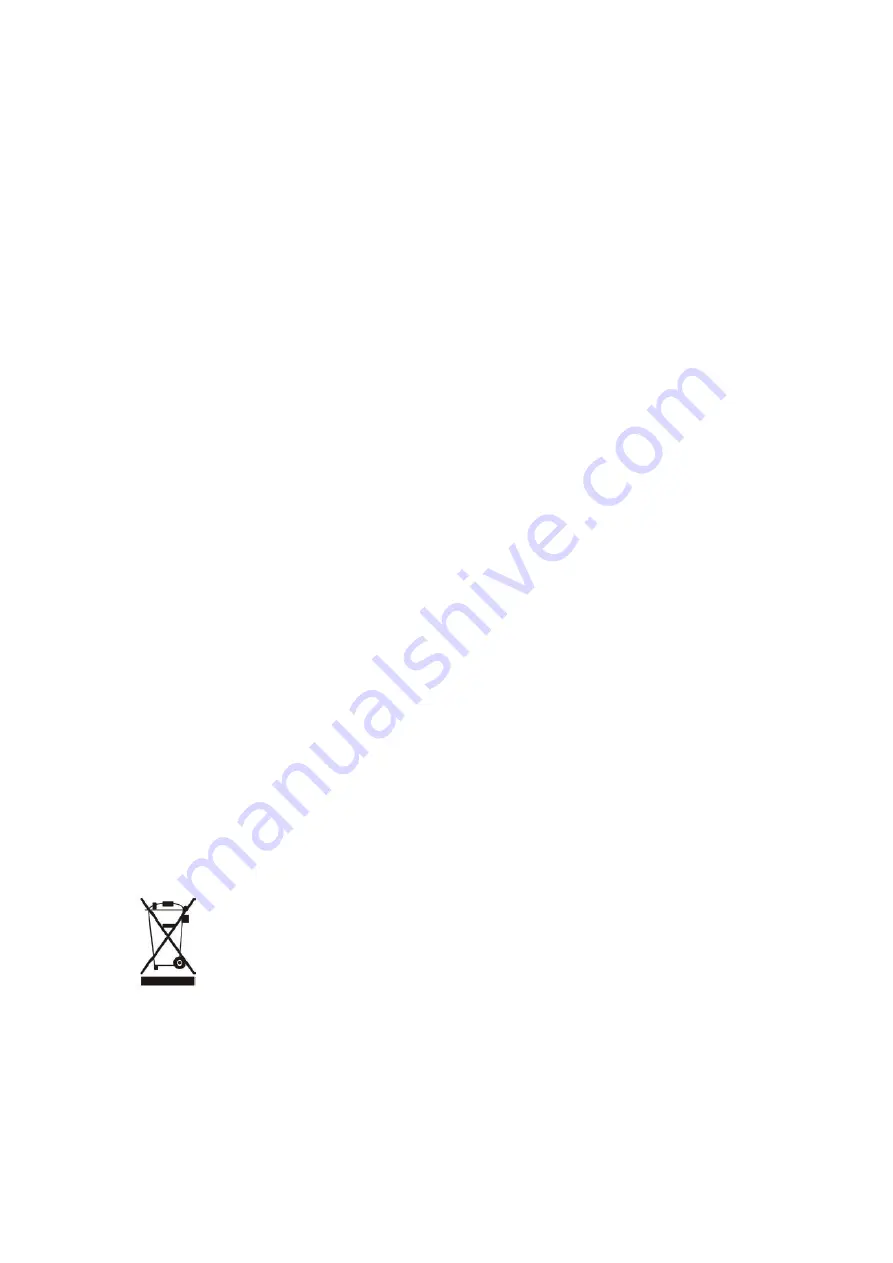
7
The high pressure circuit pipes are made of copper and have a diameter equal to or greater than 1’’5/8. A
certificate as indicated in §2.1 in compliance with standard NF EN 10204 must be requested from the supplier and
filed in the installation’s technical file.
Technical data relative to the safety requirements of the various applicable directives are indicated on the
information plate. All this information must be recorded in the appliance’s installation manual, which must be
kept in its technical file: model, code, serial number, maximum and minimum OT, OP, year of manufacture, CE
marking, manufacturer’s address, refrigerant and weight, electrical parameters, thermo-dynamic and acoustic
performance.
LABELLING
The equipment must be labelled so as to specify that it is out of order and that the refrigerant has been drained.
The label must be dated and signed.
For appliances containing a flammable refrigerant, check that labels are placed on the equipment stating that it
contains a flammable refrigerant.
