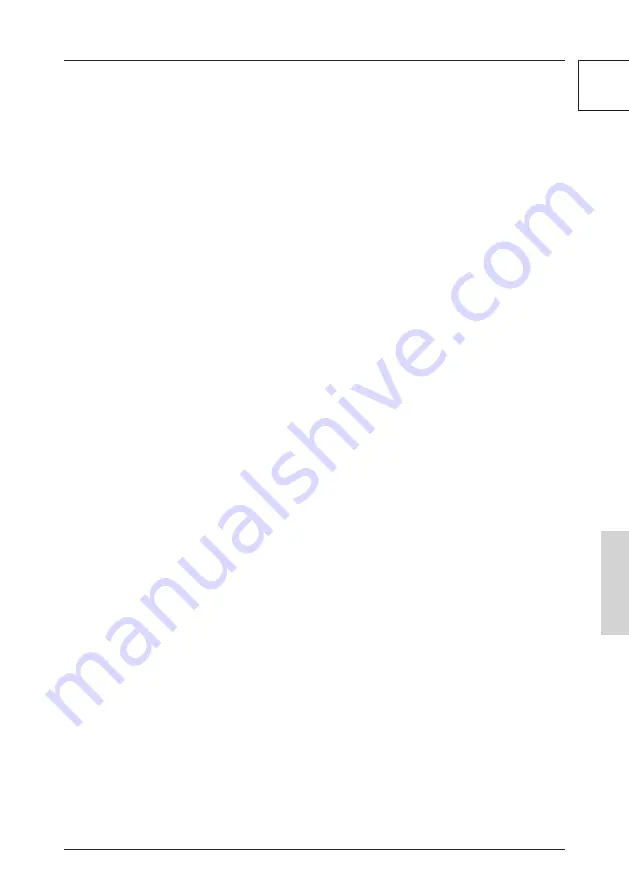
29
GB
Welding cables
Welding cables should be as short as possible,
close together, and should run across or near
the ground.
Electrical bonding
The electrical interconnection of all metallic
parts in and next to a welding machine/cutting
equipment should be taken into consideration.
Metallic parts connected to the workpiece can
increase the risk of the welder receiving an elec-
tric shock from touching these metallic parts
and the electrode at the same time. The welder
should be electrically insulated from all of these
connected metal parts.
Earthing the workpiece
It may be that the workpiece is not already
connected to earth for reasons of electrical
safety or because of its size and location, e.g. a
ship’s hull or steel structures. If so, grounding
the workpiece can reduce emissions in some,
but not all, cases. Ensure that earthing the
workpiece does not increase the risk of accident
for the user or cause the destruction of other
electrical equipment. If necessary, the work
-
piece must be grounded by a direct connection
to the workpiece. In countries where a direct
connection is prohibited, the connection should
be achieved using suitable capacitors, selected
in accordance with national regulations.
Screening
Selective screening of other cables and equip-
ment in the vicinity can reduce irradiation. The
screening of the entire welding/cutting set-up
may be considered for
special applications.
Class A (IEC 60974-10):
If you intend to use the apparatus in residential sur-
roundings supplied by the low voltage mains supply,
an electromagnetic filter may be required to suppress
electrical disturbance to a level where they will no
longer be a nuisance to the user.
The apparatus may be used in industrial or other
areas where power is not supplied by municipal LV
mains.
Class A apparatus are not intended for use in residen-
tial areas where power is supplied via municipal LV
mains, since unfavourable power conditions may cau-
se interference. As a user, you must make sure, after
consultation with your energy provider, if necessary,
that your point of connection on which the machine
is to be operated meets the requirements above.
The user is responsible for faults arising from the
welding.
The extent of that surrounding area that must
be considered depends on how the building
is constructed, and the other activities taking
place there. This area may extend beyond the
limits of the premises
Evaluation of the welding machine / cutting
equipment
In addition to the assessment of the area, the
arc welding machines/cutting equipment can
be evaluated to assess and resolve cases of
interference. An assessment of electromagnetic
interference should include in situ measure-
ments, as specified in section 10 of CISPR
11:2009. In-situ measurements can also be
made to gauge the effectiveness of any minimi
-
sation measures implemented.
Guidance for minimisation measures:
Public power supplies
Welders machines/cutting equipment should
be connected to the public power supply as per
the manufacturer’s recommendations. If there
is any interference, it may be necessary to take
additional precautions, such as fitting filters for
the mains connection. Consider shielding the
mains cable of permanently installed welding
machines/cutting equipment with a metal pipe
or similar. The shielding should be electrically
connected for its entire length. The shielding
should be connected to the welding machine/
cutting equipment power source to achieve
good electrical contact between the sheath
and the housing of the welding machine/cutter
power source.
Maintenance of the arc welding machines/
cutting equipment
Arc welding machines/cutting equipment
should be regularly maintained as per the
manufacturer’s recommendations. All access
and service doors and covers should be closed
and well secured when the welding machine/
cutting equipment is in operation. With the
exception of the changes and adjustments
specified in the manufacturer’s instructions, the
welding machines/cutting equipment should
not be modified in any way. In particular, the
spark gaps of arc ignition and stabilisation
devices should be adjusted and maintained in
accordance with the manufacturer’s
recommendations.
ENGLISH
Summary of Contents for 20078
Page 6: ......
Page 10: ...4 GAS 1 2 3 5 TEST GAS 4 6 l min Ø 0 6 mm 8 l min Ø 0 8 mm 1 1 MIG MAG WIG ...
Page 13: ...7 MIG MAG 3 3 UNI MIG 125 INVERTER MIG MAG MMA WIG ...
Page 14: ...8 2 ON 1 MIG MAG 3 10 mm 4 3 3 ...
Page 18: ...12 3 3 MMA UNI MIG 125 INVERTER MIG MAG MMA WIG 2 ON 1 ...
Page 19: ...13 3 3 1 2 MMA 3 4 UNI MIG 125 INVERTER MIG MAG MMA WIG Art Nr 16982 T I P ...
Page 21: ...15 3 3 WIG Art Nr 41690 T I P UNI MIG 125 INVERTER MIG MAG MMA WIG 4 GAS 1 2 GAS 3 Optional ...
Page 25: ...19 4 4 1 2 3 4 Art Nr 24843 T I P Art Nr 41616 T I P Art Nr 41612 41614 T I P ...
Page 26: ...20 4 4 4 1 2 3 ...
Page 111: ......
Page 112: ......
Page 113: ......