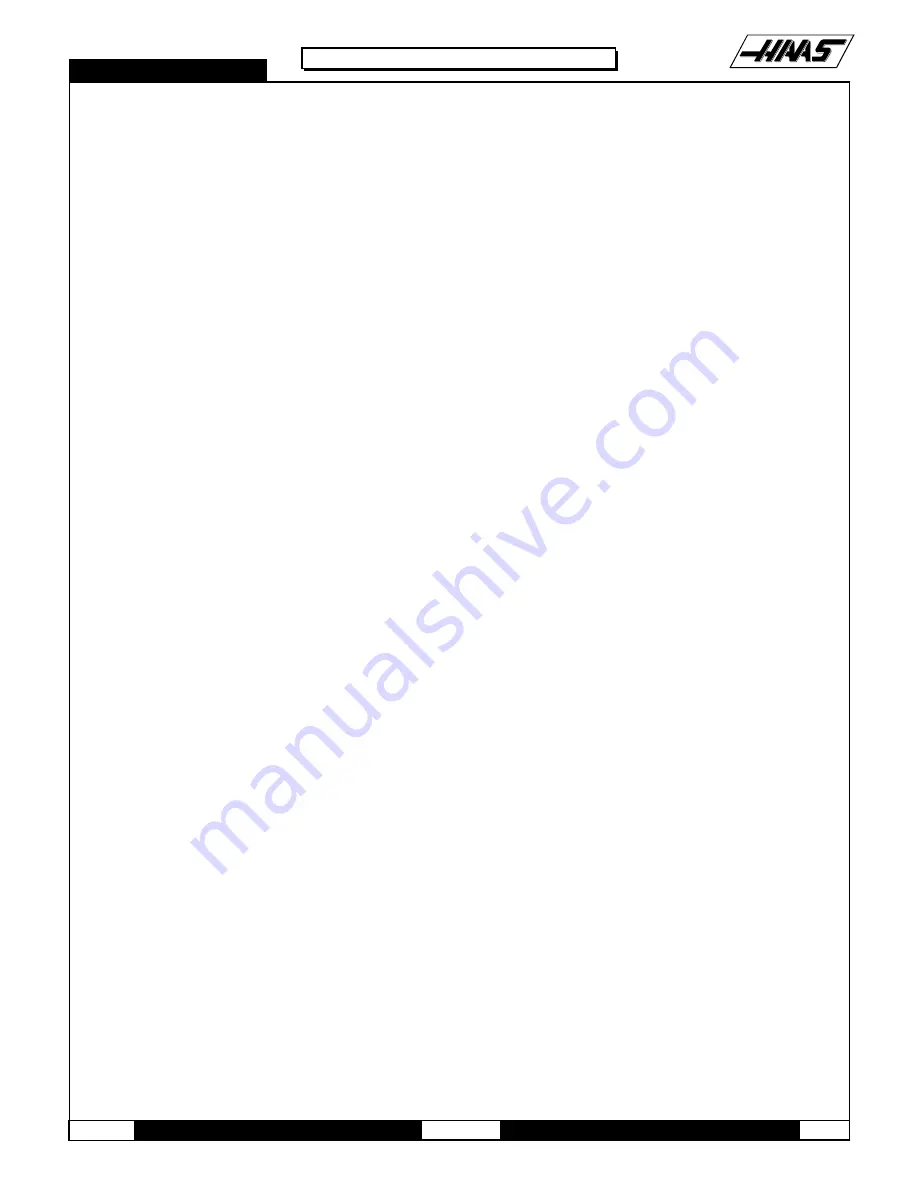
1-15-96
96-8100
159
TABLE OF CONTENTS
TECHNICAL REFERENCE
S E R V I C E M A N U A L
VF-S
ERIES
7. CONTROL PANEL
7.1 JOG HANDLE
The JOG handle is actually a 100-line-per-revolution encoder. We use 100 steps per revolution to move one of the servo
axes. If no axis is selected for jogging, turning of the crank has no effect. When the axis being moved reaches its travel
limits, the handle inputs will be ignored in the direction that would exceed the travel limits.
Parameter 57 can be used to reverse the direction of operation of the handle.
7.2 POWER ON/OFF SWITCHES
The POWER ON switch engages the main contactor. The on switch applies power to the contactor coil and the contactor
thereafter maintains power to its coil. The POWER OFF switch interrupts power to the contactor coil and will always turn
power off. POWER ON is a normally open switch and POWER OFF is normally closed. The maximum voltage on the POWER
ON and POWER OFF switches is 24V AC and this voltage is present any time the main circuit breaker is on.
7.3 SPINDLE LOAD METER
The Load meter measures the load on the spindle motor as a percentage of the rated continuous power of the motor. There
is a slight delay between a load and the actual reflection of the meter. The eighth A-to-D input also provides a measure of the
spindle load for cutter wear detection. The second page of diagnostic data will display % of spindle load. The meter should
agree with this display within 5%. The spindle drive display #7 should also agree with the load meter within 5%.
There are different types of spindle drive that are used in the control. They are all equivalent in performance but are adjusted
differently.
7.4 EMERGENCY STOP SWITCH
The EMERGENCY STOP switch is normally closed. If the switch opens or is broken, power to the servos will be removed
instantly. This will also shut off the tool changer, spindle drive, and coolant pump. The EMERGENCY STOP switch will shut
down motion even if the switch opens for as little 0.005 seconds.
Be careful of the fact that Parameter 57 contains a status switch that, if set, will cause the control to be powered down when
EMERGENCY STOP is pressed.
You should not normally stop a tool change with EMERGENCY STOP as this will leave the tool changer in an abnormal
position that takes special action to correct.
Note that tool changer alarms can be easily corrected by first correcting any mechanical problem, pressing RESET until the
alarms are clear, selecting ZERO RETURN mode, and selecting AUTO ALL AXES.
If the shuttle should become jammed, the control will automatically come to an alarm state. To correct this, p u s h t h e
EMERGENCY STOP button and remove the cause of the jam. Push the RESET key to clear any alarms. Push the ZERO
RETURN and the AUTO ALL AXES keys to reset the Z-axis and tool changer. Never put your hands near the tool changer
when powered unless the EMERGENCY STOP button is pressed.
Summary of Contents for VF-SERIES
Page 180: ...1 15 96 96 8100 177 TABLEOFCONTENTS TECHNICAL REFERENCE SERVICE M A N U A L VF SERIES ...
Page 235: ...96 8100 1 15 96 232 VF SERIES S E R V I C E M A N U A L ASSEMBLY DRAWINGS VF 1 COLUMN ...
Page 237: ...96 8100 1 15 96 234 VF SERIES S E R V I C E M A N U A L ASSEMBLY DRAWINGS VF 1 LEADSCREW ...
Page 239: ...96 8100 1 15 96 236 VF SERIES S E R V I C E M A N U A L ASSEMBLY DRAWINGS VF 3 COLUMN ...
Page 241: ...96 8100 1 15 96 238 VF SERIES S E R V I C E M A N U A L ASSEMBLY DRAWINGS VF 3 LEADSCREW ...
Page 245: ...96 8100 1 15 96 242 VF SERIES S E R V I C E M A N U A L ASSEMBLY DRAWINGS 3 4 2 1 ...