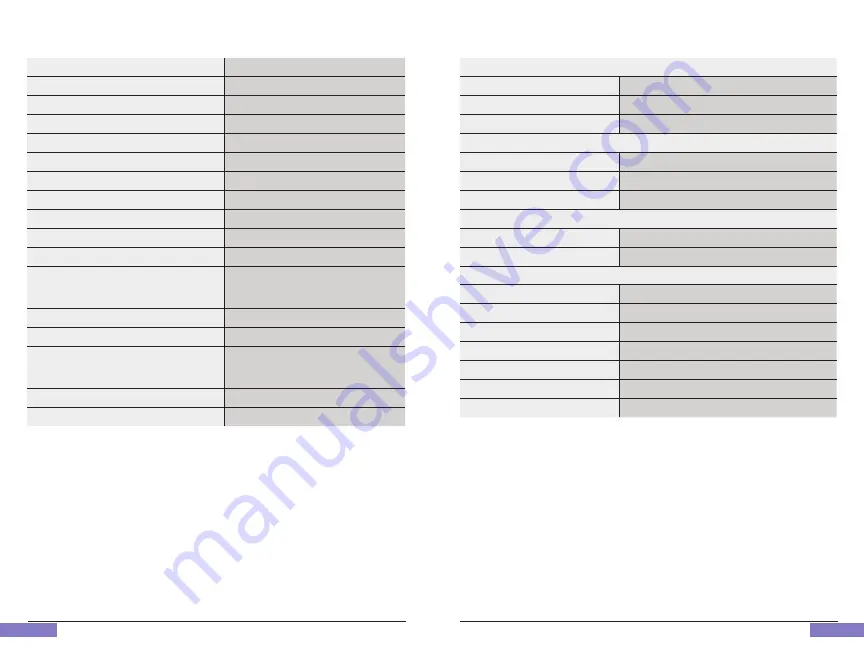
H2flow Controls
ProcessDefender™
71
Technical Data
H2flow Controls
ProcessDefender™
70
Technical Data
9. technical data
Dimensions
See Installation Sheet
Weight
See Installation Sheet
Temperature - operating
-10 to 50°C (14 to 122°F)
Temperature - storage
-20 to 70°C (-4 to 158°F)
Max. Altitude
2000M (6562 feet)
Relative Humidity (non-condensing) Continuous
0-85%
Relative Humidity (non-condensing) Intermittent
0-95%
Over Voltage category (IEC664)
II
Pollution Degree (IEC664)
2
IP / NEMA Rating (Display / HMI from the front)
IP65 / Type 4 and Type 12
Supply Voltage
1 x 100-240VAC or 3 x 200-480VAC
Supply Fuses
Type F, 0.5A Slow Blow with breaking capacity
(1)
of 35A or greater. Fuse voltage must be equal
to or greater than connected supply voltage.
Frequency
50 or 60 Hz
Electronics power consumption
5w
Current Transformers (CT)
ProcessDefender Current Transformers, 10A,
20A, 50A, 100A, 150A, 200A. Up to 1000A
special order.
CT Output
33 mV at Full Scale
Nominal Accuracy (10%-100% of full range)
>99%
Relay Outputs
Breaking capacity
1250VA
Max. Switch Voltage
240 VRMS / 30VDC
Max. Current
5A
Analog Output
Output
4-20mA
Accuracy
>99%
Resolution
0.02mA
Digital Input
Input Voltage
24-48VDC / 24-240VAC
Input Impedance
200k
Ω
Connections
Type
Screw terminals
Wire Type
Copper, solid or stranded
Min. Cable Temperature Rating
65°C (149°F)
Wire Strip Length
6.5 to 7.0mm ((0.26 to 0.28”)
Wire Gauge
0.8mm
2
to 3.3mm
2
(18AWG to 12AWG)
Torque
0.5 to 0.6Nm (4.42 to 5.31 lb/in.)
Approved to
CE, UL, cUL up to 500VAC