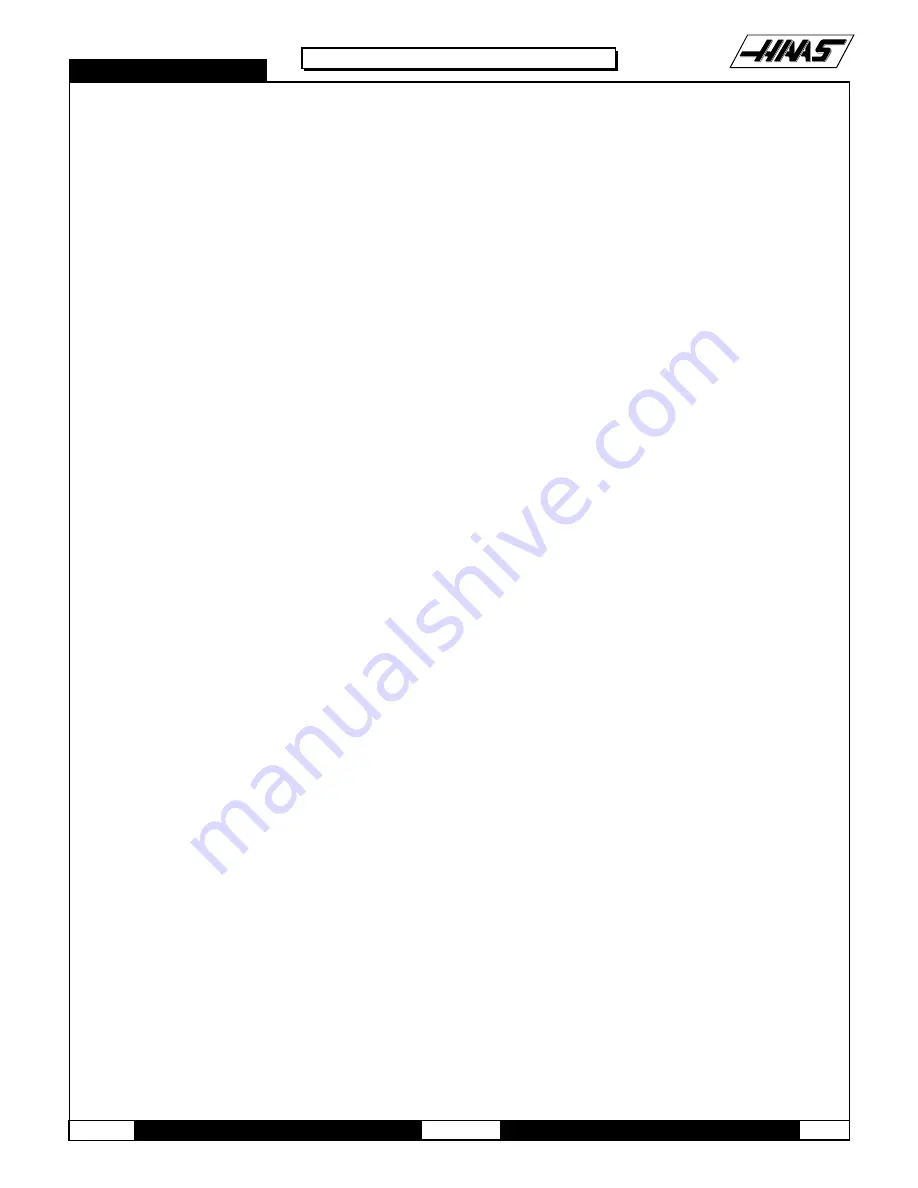
1-15-96
96-8100
153
TABLE OF CONTENTS
TECHNICAL REFERENCE
S E R V I C E M A N U A L
VF-S
ERIES
4.6 SERVO DISTRIBUTION PCB (SDIST)
The Servo Distribution PCB is used to provide the 160V DC buss for the servo drives, the low voltage AC power for the
drives, and to monitor the supply voltage for the servos.
There are three pots on this card. They are:
R2
This pot adjusts the buss voltage at which the regen load resistor is applied as a load to the power supply.
This will consume any excess power causes by the regenerative effects of decelerating the servo motors. This
should be set to turn on the load between 183 and 187V DC.
R11
This pot adjusts the fraction of the buss voltage that is sent to the Motor Interface PCB A-to-D converter. This
is a full scale 5V input and the program will interpret full scale as 200V on the buss.
R15
This pot adjusts the voltage at which an overvoltage alarm discrete is generated. This should be set to alarm
between 188 and 192V DC (about 265 AC).
The red CHARGE LED is also mounted on the SDIST PCB. It indicates that the supply capacitors still contain a charge.
The discharge resistors provide a load through this LED. It will dim and appear off when the voltage is below 20 volts.
The connectors on the SDIST PCB are:
P1
Low voltage AC power to X drive card (570)
P2
Low voltage AC power to Y drive card (580)
P3
Low voltage AC power to Z drive card (590)
P4
Low voltage AC power to A drive card (600)
P5
12V DC from power supply (860A)
P7
115V AC to fan
P8
160V DC supply to tool changer(80)
P9
Voltage monitor to A-D (980)
P10
Regen load resistor (920)
P11
Relay #1 contacts from IOPCB (110)
P12
Overvoltage status to IOPCB (970)
P13
Ground fault detect signal to IOPCB (1060)
TB1
Three phase 115V AC to SDIST
TB2
+160V DC and return to each servo drive card
There are three fuses mounted on the SDIST PCB; FU1 and FU2 protect the primaries of the fan and transformers. They are
½ amp, 240V AC, AGC type. FU3 protects the regenerative load circuit from a short circuit.
4.7 SERVO DRIVE PCBS (DRIVER)
NOTE: REFER TO THE PCB AND CABLE LOCATION SECTION FOR BOARD DIAGRAMS.
The servo drive PCBs are H drive with PWM control. There are eight states used in the H drive providing free-wheeling
current during PWM and very low current ripple. The PWM frequency is 16 kHz. All drive cards are current limited at 20 to
22 amps. They operate from a nominal supply voltage of 160 volts. The peak power output is thus about 3000 watts, or 4
H.P. The continuous power output is, however, limited by a microprocessor based fuse setting, overcurrent shutdown, and
motor thermal protection. Short circuit protection is provided by the drive card and, if sustained for over 0.01 second, the
microprocessor will shut the servo drives off and generate an alarm.
Summary of Contents for VF-SERIES
Page 180: ...1 15 96 96 8100 177 TABLEOFCONTENTS TECHNICAL REFERENCE SERVICE M A N U A L VF SERIES ...
Page 235: ...96 8100 1 15 96 232 VF SERIES S E R V I C E M A N U A L ASSEMBLY DRAWINGS VF 1 COLUMN ...
Page 237: ...96 8100 1 15 96 234 VF SERIES S E R V I C E M A N U A L ASSEMBLY DRAWINGS VF 1 LEADSCREW ...
Page 239: ...96 8100 1 15 96 236 VF SERIES S E R V I C E M A N U A L ASSEMBLY DRAWINGS VF 3 COLUMN ...
Page 241: ...96 8100 1 15 96 238 VF SERIES S E R V I C E M A N U A L ASSEMBLY DRAWINGS VF 3 LEADSCREW ...
Page 245: ...96 8100 1 15 96 242 VF SERIES S E R V I C E M A N U A L ASSEMBLY DRAWINGS 3 4 2 1 ...