RECOVERY
When draining the refrigerant for maintenance or decommissioning, best practices should be followed in order to
safely drain all of the refrigerant.
When transferring refrigerant to a cylinder, make sure that you use a recovery cylinder that is compatible with the
refrigerant. Make sure that the correct number of cylinders are provided for recovering all of the refrigerant. All
cylinders used must be intended for the recovery of refrigerant and must be labelled for this specific refrigerant.
The cylinders must be equipped with a vacuum valve and a stop gate in good working order. Empty collection
cylinders are drained and, where possible, cooled before recovery.
The recovery equipment must be in good working order, the instructions for using the equipment must be within
reach and the equipment must be compatible for use with the refrigerant concerned, including, where
appropriate, a flammable refrigerant. Moreover, a set of calibrated scales must be available and in good working
order. The pipework must be complete, have no leaks or disconnected connectors, and must be in good condition.
Before using the recovery unit, check that it is in good working order, that it has been well maintained and that
the associated electric components are sealed so as to prevent any risk of fire in the event of refrigerant being
released. If you have any doubts, contact the manufacturer.
The recovered refrigerant must be sent to the refrigerant supplier in its recovery cylinder with a waste transfer
note. Do not mix different refrigerants in the recovery units, and in particular in the cylinders.
If the compressor has been removed or if oil from the compressor has been drained, check that the refrigerant
has been completely removed to prevent it from mixing with the lubricant. The draining process must be carried
out before returning the compressor to the supplier. Only the electric heater of the compressor body can be used
to accelerate this process. This operation can be carried out safely once all liquids within the system have been
drained.
RECYCLING
This symbol is required by the European directive DEEE 2012/19/EU (directive on
waste electrical and electronic equipment) and means that your appliance must not
be thrown into a normal bin. It will be selectively collected for the purpose of reuse,
recycling or transformation. If it contains any substances that may be harmful to the
environment, these will be eliminated or neutralised. Contact your retailer for
recycling information.
Summary of Contents for HPGI50
Page 2: ......
Page 60: ...58 2 Dimension mm Model HPGI50 Model HPGI60 70 85...
Page 67: ...65 5 Electrical Wiring 5 1 SWIMMING POOL HEAT PUMP WIRING DIADRAM HPGI50 HPGI60 HPGI70 HPGI85...
Page 80: ...78 8 Exploded Diagram 8 1 Exploded Diagram Model HPGI50...
Page 82: ...80 Model HPGI60 70 85...
Page 87: ...85 2 Dimensi n mm Model HPGI50 Model HPGI60 70 85...
Page 108: ...106 8 Diagrama de despiece y mantenimiento 8 1 Modelo HPGI50...
Page 110: ...108 8 2 Modelo HPGI60 70 85...
Page 115: ...113 2 Dimension mm Mod le HPGI50 Mod le HPGI60 70 85...
Page 123: ...121 5 C blage Electrique 5 1 Sch ma de c blage de la pompe chaleur HPGI50 HPGI60 HPGI70 HPGI85...
Page 135: ...133 8 Sch ma clat et liste des pi ces d tach es 8 1 Mod le HPGI50...
Page 137: ...135 8 2 Mod le HPGI60 70 85...
Page 142: ...140 2 Ausma e mm Model HPGI50 Model HPGI60 70 85...
Page 162: ...160 8 Explosionszeichnung 8 1 Explosionszeichnung Modell HPGI50...
Page 164: ...162 Modell HPGI60 70 85...
Page 169: ...167 2 Dimensioni mm Modello HPGI50 Modello HPGI60 70 85...
Page 189: ...187 8 Esploso e manutenzione 8 1 Modello Model HPGI50...
Page 191: ...189 Model HPGI60 70 85...
Page 196: ...194 2 Afmeting mm Model HPGI50 Model HPGI60 70 85...
Page 216: ...214 8 Open geklapt diagram 8 1 Open geklapt diagram Model HPGI50...
Page 218: ...216 Model HPGI60 70 85...
Page 223: ...221 2 Dimens o mm Modelo HPGI50 Modelo HPGI60 70 85...
Page 245: ...243 8 Diagrama Explodido 8 1 Modelo HPGI50...
Page 247: ...245 8 2 Modelo HPGI60 70 85...
Page 252: ...250 2 Wymiary mm Model HPGI50 Model HPGI60 70 85...
Page 271: ...269 8 Schemat budowy pompy 8 1 Widok urz dzenia rozebranego Model HPGI50...
Page 273: ...271 HPGI60 70 85...